Partner with utilities to cut costs, improve your corporate sustainability image
Learn about resources to save money on power and be a good steward of natural resources

Cargill recently completed the installation of an on-site solar project at its facility in Velddriel, Netherlands. The solar panels spell out “Cargill” on the roof.
Photo courtesy of Cargill

The move away from coal at a New Zealand site is part of Fonterra’s plans to have net zero emissions at its manufacturing sites by 2050. Once completed, the transition at the site will reduce the cooperative’s national coal consumption by almost 10%, saving more than 84,000 tonnes of carbon emissions per year—the same as taking 32,000 cars off the road.
Photo courtesy of Fonterrra

Hormel Foods partnered with IGS Solar to build a 1.2 million kWh solar facility at its pepperoni/salami plant in Lathrop, Calif.
Source: Hormel Foods

Frito-Lay announced its zero- and near-zero emission freight facility project in Modesto, Calif. Part of California Climate Investments, it will transform one of Frito-Lay’s largest sites in the U.S. into an industry-leading showcase for environmentally sustainable manufacturing, warehousing and distribution. From left to right: Matt Fenton, senior site director, Frito-Lay Modesto; Mike O’Connell, vice president, supply chain, PepsiCo; Dr. Alexander Sherriffs, board member, California Air Resources Board and San Joaquin Valley Air Pollution Control District; and Samir Sheikh, executive director, SJVAPCD.
Photo courtesy of Frito-Lay




