Water filtration
Strainers with automatic scraping prevent clogging and fouling in water/liquid filtration
While these devices can filter out micron-sized particles, they also minimize downtime normally associated with manual cleaning and blowdowns
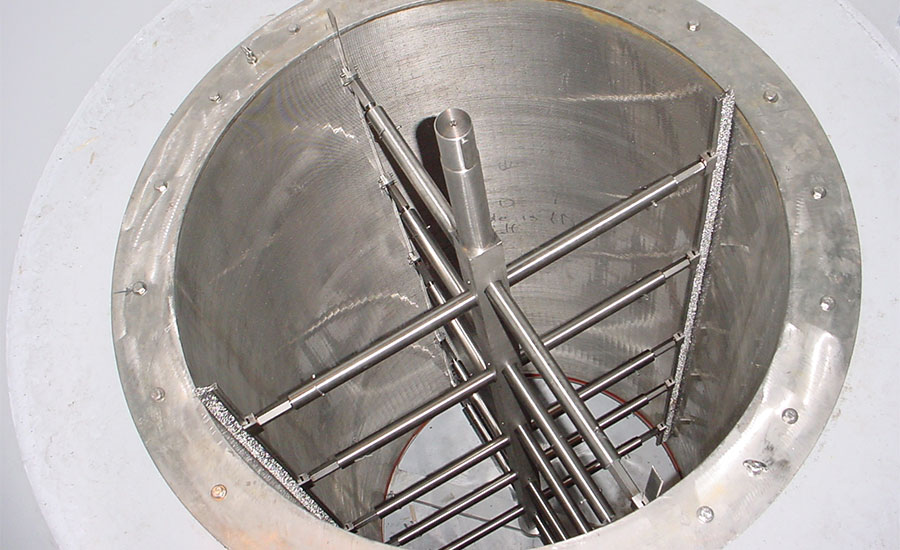
Plugging and fouling from large solids and small particulates can cause unscheduled downtime, excessive maintenance and costly premature replacement, but automatic scraper strainers can remove waste from raw water before the debris enters heat exchangers and cooling systems. Source: Acme Engineering Products Inc.
Automatic strainers have many uses, for example, providing necessary filtration for process cooling water, liquid product, and wastewater treatment. Each application requires the removal of suspended solids of various sizes to attain certain characteristics or qualities.
Traditionally, filters have been limited to a rather narrow range of particle sizes, so plants may require multi-stage filtration if straining to a wide array of sizes is required. Moreover, conventional filters typically must be manually cleaned. This necessitates taking them out of service, resulting in downtime during each manual cleaning. In addition, if clogging or fouling occurs, then compliance issues can cause additional delays in operation.
In response, filter suppliers have developed automatic, self-cleaning scraper-strainers that filter out both tiny particles and large debris. Since one unit can handle a wide range of sizes, it can eliminate the need for larger, multi-stage filtration equipment in downstream wastewater filtration and other processes.
Process cooling operations
According to Robert Presser, vice president of Acme Engineering, a North American manufacturer of industrial self-cleaning strainers, the most common automated scraper strainer application is to clean and filter plant cooling water so it can be reused.
With these cooling systems, recycled water typically circulates through pipes, absorbing system heat from production machinery, and then is returned to be filtered and reused. Usually, a chiller unit is utilized in process water cooling to remove the accumulated heat.
When outdoor cooling towers are used in conjunction with process cooling, debris such as dust, dirt, leaves, and even windblown trash may need to be removed before the re-circulated water can be reused.
“Strainers are commonly utilized to remove suspended solids from the cooling water,” says Presser. “Failing to do so sufficiently can risk fouled processes and production downtime.”
The benefit of an automated scraper strainer that removes both small particles and larger debris for re-circulated process cooling water is improved system performance, uptime, and product quality with minimal operator oversight.
It’s not necessary for an operator to open and clean an automated scraper strainer (as is needed with a manual strainer), says Presser. No manual blow-down of strained solids is needed. Since the scraper strainer operation is automatic, it is essentially “set-and-forget,” which allows operators to walk away and focus on other aspects of the facility.
For example, with the automatic scraper strainer from Acme, the motorized unit is designed to continually remove both very large and very small, suspended solids down to sub-100-micron particles from process cooling water, liquid product, and wastewater. Cleaning is accomplished by a spring-loaded blade and brush system, managed by a fully automatic control system.
Four scraper brushes rotate at 8 rpm, resulting in a cleaning rate of 32 strokes per minute. The scraper brushes get into wedge-wire slots and dislodge resistant particulates and solids. This approach enables the scraper strainers to resist clogging and fouling when faced with large solids and high solids concentration. It ensures a complete cleaning and is very effective against organic matter “biofouling.”
Blowdown occurs only at the end of the intermittent scraping cycle when a valve is opened for a few seconds to remove solids from the collector area, so manual cleaning is not necessary. Liquid loss is well below 1% of total flow.
Liquid product
Automatic scraper strainers are also applied in the food processing industry to filter liquid products to certain specifications or quality standards, says Presser.
For example, the automatic scraper strainer has been used to filter out excessive amounts of orange juice pulp by a company in South America. This application did not use a scraper brush to avoid bristle contact with the product. Instead, fiberglass blades were used, and the rest of the equipment was constructed of food grade SS316L (stainless steel).
A similar method could also apply to straining applications of various food products that have some liquid or semi-liquid component.
![]() |
Getting a sense of scale…For a really large water treatment center operation, self-cleaning scraper strainers can filter small particles and large debris. Note the automobiles in the lower-right corner. Source: Acme Engineering Products Inc. |
Wastewater treatment
As food processing plants seek to reuse as much water as possible for internal use, applications that were previously supplied by potable water are being converted to grey water sources to aid conservation. The ideal would be to achieve a closed loop system that continually filters, treats, and reuses much of the plant’s wastewater stream. However, this requires sufficient straining.
“Properly filtering grey water can involve settling tanks and downstream treatment through a membrane,” says Presser. “However, automatic scraper strainers that filter down to 100-200 micron-sized particles can simplify the process in a single step and handle volumes up to 20,000 GPM as needed. This simplifies wastewater treatment and can eliminate multi-stage filtration system cost and complexity.”
Presser adds that the strainers are also used to remove certain solids from the waste stream so the water can be discharged or sent for further downstream treatment depending on local environmental regulations.
When a facility has both small particles and large debris in its process cooling water, liquid product, or wastewater, using an automatic strainer minimizes the required maintenance to keep it operational and helps to maximize production uptime.
For more information:
For more info, visit Acme Engineering Prod. Inc. at acmeprod.com or call Robert Presser at 518-236-5659. In Canada, call 514-342-5656.
Looking for a reprint of this article?
From high-res PDFs to custom plaques, order your copy today!