Green Series
How food processors can successfully manage water and utilities
Production demands are king, but processors can still find efficiencies

Discharge water is an area that processors need to pay attention to for both efficiency and regulatory concerns, such as phosphorous from antiscalants making its way into discharge water. U.S. Water has developed PhosZero, an antiscalant that does not use phosphorus; this image is of discharge water with no phosphorus.
Photo courtesy of U.S. Water



In an office building, there are all sorts of ways to reduce energy and water usage.
Using daylight and outside air can cut energy and HVAC costs. Aerators on sinks and low-flow toilets can reduce water usage. HVAC set points can be raised to participate in demand-response programs, power strips can be turned off at the end of the day to prevent equipment from still drawing power, and high-efficiency dishwashers in the breakroom can cut down on water usage.
But in food processing facilities, production demands make energy and water efficiency entirely different challenges than they are in other types of facilities, which means processors have to get creative when they’re trying to improve their utilities management, save money and meet corporate sustainability goals.
The office building comparison does apply in one important area: It shows how energy and water have to be thought about differently in food production plants and how processors have to make their case for investments in equipment and training, without being able to take advantage of something, such as new office lighting, having a six-month payback.
There are ways to save energy and water in production, but they are subordinate to production demands and regulatory requirements. While office buildings have to comply with building codes, how complex are those compared to FSMA requirements, other safety regulations and customer demands for production practices that meet certain standards?
“You can’t not get the food up to the kill temperature just to save energy,” says Warren Green, vice president and manager of process engineering for Hixson.
Green considers the steps involved in producing milk.
“It has to start cold, it has to get warmed up, then, if it’s traditional white milk, you’ve got to bring it back down and refrigerate it again,” he says.
All of that takes energy and water, and those demands grow exponentially when you start adding in all the pieces of the production process. That makes energy and water management and efficiency a daunting task, but not an impossible one. Processors have options, and understanding how those options can be taken advantage of is critical to achieving savings in energy, water and the money required by both of those things.
Measure twice, cut (costs) once
You’ve probably heard it a million times, and for good reason: You can’t manage what you don’t measure.
You more than likely apply this concept to all aspects of your production, even if you don’t put it in those terms. You measure how many of a particular product come off of a production line damaged during a run to make sure you’re within an acceptable failure rate. You measure how much capacity you have during peak times and how much wiggle room you have to expand production if necessary. You measure the number of employees you have on a production line, how many hours they work and how few you can get by with if circumstances demand it.
You measure all those things, so that you can manage them, and your utilities should be no different. It starts with looking at your utility bills and asking two questions:
- Why are we spending this much money on utilities?
- What can we do to reduce the amount we spend?
That sounds pretty simple, and it is. But that’s just the starting point for more complex questions, says Steve Tapper, food and beverage industry consultant for U.S. Water. “In most cases, [processors] know water in and water out, and not per their applications,” he says. “Most plants are considerably off what the minimum requirements are and what the maximum requirements are, but they don’t know that, because they don’t have true measurement.”
This applies to energy as well. In both cases, it’s easy to find out the top-line number of how much electricity, water and natural gas you’re using. But how much electricity are your conveyor belts using? How much water are you using for washdowns? How much natural gas are your ovens and dryers using?
When you can answer those questions, then you have information that you can really use to start finding efficiencies. Older equipment was a “black box,” says Phil Kaufman, energy technology manager for Rockwell Automation. You generally couldn’t pull any information from it on how much energy it was using, so you couldn’t break down energy usage by each step of the production process.
Now, each piece of equipment in your plant probably has reporting capability—or, in the case of old machinery, could offer it if upgraded—and all of that data can be evaluated to see how each piece demands resources and how all of those resources add up.
“Whether it’s a machine or a pump or a valve, all of this information now has some sort of energy content to it,” says Kaufman. “So, now you’re getting this information, and the journey is to contextualize it with manufacturing. You went from a black box to a lot of information, and now the information needs context.”
There are a lot of ways to take advantage of that information, and they range from upgrading or maximizing the capabilities of equipment to offering improved training and focus on the operator’s role. But they all start from the point of measurement, says Brett Robison, strategic business leader in food and beverage industry for U.S. Water.
“You’ve got to measure,” he says. “You’ve got to measure quantity, and you’ve got to measure the quality of the water you’re using in each application. Once you do that, then you can look at prioritizing areas of emphasis.”
