Plant Construction Survey
Food Engineering’s 43rd Annual Plant Construction Survey
COVID-19 overshadows project planning and construction while decreasing already short labor supplies

Like Monty Python’s famous “Nobody expects the Spanish Inquisition,” certainly no one expected—at least way back on New Year’s Day 2020—the coronavirus (aka COVID-19) would come out of seemingly nowhere and close down so much of the world’s economy, while inflicting such a great global toll on human lives. But, COVID-19 has tested our industry and its supply chains, and we’re learning about the industry’s resiliency in the process.
A few days after New Year’s, I prepared the 2020 survey questions for this article, thinking we had a pretty good economy during the last year. And we did. There were already supply chain changes on the way, spurred by the market for home deliveries of high-end meal kits and grocery store deliveries (e.g., Giant/Peapod), and with Amazon’s purchase of Whole Foods, there was a trail to be blazed in home deliveries. Little did we know, however, just how well this new home delivery market concept and the food supply chain in general would be tested as we stayed at home in quarantine.
Article Index:
COVID-19 and its impact on plant construction
While this year’s number of 609 projects for calendar year 2019 in FE’s Plant Construction Survey (new and expansions/renovations) follows a small, incremental downward trend over the last four years, it’s difficult to know how much COVID-19 has affected the reporting this year. We’ll look into the numbers in more detail a little later after we explore some of the trends—especially coronavirus—related by the A&E/Cs for this article. Keep in mind that many of the responses from A&E/Cs in this article reflect business before COVID-19 took hold on our economy.
Depending upon where your business is located, COVID-19 has had different impacts. “Due to COVID-19, some project sites are being closed due to government mandates, and other projects are being delayed,” says Don Oberlies, VP/market leader, Alberici Constructors. “Equipment deliveries from other impacted countries are also adding to the delays.”
In Pennsylvania, where I live, what’s considered an essential business and what’s not in the COVID-19 environment isn’t always so clear, but the outbreak has hurt construction.
“In Pennsylvania, the deeming of construction as non-life essential has hurt construction projects across the board,” says Mark Galbraith, co-owner of Galbraith Pre-Design Inc. “Other than maintenance (in order to keep facilities in compliance with food safety regulations), projects are shut down. This includes one of our sizeable projects, which halting progress may affect the producer’s ability to meet demand or merge into new products and markets once the nationwide quarantine is lifted. It is also affecting the entire supply chain. In Pennsylvania, dairy farms have been forced to dump raw milk down the drains.”
For Epstein, Darrin McCormies, senior VP, director of industrial services, reports that since the emergence of the COVID-19 pandemic, projects in the food industry have continued with no slowdown in expected completion dates. He also says his firm has taken on cannabis projects as there have been several new companies anticipating the widespread growth of the cannabis industry.
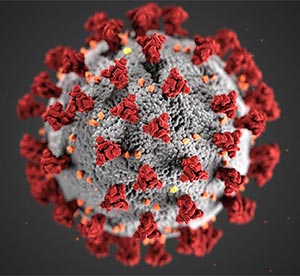
At the time of writing this article, due to COVID-19, we’ve seen the closure of four Smithfield facilities in the U.S., several Tyson operations and a couple of JBS plants, putting a crimp on the protein supply chain. The supply chain for construction materials, however, has not been quite as affected, but finding labor remains a perennial problem.
For example, Forrest McNabb, executive vice president of Big-D Construction, reports that while the availability of construction materials has remained surprisingly stable over the last year, the labor situation remains stressed due to a very low unemployment rate in the construction business. And he adds, “While dealing with that, we then have COVID-19 arrive and there are some immediate impacts in managing projects to assure the safety and health of the labor force.”
McNabb, an industry veteran, describes something all too familiar. “It is the first time in my career that we are having to do week-to-week strategic planning based on the unknowns in dealing with COVID-19 versus our actual short-term and long-term strategic planning. We are optimistic ‘this too shall pass,’ but it is all hands on deck with weekly meetings, making sure we are very proactive in maintaining best practices with our people and projects to stay out of harm’s way.”
“The pre-COVID-19 economy, as we all know, was strong and vibrant, marked by record low unemployment and widespread resource constraints across the trades, project and construction management and engineering professionals,” says Gregory Franzen, Faithful+Gould agrifood subsector lead. “Yet to be seen is the resilience of our industry to adapt to the new complexities presented to us with COVID-19.”