Electricity is relatively inexpensive in the U.S. today, thanks to the low market price of natural gas, which is the biggest source of power for electrical generation. However, unless you also have plants in the rest of the world, the cost of electrical energy may not be top of mind to you, but you can be sure that in the eyes of your end customers (we consumers), your commitment to sustainability may be the one factor that gains or loses a sale for your business.
Natural gas generated 38.4% of the nation’s electricity in 2019, as reported by the U.S. Energy Information Administration in February. Electrical energy generated by coal accounted for 23.5% of U.S. power generation, while nuclear energy produced 19.7%, and renewables created 17.5% of our electricity.
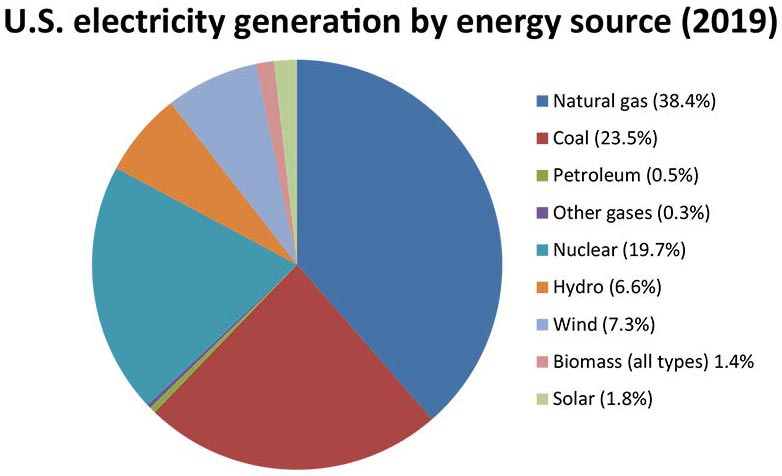
Source: U.S. Energy Information Administration
The battle for saving energy and improving your public sustainability image can be fought on many fronts. Today, resources are available that not only can help you save energy—and money—but also to help you be a good steward of our resources. While large food companies have their own sustainability departments, small and medium processors often don’t, but would still like to do their part. For them, the path to take is not always so clear. While a small processor may not think of it, a local utility might actually be a good place to get started on the path to improving energy savings and corporate image. Certainly, if a local utility doesn’t have the resources on staff, it will have the right connections to a knowledgeable energy management firm. Even smaller processors, however, can learn from watching what the large manufacturers do because every sustainability improvement happens on a plant-by-plant, project-by-project basis.
What Cargill is doing
Cargill is one worldwide food company that has the wherewithal to get sustainability done on a large scale, and has a department that sees to it. I spoke with Peter Dahm, sustainability director, operations and natural resources at Cargill’s Business Operations and Supply Chain, to get a big picture of what is doable when a large food company has the resources to create sustainable operations corporatewide.
FE: Please describe sustainability programs in development or in place to decrease the use of electricity or natural gas.
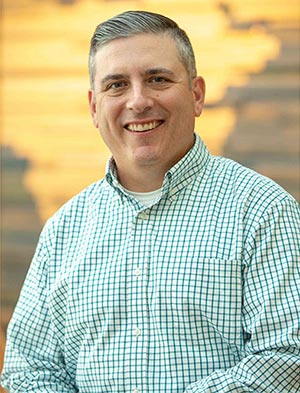
Peter Dahm: At Cargill, we are working to reduce CO2 emissions by 10% by 2025, measured against a 2017 baseline. To deliver on this goal, we’re focused on operating more efficiently, advancing on-site renewables and investing in off-site renewables.
We recently announced a handful of global renewable energy projects that will help us reduce approximately 350,000 metric tons of CO2 emissions a year, which is comparable to providing electricity for more than 40,000 homes per year. We are working toward this goal by developing and executing projects around the globe.
Earlier this year, in partnership with Geronimo Energy we announced a virtual power purchase agreement (VPPA) for the Prairie Wolf Solar Project in Coles County, Illinois. This is the second VPPA between Cargill and Geronimo Energy. The project is estimated to offset CO2 emissions by approximately 285,000 metrics tons annually, the equivalent of 32,887 homes’ energy for one year. This project builds on our existing work with Geronimo Energy through the Crocker Wind Farm.
In 2018, Cargill initiated a VPPA with Geronimo to buy 50 megawatts of wind power from Geronimo Energy’s 200MW Crocker Wind Farm project.
In addition to VPPAs, we are also pursuing energy savings within our plants through both management systems as well as improving the efficiency of our operations. In order to reduce GHG emissions, we are also pursuing the use of cleaner fuels where they are available.
Cargill recently completed the installation of an on-site solar project at its facility in Velddriel, Netherlands. The total installation size is around 100 kWp, which will save 50 metric tons of CO2. This means that during the day, the facility will be 100% powered by energy from the solar panels.
At Cargill’s plant in Villagorgona, Colombia, Cargill partnered with a local energy company to construct a solar farm near the plant. This solar farm will provide approximately 42% of the plant’s electricity needs, delivering clean solar power and reducing approximately 2,500 metric tons of CO2 annually.
FE: Are you partnering with electric or natural gas utilities to find ways to reduce utility usage? If so, how have the efforts helped?
Dahm: Cargill launched a joint venture with a local renewable energy provider, CleanMax, at Cargill’s facility in Davangere, India, to supply 70% to 80% of the facility’s electricity needs through a wind and solar hybrid power park in the state of Karnataka. The partnership will help eliminate 29,865 metric tons of CO2 emissions per year.
In Kansas, Cargill has partnered with Westar, our local electricity provider through its green tariff offering. Under this program Cargill is a subscriber to the Soldier Creek Wind Farm. Via Westar, we will be supplying 87% wind power to our plants in central Kansas.
In Texas, we recently announced a physical solar power purchase via our retail energy provider, MP2. This purchase will supply 90% solar power to our plants within the market.
As the world faces extraordinary challenges, like climate change, delivering on Cargill’s purpose to nourish the world in a safe, responsible and sustainable way is more critical than ever before. That is why we collaborate with strategic partners in our sustainability and renewable energy work to bring this purpose to life and to help meet our goals.
FE: Have the projects met your expectations?
Dahm: All of these renewable energy projects are helping drive progress toward our climate commitment to reduce our absolute operational emissions by 10% by 2025. In FY2020, Cargill cut emissions in our global operations by 2% from a 2017 baseline on an absolute basis.
FE: What are your future sustainability goals for the use of electricity and natural gas?