Perspectives and priorities
Identifying and tackling those areas of emphasis may seem daunting, and it can be overwhelming to think about how many individual components there are in a production plant and how much electricity, natural gas or water each one might be using. But if you start with good data, it becomes a lot easier to make an evaluation of how efficient a process is and how you can improve upon it.
For example, regulations require a certain amount of fresh water to be used per bird processed in poultry plants. Do you have the data on how close you are to that standard? You obviously can’t be below it, but you don’t have to be 25 percent above it. Or if a kill step requires a temperature of 180°F, are you going to 180°F or 181°F, or even higher than that? If you can nail down how close you are to the goals you have to hit, then you can determine if you’re hitting them in the most efficient manner possible. One extra degree in an oven may not seem like a big difference, but start thinking about how much extra energy it requires over an entire production shift, work week, month or year, and it adds up.
Another element of the regulatory aspect is requirements for elements, such as discharge water, especially when it comes to materials in the water. Local, state and federal regulations all require water to contain “less than X” amount of different materials, and ensuring water doesn’t break those rules can require energy investments.
“Things like phosphorus, for example, are getting more and more tightly regulated,” says Robison. “Just because we were able to keep it at 2 ppm for a decade coming out of the plant, maybe it’s going to [hypothetically] be .5 ppm next year.”
Phosphorus is a common ingredient in antiscalants, and many states prohibit any discharge of phosphorus, much less 2 ppm. U.S. Water has recently developed an antiscalant that does not use phosphorus.
Phosphorus discharge is just one example of how the potential for future tightening of regulations is another argument in favor of processing something like discharge water as efficiently as possible. If the regulations are going to tighten, you don’t want to get caught with a process that isn’t efficient and is suddenly costing you huge amounts of money, because you never bothered to evaluate that process.
So, the first step is ensuring that you’re hitting your required targets as efficiently as possible. The next is taking a look at your processes from both a big-picture and a detailed perspective to see if there’s anything you can do to improve their overall efficiency, and not just saying, “We’re meeting regulations, so we’re good.”
From a big-picture perspective, you can start with things such as whether you can shift some of your production to a different time of day. Peak demand hours put a lot of strain on the grid and result in big charges on your electric bill, so can you schedule a production run for second or third shift? Or, if you can’t do that, can you find other ways to trim down your energy usage during peak hours?
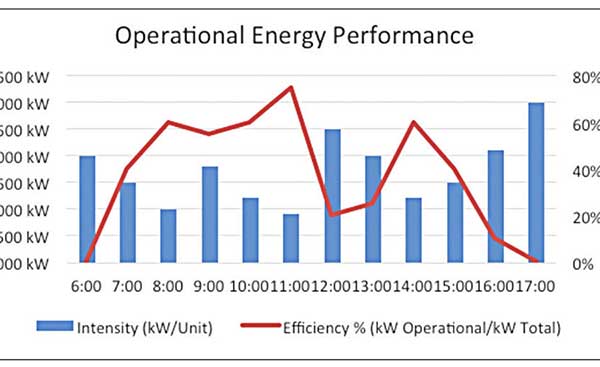
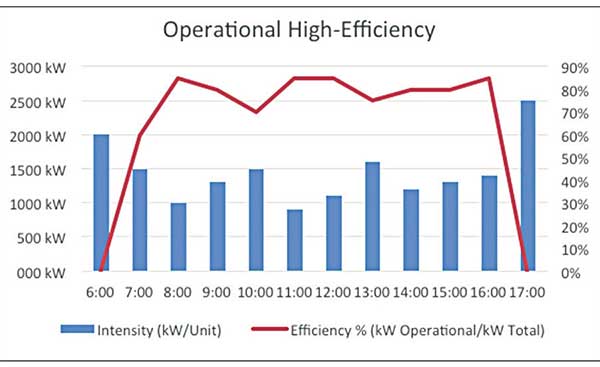
Two charts from a Rockwell Automation white paper showing the difference between a manufacturing operation with large efficiency swings and one that is focused on high- efficiency operations.
Charts courtesy of Rockwell Automation
Your utility and your machines will both offer you data to help evaluate your peak usage. The machines can tell you how much you’re using in each part of the process; the utility can tell you how much your usage during those times is costing you. Getting hit with a big demand charge for a spike in usage during peak hours can cost literally thousands of dollars.