The future is a little nebulous for some processors. “Construction projects were going strong, and the outlook for the year looked great before COVID19 became a pandemic,” says Matt Hartenstein, P.E., mechanical engineering manager, Mechanical Process Group, Shambaugh & Son. “Now the outlook is unclear as companies are slowing down and/or putting projects on hold.”
While the coronavirus may not have adversely affected the construction goods supply chain, it has had an impact on planning and lead times as Franzen summarizes risks and challenges:
- Adapting to different safe work practices on projects in a fully operational plant environment.
- Planning for lead time impacts to process and other equipment manufactured overseas.
- Learning how best to engage on-site differently, respecting social distancing requirements, meaning the way we meet and engage on-site about projects may change.
While there are apt to be delays in project planning, spending and construction scheduling, some A&E/C folks are, however, thinking positively with a good end in sight. Says Lloyd Snyder, Woodard & Curran senior VP, “Pre-virus, the spending was increasing. I think this pause in spending will end with a surge not seen since the end of WWII. Manufacturing will have a renaissance.”
“Despite being inundated with concerning news on a daily basis, both from a global health and a global economic standpoint, food and beverage processors, for the most part, seem to be galvanizing around their role as essential businesses and vital components of maintaining the safety and survival of the populace,” says Mark DiGino, director of business development, E.A. Bonelli + Associates. “It hasn’t been easy to adapt to rapidly changing conditions, but we are picking up on more optimism than pessimism … Site visits for design and contracting personnel have obviously been halted, but we’ve found that even that has done little to stop our clients from proceeding with plans that had been in motion prior to any ‘shelter in place’ or ‘safer at home’ orders.”
What the numbers say about 2019
The numbers reported this year by A&E/Cs reveal a couple of interesting trends in calendar year 2019. First, the state of new projects remains healthy, especially considering new warehouse and distribution center (DC) projects to support our growing, online shopping habits—given a shot in the arm by the coronavirus keeping us home and not shopping in person or eating at restaurants. In addition, several A&E/Cs reported an increase in pre/wastewater treatment projects and new process plant construction as some older facilities are beyond upgrading. More on this later.
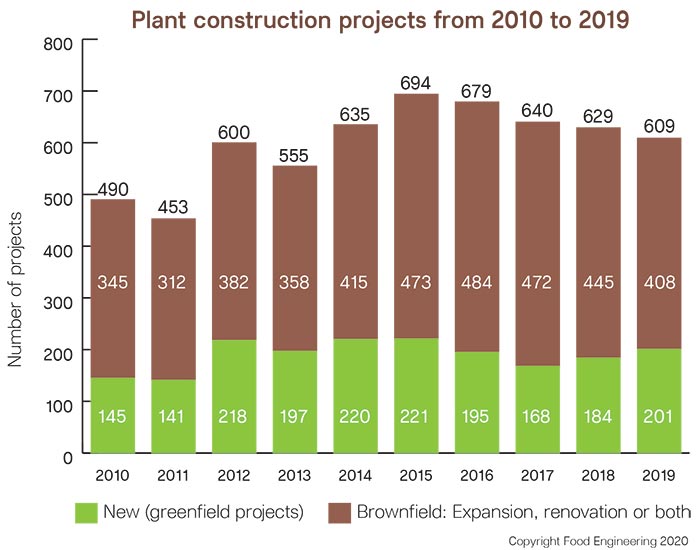
Click image to enlarge
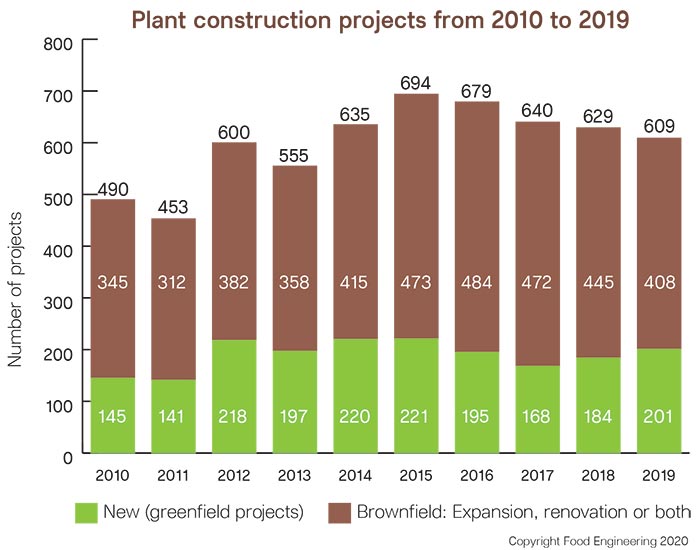
While the 2019 total number of reportable food and beverage plant projects (expansions, renovations, new or combination thereof) totaled 609, the number was down the 2018 total of 629, representing a 3.2% drop. However, 2019’s number of new projects (201) showed an increase of 9.2% over 2018’s number of 184. In addition, though the number of recorded 2019 DC/warehouse-only projects (100) was smaller than the previous year’s 123 projects (a 10-year high), DCs and warehouses still accounted for 16.4% of total projects, whether renovations, expansions or new projects. Compared to 2018, the 2019 number was down by 18.7%, but still 53.4% higher than the 10-year average of 65.2 units.