Dahm: Managing climate is a top priority at Cargill, and the company is making progress in its operations with new renewable energy projects. This year, Cargill announced 10 new renewable energy sources around the world, including wind and solar power.
These renewable energy projects represent Cargill’s expanding renewable energy portfolio and progress against its climate commitment to reduce 10% of its overall greenhouse gas emissions from its operations by 2025, against a 2017 baseline. This is in addition to its commitment to reduce greenhouse gas emissions in its global supply chains by 30% per ton of product by 2030.
We continue to participate and invest in renewable energy projects to change the way we power our operations, harnessing the innovative economic and environmental benefits of renewable power.
Help for smaller companies
In past articles, I’ve talked about leaks—“hidden” sources of electrical energy waste—for example, compressed air leaks throughout your facility or the underground water main break that causes a water pump to run 24 hours a day. Energy experts can help find these energy wasting leaks, and they can help in other ways as well. And like Cargill, you can partner with energy companies and utilities to help get you started and maintain programs.
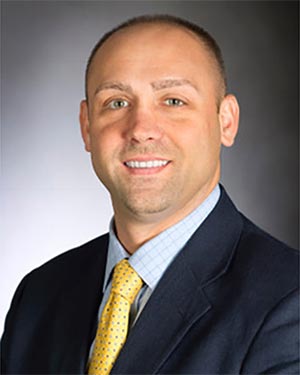
TJ Navarro, director, solutions at Constellation’s Efficiency Made Easy, tells a simple story of how replacing old inefficient lighting with low-energy LEDs produced an unexpected, happy result at a parts manufacturing plant. Constellation is an Exelon company, which is the parent company to many utilities throughout the nation, some with their own energy management programs.
“We worked with a plastic injection mold company, and we did a lighting upgrade for them,” says Navarro. Some weeks after the installation, Navarro got a call from the chief executive officer reporting that the employees were happy with the new lighting, and although the manufacturer’s internal rejection rates went up, their customers were extremely happy, saying their incoming rejection rates were lower than ever. What happened? While the manufacturer saved $400,000 over four years in electrical energy, something much bigger occurred.
When the executive asked what was going on in the production line, employees said that with the new lighting they could now better see the products they were making and were able to pick out defective parts easily—hence a higher internal rejection rate that kept bad parts from going out the door. With more light on the subject (excuse the pun), the manufacturer’s staff was also able to see better what was going on with the production equipment, make some engineering changes to the line, and retool the process. In the next six months, the company saved a half-million dollars by cleaning up the process and reducing rejects—thanks to the improved lighting.
Could a lighting improvement help your plant save energy and be more productive too?
While a big company like a Cargill or a General Mills has its own sustainability support staff, small and medium companies often don’t—or they give the duties over to the plant manager, as happened in a manufacturing facility where I once worked. Like the plant manager doesn’t have enough to worry about besides the shrubbery, blue herons and the wetlands on which the plant’s industrial park is situated.
This is where Navarro’s group can help. “One of our core competencies as a company is structuring commodities to help customers control costs and set budgets.” This means Constellation can help manufacturers with customized energy and pricing strategies whether solutions revolve around natural gas, electricity and/or renewable energy products.
Constellation will send in experts to understand how a manufacturer uses energy, recommend monitoring capabilities, install any necessary monitoring hardware and/or software, and work out a billing plan that fits the processor’s needs. In many cases, companies see an ROI in four to five years. Lighting is not the only consideration. Consultants will look at factory equipment, HVAC, air compressors, water pumps and manufacturing processes in general to discover and recommend energy-saving changes. Some clients have even considered CHP (combined heat and power) systems.
While electrical generation rates have come down due to decreased costs of fuels, demand costs, transmission fees and regulatory charges today can be equal to the electricity itself, says Navarro. In some communities where electrical generation rates are as low as 4 cents per kWh, the other charges can sometimes more than double that amount. That’s why it’s important to monitor and control demand. Some clients have installed large capacitor banks to store energy overnight when rates are low to be ready to take the demand load or surge when equipment is started in the morning, thus decreasing demand charges from the utility. Of course, sequentially starting large motors with VSDs can also lower demand charges. Energy management systems can be linked with control systems to minimize demand usage and its charges.
Consultants like Navarro can also help clients with energy credits and solar installations where, in states like New Jersey, solar can be a big deal. Warehouses that put 500-600 kWh arrays on their rooftops can see ROIs in four to five years.
Another energy consulting company, CLEAResult, works with manufacturers and often partners with energy companies to help reduce electrical usage. Founded in 2003, the independent company has offices in 60 cities in the U.S. and Canada. Like Constellation, it can provide a comprehensive set of energy programs and demand-side management strategies. One program it offers for commercial and industrial facilities is called Strategic Energy Management, which is explained in an online webinar.
A good bet: If you enlist an energy company to help you decrease costs, you may find that the savings you realize will outweigh the consulting and material costs in a relatively short period of time.
Looking for a reprint of this article?
From high-res PDFs to custom plaques, order your copy today!