“Just cognizance and knowledge that those charges are out there is kind of like step 1, and step 2 is ‘Is there really something that we can do substantively in our day-to-day operations?’” says Hixson’s Green. “Some just don’t have that luxury, and others might have a little bit more float in their schedule where they can shift things.
“But from a manufacturer’s perspective, if they’ve got a shipment, and they’ve got to make product, they don’t let a demand charge get in the way. Production is king, and they’ve got to be able to make product when they need to make product.”
One equipment-based solution that can help is variable speed drives and motors. Having to start a motor from 0 to 100 percent during peak time is a budget buster. Ramping up a variable speed drive that’s already running or only having to start a motor from 0 to 20 percent is a whole lot more efficient and will cost a whole lot less money. By having variable speed equipment available, you can meet production needs or sudden increases in required capacity while still having some level of control over the cost of doing so.
Another possibility is taking advantage of the off hours for things, such as ice building, even if you can’t shift production. By making ice at night, during times of lower demand, you can use it during the day to help cool without having to make it on the fly.
Investing in efficiency
New equipment can offer huge advantages in terms of not only the information it can provide, but in its operating efficiency. But that leads to a bit of a conundrum for food processors: If you’re buying a piece of equipment that has an expected lifespan of 15 or 20 years, will it still be efficient as it approaches the end of its service time?
The answer, as it so often is, is “maybe.” A big capital investment now might be top of the line in terms of efficiency, then be outdated halfway through its expected lifespan. Unfortunately, there’s no way to predict whether that will be the case, so processors have to be willing to take that risk.
Even if a big capital investment means sacrificing some efficiency opportunities down the road, there are other ways to still get the most out of your production process overall. A dryer may last 20 years, but other components of the production line may not, so they can be replaced with more efficient options as they reach the end of their operating life.
All of that means that processors need to do as much as they can up front to be sure that they’re getting a piece of equipment that can help them hit their efficiency targets over a reasonable timeframe. Data is a huge part of that, of course, and having more of it available helps make the business case for spending more up front to maximize long-term savings.
When making the case for upgrades, large or small, processors can take some steps to increase their chances of approval. The one that comes to mind for most people is being able to show a relatively short payback, because as more people become familiar with efficiency and sustainability initiatives, they become more open to the idea of “pay more now, but save much more over time.” When the people making the financial decisions are open to that idea, then having a projection backed by data makes it an easier sell to spend more money up front.
“People are still trying to make good business decisions, but they’re trying to get a little more data-driven in their decision-making,” says U.S. Water’s Robison. “You might walk into an old, old plant, but they’ve got five new pieces of equipment that they just invested millions and millions of dollars in. Well, sometimes, you’ve got to work with what you’ve got; sometimes, you may have to put a plan together to say, ‘This is somewhere where we might want to look at investing capital at some point in time, because here’s the payback.’”
Operational efficiency
Equipment, data collection, measurement and strategy are all important, but any or all of them can be ruined by inefficient operations. To go back to the office building example, giving employees access to the thermostats may cut down on complaints, but it probably won’t do your heating bill any favors.
A similar concept applies to plant operations. Automation and controls can help by managing elements of the process efficiently, but operators need flexibility to do their jobs. To keep that from ruining your best-laid plans, you need to evaluate how operators do their jobs not only from a production-efficiency standpoint, but from a resource-efficiency standpoint as well, says Kaufman.
“Every operator’s different,” he says. “Even though there’s a lot of automation, everybody sets up and tweaks things differently. We find different operators are very good at their job, and then we find out ‘oh, they leave everything on over lunches,’” which wastes energy.
“We want everybody to be like Joe [as an operator], but when we look at the energy, we want everybody to be like Nancy.”
Training is key to making sure your operators are imitating the best parts of both Joe and Nancy. Operating-efficiency training helps make sure that they aren’t wasting time or resources by adding or duplicating steps, and energy-efficiency training helps make sure they understand when to shut down equipment or take other steps to ensure resources aren’t being wasted.
Also, make sure your documentation of operating procedures includes energy aspects.
Processors that put in the time and effort to operate efficiently will see real results in terms of meeting goals and regulatory requirements.
For more information:
Hixson, www.hixson-inc.com
U.S. Water, www.uswaterservices.com
Rockwell Automation, www.rockwellautomation.com
Looking for a reprint of this article?
From high-res PDFs to custom plaques, order your copy today!