Reportable food and beverage projects are those valued at over $1 million. They have been made public by the processor, a government entity (including local or state economic development groups), or the A&E/C firms responsible for them. The survey (though the table lists “Completion Date” at the header) includes projects begun, announced by any entity or completed in 2019. If dates listed are beyond 2019, they reflect the projected completion date for a project either announced in 2019 or underway in 2019. Projects that appeared in last year’s table with a 2019 date were carried over—unless there was an obvious duplicate. Keep in mind, some projects can be announced, then dropped at the last minute for any number of reasons, e.g., legal problems, lack of expected funding, site issues, changing needs, politics, etc. In the table, “D/W” refers to distribution/warehouse, and “DC” refers to distribution center; “Exp.” refers to expansion and “Ren.” is for renovations, and some projects include both.
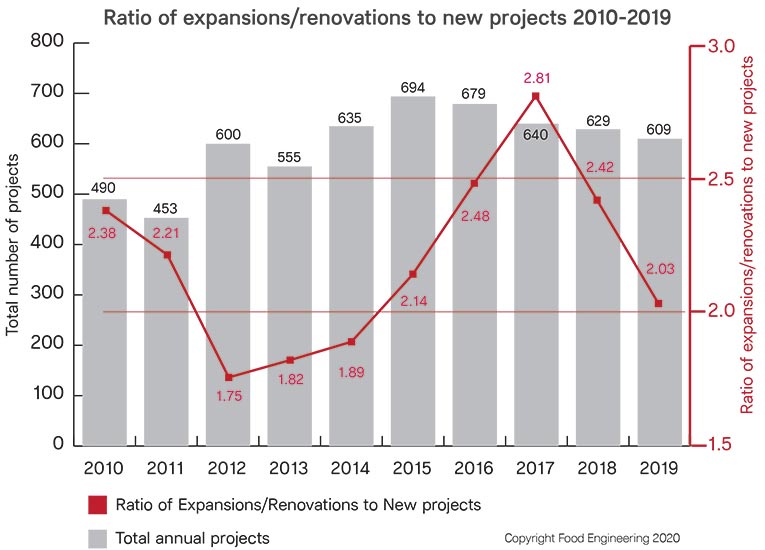
Click image to enlarge
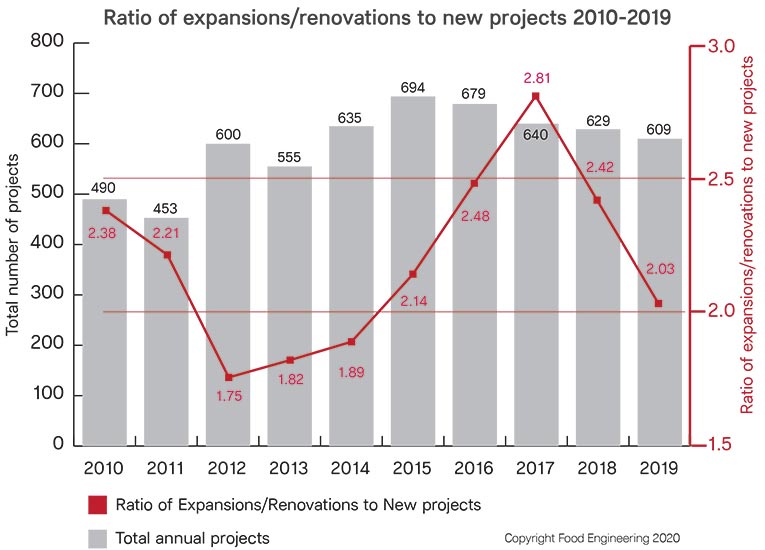
A more detailed look at the numbers shows pet food projects numbered 23 out of 609, and alcoholic beverage projects numbered 41, down 25.5% from 55 projects in 2018. The total number of projects at 609 represents a 1.8% increase over the 10-year average of 598.4 projects. New projects for 2019 (201) showed a 6.3% increase over the 10-year average of 189, while expansions and renovations (408) showed a 0.3% decline over the 10-year average of 409.4 projects. Also interesting is that this year’s ratio of expansions/renovations to new facilities has again dropped since 2017, when the ratio was 2.8:1, the highest in the last 10 years. That ratio declined to 2.03:1 in 2019, indicating an increasing number of new projects.
