Engineering R&D
New desiccant technology uses ceramic material
Loose beads are no longer required for compressed air systems

Cutaway image of the Cerades dryer shows structured, straight tube nature of the material.
Photo courtesy of Atlas Copco
Most likely you have a compressed air system in house with the usual desiccant—typically activated alumina or silica gel. While these materials work well initially, their drying performance decreases over time. This can compromise air quality, which means more maintenance. Another issue: as loose desiccant decomposes, it releases dust into the system, requiring additional filtration and maintenance—and increased maintenance costs.
Atlas Copco has recently come up with a more durable and effective, patented solution called Cerades. Its ceramic desiccant material consists of several small structural ducts, which compressed air passes through freely, with a low pressure drop. For this reason, energy costs are lower when using a dryer with this desiccant. Cerades provides users with ISO 8573-1:2010 class 2 air purity for particles without additional filters.
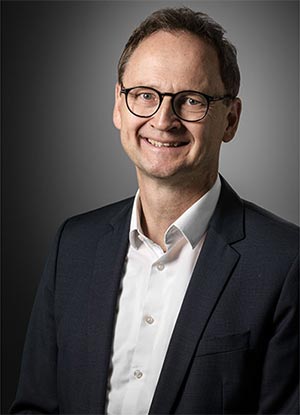
I asked Jan Norz, product and business development manager air treatment, Industrial Air Division, to explain how this system works.
FE: How long has this desiccant been in development? Who are the inventors/developers?
Jan Norz: Our original mission was locating new materials to absorb humidity. In 2016, after years of testing, the R&D team had its first breakthrough. Our new mission became bringing this idea to the market with benefits not found in a conventional desiccant dryer.
At inception, there were only a handful of Atlas Copco employees working on the project. After filing for the patent in 2018, the team working on the invention was expanded to include several engineers.
FE: How does Cerades differ from conventional desiccants?
Norz: Cerades is the first-ever solid descant. Instead of simply improving traditional adsorption dryers, which use thousands of tiny, loose desiccant beads to dry compressed air, we devised a product, best explained through five key points:
- Lower energy costs. The compressed air flows straight through the structured Cerades, reducing the drop-in pressure of the dryer. In loose desiccant, the air must overcome more resistance as it travels through the beads.
- Desiccant beads get pushed around through the drying tower during the cycle. This friction causes the beads to decay over time, which can compromise dew point. Cerades lasts much longer to protect air quality and extends service intervals.
- As loose desiccant decays, it releases a fine dust into your air system—which creates a requirement for extra filtration and maintenance, adding to service costs. This dust is also a health and environmental issue, as it circulates in the ambient air during desiccant replacement. Cerades eliminates this problem, providing environmental and health protection, lower operational costs, and reduced downtime.
- Cerades is vibration-resistant and can be mounted horizontally.
- Dryers with ceramic desiccant can handle a higher airflow.
FE: How does Cerades work?
Norz: Simply put, as a structured desiccant—consisting of a solid, ceramic block—Cerades dries the compressed air as it flows through straight, structured tubes.
FE: What are the benefits in using Cerades over conventional desiccants? How does purging compare between the ceramic and conventional materials?
Norz: When it comes to purging, whether a solid or bead desiccant, you want your purge rate to be between 15-20%. Cerades hits this mark, achieving a rating as low as 16%. Dew point ratings impact the efficiency of the purge, and dew point controls affect the airflow and amount of air being dried. With Cerades, if the customer is not using a PDP (pressure dew point) sensor, it will continuously dry the air to the required PDP.
As standard desiccants decay over time, it influences the PDP levels and impacts efficiency. With Cerades, there is no desiccant decay. With no desiccant decay, Cerades is environmentally friendly, provides clean compressed air and eliminates hazardous fine dust.
An inherent disadvantage of a standard desiccant is that it will lose its drying capacity when water enters the dryer. This causes problems for the drying process and negatively affects air quality. Cerades overcomes this issue and will retain its drying capacity even when wet, providing an additional benefit that nobody else is offering.
FE: How can a Cerades-based dryer especially benefit the food and beverage industry?
Norz: Cerades offers the food and beverage industry benefits in the areas of cost savings, performance and sanitation. Through the security of a reliable dew point, Cerades provides customers constant performance, resulting in energy savings and cost savings. Additionally, contamination from dust particles often seen with a conventional desiccant is eliminated with Cerades. As such, customers’ products remain clean and safe, and the threat of contamination is removed.
FE: Can this desiccant be used with existing dryers, or does new equipment need to be purchased?
Norz: To ensure the customer receives the full benefits of Cerades, we are only offering this technology in new equipment. Currently, our engineers are developing a plan to create a rebuild kit for bead dryers. When Atlas Copco launched its CD+ dryer range series in 2017, Cerades was already in the works, and we were prepared for the units to be replaced. The CD 20⁺-335⁺ is the first dryer to use Cerades.
FE: What is the expected lifetime of the Cerades material? How does the cost to replace it compare with conventional desiccants?
Norz: The dryers using Cerades in our lab has been running for multiple years, and we have not seen any performance reduction. We anticipate a life span of seven years, compared to approximately four to five with a conventional desiccant. Considering the replacement cost of a conventional desiccant, paired with the added 2-3 years of Cerades life expectancy, the replacement cost for Cerades is relatively the same.
FE: Is the technology available now in the U.S.?
Norz: Cerades is available in the U.S. exclusively through the new Atlas Copco CD 20⁺-335⁺ adsorption dryer series.
FE: Is the system operating anywhere in food and beverage now?
Norz: Cerades was launched in July 2020, and we have seen high interest from the industry, as well as in the direct and indirect air use for the process.
For more information, visit atlascopco.com.
Looking for a reprint of this article?
From high-res PDFs to custom plaques, order your copy today!