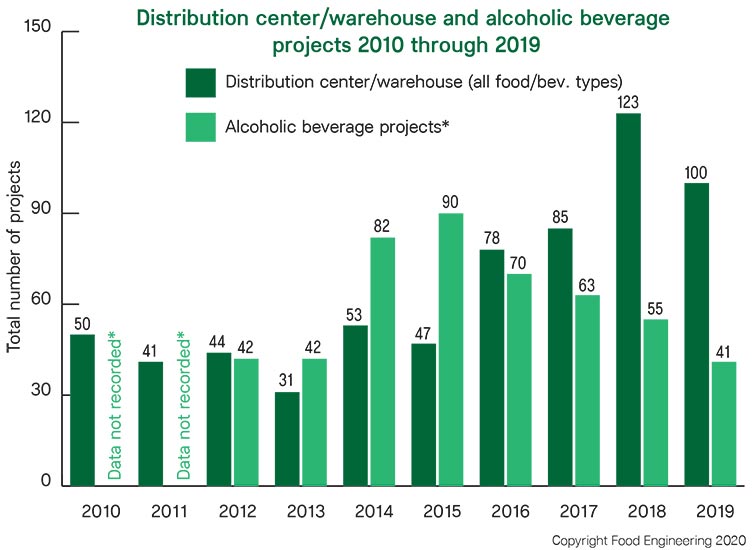
Click image to enlarge
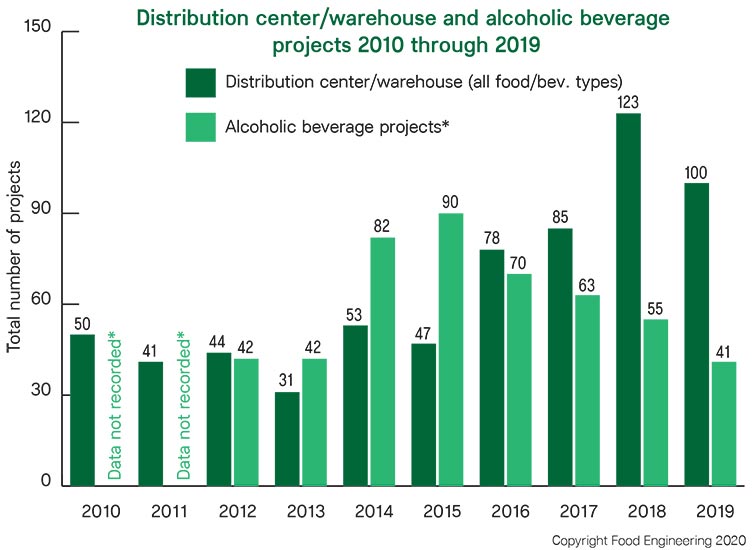
Labor creates compound issues
Even before the emergence of COVID-19, there was an industrywide labor shortage. “Construction employment opportunities are at an all-time high, but the number of new entrants into the workforce continues to steadily decline each year,” says Heath Catt, Construction/Design-Build Group, Burns & McDonnell. “Widespread labor shortages are not limited solely to field construction. This trend is also taking its toll on suppliers and fabricators, affecting shop production levels and driving up the prices of manufactured equipment.”
Like suppliers and fabricators who’ve automated to be more productive, construction is beginning to require more technical skills than needed to run a backhoe. The typical construction worker is now required to be smarter and more technologically savvy than ever before, says Brian King, A M King president. “As more automation, robotics and software applications impact how structures are built, the individuals operating this equipment and technology must also be better trained and more proficient. The future construction worker will spend more time operating a machine than operating a tool.”
With the general improvement of the economy, ongoing deregulation and renegotiated trade agreements by the current administration, the volume of project activity has taken off, resulting in labor availability issues and material cost increases, says Jens Ebert, SSOE Group principal division manager. “The market conditions have been driving owners to accelerate project delivery schedules in an effort to get in front of further constraints and rising costs.” Unfortunately, says Ebert, to cut costs clients increasingly push for projects with lower levels of engineering definition.
Sadly, this labor shortage can have unintended consequences on smaller projects. David Ziskind, Black & Veatch director of engineering, NextGen Ag, says, “In the construction sector, with record employment, finding qualified/skilled labor is a challenge for contractors, and many contractors are adjusting their bids to favor larger projects—in some cases making it difficult to accurately estimate and even source smaller projects.”
Scheduling issues before COVID-19
There seems to be an adequate supply of materials and labor for projects, but you can’t forget about labor, says Mark Redmond, PE, president of Food Plant Engineering. “There is no overcapacity, so it takes prior planning to line things up for any given project. The supply chain does not allow for immediacy.”
“Due to the good economy we are challenged with finding quality subcontractors,” says Tamara Zupancic, director of marketing for The Austin Company. “Clients are not revising their schedules, so we are being more creative in our approach to meet client requirements.”
Carefully planned, projects can go on time and budget. “The lead times on materials and equipment are becoming slightly longer,” says Tammi McAllister, CRB associate, core team leader. “The increased lead times are something we can account for as long as we know and can plan for them.”
“Based on the size of projects, we are looking at subcontractors that can handle those projects and beginning discussions with them early to incorporate them as part of the team,” adds McAllister. “If we don’t engage subcontractors early, we run the risk of projects being delayed. Clients understand the market but look to us to manage the risk and keep them on schedule.”
Today, processors expect A&E/C firms to take on a co-leadership role in and contribute accountably to a deliberate process of achieving the fastest, safest, most economic start-up, says Tom Wiersma, independent A&E consultant. Most clients have the experience to anticipate and build into their thinking the impacts of a tight labor market and the bottlenecked availability of some fundamental building materials. Therefore, to get started on the right foot, most food processors are more comfortable than ever with engaging a preferred architectural and engineering firm or AEC mobilization consultant early in the pre-project programming and scope phases.
Top 10 A&E/C Hot Trends
- Increasing production to meet demand
- Food safety: FSMA regulations/GFSI (design, layout, etc.)
- Capital availability
- Automation: process control, robotics, packaging, etc.
- Overall cost/controlling costs
- Fast project deployment
- Flexibility in plant design to accommodate flexible manufacturing
- Ability to easily manage subcontractors
- Old plant vs. build new — often easier to build new than upgrade
- Workplace safety
*Last three tied with same score
Top 10 Hot Trends A&E/C firms say are of most concern to food processors
- Food safety: FSMA regulations/GFSI (design, layout, etc.)
- Capital availability
- Fast project deployment
- Flexibility in plant design to accommodate flexible manufacturing
- Increasing production to meet demand
- Workforce availability (line workers)
- Overall cost/controlling costs
- Automation: process control, robotics, packaging, etc.
- Ability to change design when building
- Workplace safety
*Nos. 4, 5 and 6 tied with same score
Prefab and modularity aid plant construction
To help compensate for labor shortages and simplify construction, many A&E/Cs have been using a well-established practice that is commonplace today. The modular approach—much like pre-manufactured homes—is to build skids or ready-to-go equipment in a modular section, for example, a “CIP skid.” Just like modular electronics, these sections are plugged in and wired at the plant and are quickly operational, as they’ve already been built and tested at the shop.
With the current set of 3D design tools and today’s automation equipment and simulation software, more prefabrication can be done off site, says Harlan VandeZandschulp, P.E., president of Gleeson Constructors & Engineers LLC. Offsite design and prefab at an integrator’s or machine builder’s location can help keep labor costs down and decrease the need for more skilled people at the construction site when they’re already hard to find.
This modular approach isn’t just for automation or process equipment. “Whether modularizing building components, pipe racks or equipment skids, this prefabrication technique executes work in a more controlled environment,” says Catt. “This decreases risks to productivity, eliminates other potential negative impacts, and creates an additional work front. In many cases, modularization helps lower overall construction costs while improving quality and schedule.”
“Office and utility areas of manufacturing facilities are prototypes for modular construction, but we are beginning to see more activity in all areas,” says Keith Perkey, VP—Food & Beverage Division, The Haskell Company. “We are also beginning to see more use of technology throughout the construction process. Augmented reality is being used for field quality checks to match design models to field installation; sensors are being deployed in the construction materials and the construction workforce to improve both quality and safety.”
New plant construction vs. expansions and upgrades
Food processors are raising the need to respond to consumer demands and are looking to increase production, change technologies and meet food safety regulations, says Tyler Cundiff, VP, business development—food and beverage market, Gray. When possible, they want to reallocate existing space and make modifications. But sometimes, mods/upgrades to existing facilities may not be practical.
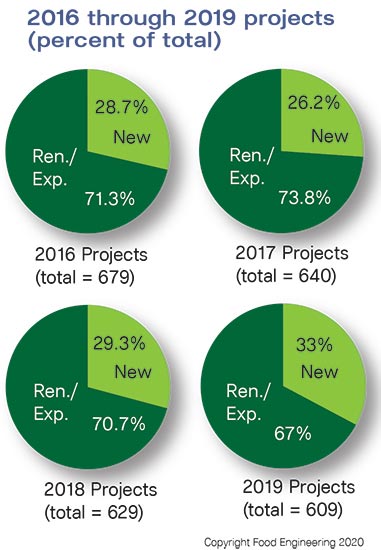
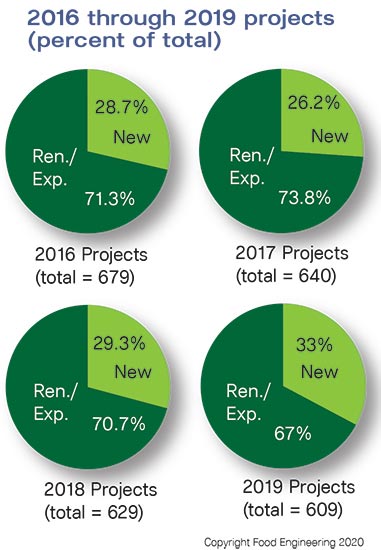
Our survey found an increase in new projects in 2019. Can you feel the frustration of an older facility? If you have an aging warehouse or plant, you have to ask: Is it providing the capacity, performance and efficiency you need to make a profit today? Twenty years ago, it may have been sufficient, and now you wonder if it’s just not worth applying bandages anymore, especially with limited capacity and flexibility, “head knockers” and ancient automation equipment. Is greenfield a viable solution?
“Clients are finding that the cost of upgrading/renovating their facility is not that far off from building new,” says Luke Waite, ESI Group USA regional manager. “They find they may have antiquated equipment or mechanical systems—or that current operations do not meet food safety requirements—that have to be updated, which can significantly drive the cost of an expansion/renovation project up.” A new facility allows clients a clean slate, so to speak, to meet the updated food safety requirements for product/people separation as well as sanitation, limiting any possible interruption of their existing production while meeting consumer demands, says Waite.
If you’re a homeowner, you may have encountered this little “surprise” when you decide to renovate or upgrade, but on a plant-size scale, the added costs of bringing everything “up to code” gets pricey real fast. “When tackling renovations, companies are finding that upgrading plants requires upgrading to modern regulations and standards,” says Chris Jarc, P.E., vice president and manager of project management, Hixson Architecture & Engineering.
“If you are renovating an older plant, you are now required to consider accessibility (ADA) issues like employee welfares, path of travel and toilet facilities,” says Jarc. “Additionally, energy codes have become more restrictive, and building officials are requiring the new codes be followed: There is no “grandfathering” anymore. A 4,000-sq.-ft. renovation may end up requiring an additional 10% to 20% in costs to retrofit all of the regulatory-required items.”
Warehouses, distribution centers key to today’s online world
Changing consumer preferences certainly have had an impact on Haskell’s projects, says Perkey. In many cases the core production operation remains the same, but the packaging options and the warehouse and supply chain elements of the projects have changed to meet the current consumer demands. “Overall the volume of warehouses and fulfillment center activity has been strong and we certainly have seen increases in project opportunities in this arena,” says Perkey.
“Customization and personalization are merging to give consumers very real ways to get products they want,” says Woodard & Curran’s Snyder. The rise of Amazon has created demand for fast, efficient delivery. Big box stores have also survived and thrived. Mega food processors like Kellogg and Campbell are trying to find their niche in the changing retail supply chains. To achieve this supply chain flexibility requires complex warehouse operations that are in need of automation and ERP integration, says Snyder.
E-commerce is playing a major role in the design and construction of distribution facilities, says Steve Tippmann, executive VP for the Tippmann Group. These facilities have larger footprints, and owners are trying to locate them more in urban sites, closer to where the population is, because deliveries now are expected in a day or less. “The demand for cold storage is very high,” adds Tippmann. “It’s hard for manufacturers to find storage space across the country, so now they’re starting to build new cold storage projects attached to their manufacturing plant, while cold storage providers are expanding more frequently.”
“We have worked with many clients who sell directly to the consumer. This is definitely fueled by companies like Amazon who have the capability to take on the distribution of products if suppliers can get a substantial amount of product to their facility,” says Jennifer Redmond, marketing director of Food Plant Engineering. “This system affects warehouse needs because suppliers are increasing the frequency of shipments rather than requiring longer-term storage.”
Wastewater treatment as important as the food process
Do you call the addition of a wastewater pretreatment or treatment facility to a processor’s campus new construction or an expansion? If one doesn’t already exist, adding one is certainly new, and while more money can be spent for an on-site wastewater pretreatment center than a food processing line expansion, it certainly qualifies for a table entry on our yearly construction survey. In fact, Matt Williamson, director of engineering at ADF Engineering, says that on-site wastewater treatment continues to be a strong driver of capital spending.
“The majority of our greenfield projects have been faced with difficult site challenges, including wetlands, poor soils and lack of existing utility infrastructure,” says AM King’s Dan Crist, VP of operations. “Many food processing facilities are being designed and constructed with on-site wastewater treatment due to inadequate offsite utility infrastructure and/or local AHJ (authority having jurisdiction) requirements.”
And when a municipality has an existing wastewater requirement specification, it’s not uncommon for the municipality to set higher standards when it realizes that it can’t any longer handle the wastewater it’s getting. Alberici’s Oberlies is seeing an increase of wastewater projects as municipalities place new demands on wastewater that existing pretreatment facilities can’t meet without upgrades.
For a processor with a lot of wastewater, Black & Veatch’s Ziskind says the use of digestion technologies provides a triple win. A manufacturer can hit the trifecta of reduced wastewater costs, water reclamation and energy generation. What’s not to like about that? Smithfield Foods has been doing this for some time.
To be continued
While we’ve looked at the key issues—including COVID-19—facing food processors and A&E/Cs this year, there’s a lot more to cover. Be sure to watch for a follow-up story online where we will cover other design criteria and issues including FSMA, site-related issues beyond wastewater (such as weather and flood plains), trends in automation, and supply chains.
The following companies and individuals participated in the Food Engineering Survey:
ADF Engineering, Inc.
www.adfengineering.com
E.A. Bonelli + Associates Inc.
www.eabonelli.com
Shambaugh & Son L.P.
www.shambaugh.com
ARCO National Construction
www.arconational.com
ESI Group USA
www.esigroupusa.com
Stellar
www.stellar.net
Black & Veatch
www.bv.com
Food Plant Engineering LLC
www.foodplantengineering.com
The Haskell Company
www.haskell.com
Burns & McDonnell
www.burnsmcd.com
Galbraith Pre-Design Inc.
www.gp-inc.com
Tom Wiersma,
independent consultant
616-293-3411
CMC Design-Build Inc.
www.cmcdesign-build.com
Gleeson Constructors & Engineers LLC
www.gleesonllc.com
Tippmann Group
www.tippmanngroup.com
Dean Snyder Construction
www.deansnyder.com
Hixson Architecture & Engineering
www.hixson-inc.com
For further reading: Factors in Plant Construction
Looking for a reprint of this article?
From high-res PDFs to custom plaques, order your copy today!