Legacy software
Five signs it’s time to upgrade your legacy SPC system
Not only can a new system provide you with more actionable data, it'll be more secure
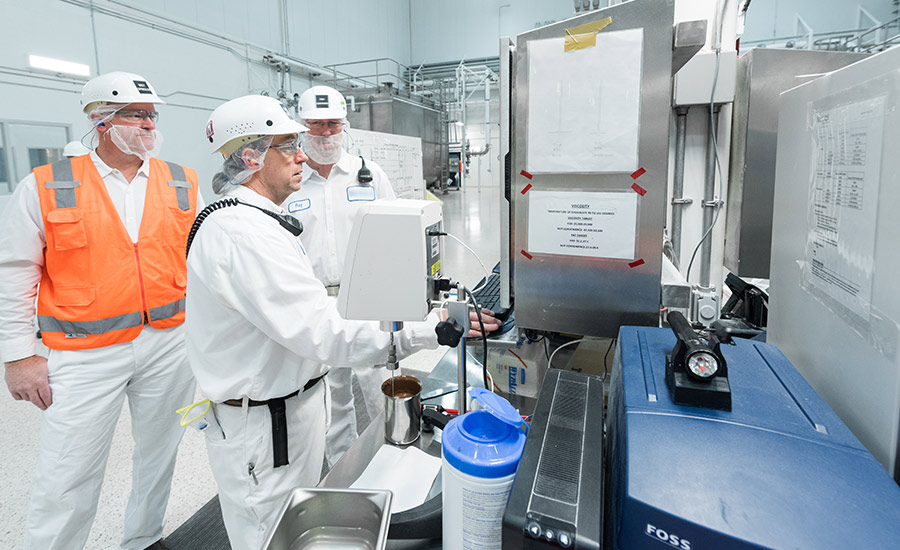
Team members check viscosity of a chocolate sample and enter it into the quality control system. Statistical process control software can keep a running tab on product quality and let operators know what process variables could put the resulting product out of tolerance. Photo by Imagemakers Inc. for Food Engineering
Statistical process control (SPC), as you probably know, is an industry-standard methodology for measuring and controlling quality during the manufacturing process. The concept was developed at Bell Laboratories in the 1920s by physicist and statistician Walter A. Shewhart, who came to be known as the father of statistical quality control.
Shewhart realized that he could detect differences in the sources of variation of a manufacturing process—whether sources were “common” (natural/predictable) or “special” (unusual/unexpected). He described common variations as “in control” and special variations as “not in control.” And thus, the control chart and SPC were born.
At the time, SPC was performed manually with a pencil and paper. Fast forward to the end of the 20th century, and advancements in computing brought myriad SPC software systems to the marketplace, followed by a wave of upgrades and improvements.
Initially, these systems made SPC easier, faster, and more efficient. But that period of innovation slowly dried up. The overall design and architecture of the software has since remained largely unchanged, and many legacy systems are still in use today.
If it ain’t broke…
Manufacturers often have an “If it ain’t broke, don’t fix it” mindset when it comes to their SPC systems. If the old system still performs the basics, why spend the money to change it?
While it may not be broken in a literal sense, an outdated SPC system limits a manufacturer’s ability to achieve the efficiency, productivity, flexibility, and level of quality needed for success in modern manufacturing. Next-generation SPC solutions are available today that mark a radical shift away from the design of their predecessors. They’ve been architected from the ground up to better support manufacturers’ needs, today and well into the future.
If your manufacturing organization is still maintaining a legacy SPC system, the following five signs indicate it may be time to embrace a next-gen solution:
1. Your data is siloed
Legacy SPC systems usually store data locally, meaning the files are only accessible on the workstation or device on which that system is installed. This creates “islands” of data that are isolated, incomplete, and inconsistent across manufacturing operations.
These islands can’t talk to or integrate with one another, making it nearly impossible for organizations to manage consistency, standardization, and governance of the data. Any meaningful comparisons or analyses are limited, keeping an organization from seeing the “big picture” of quality across their operations. Valuable insights are left untapped and opportunities for quality improvement are missed.
Moreover, on-premises legacy SPC systems also keep data siloed inside the plant—a limitation that caused issues during the COVID-19 pandemic. As many quality personnel and plant managers shifted to remote work for the first time, they found they couldn’t access critical information or stay connected to the plant floor.
The next-gen difference: Thanks to the power of the cloud, modern SPC solutions offer a better approach. Cloud-based systems can integrate with a multitude of sources to collect, streamline, standardize, and store data—from all processes, lines, and plants—in a secure, centralized repository. The data and resulting analyses are accessible in real time, from any device with a web browser.
Plant managers and quality pros can access the “big picture” of processes and product quality, whether they’re at a shop floor workstation or using a smartphone on the go. Managing and maintaining processes and data becomes much more efficient. And when everything is centralized and standardized, it is also much easier to uncover actionable insights for quality improvement across entire manufacturing operations.
2. You’re bogged down by inefficiency
Manufacturers constantly strive to improve efficiency and productivity. That’s why we see so many organizations implementing Lean Six-Sigma, Good Manufacturing Practice (GMP), and other methodologies to achieve more efficient operations, while delivering better, faster, cheaper products for consumers.
Unfortunately, legacy SPC systems have exactly the opposite effect. First, quality data needs to be recorded by operators, who spend a large chunk of their time watching control charts and monitoring process parameters waiting for a violation that may or may not occur. Then there is the tedious process of preparing data for further analysis. This might involve transcribing paper forms into a digital format, merging multiple Excel spreadsheets, or manually importing and reformatting data from multiple other systems. When analysis is complete, quality professionals interpret, export, and then distribute the results (usually on paper forms or via email).
All this takes considerable time, so these processes are usually performed in a “batch” after the end of a run, shift, day, week, or sometimes even month. All the while, hidden issues are dragging down efficiency and productivity. And by the time they are found, its often too late to take remedial action. The result is a significant amount of scrap, waste, rework, and downtime.
The next-gen difference: Manufacturing happens in real time, and so should SPC. Next-gen solutions can automate data collection and analysis to stop problems in real time, as well as utilize exception-based reporting to free up operators’ time and focus. Essentially, the software continuously monitors data streams to detect specification or statistical violations as they happen.
Data is entered directly into the SPC system, so there is immediate feedback (i.e., is any action required or not?). When the software detects a problem or concerning trend, operators, quality teams, and other relevant personnel are immediately alerted. No poring over control charts or sifting through extraneous data—the information needed to act fast, maintain quality, and keep operations running smoothly is presented directly to the right people in real time.
3. You’re suffering from data overload
Legacy software provides the basics of SPC. But to keep up with the demands of modern manufacturing, organizations need greater insight into trends that impact performance. Armed with just legacy software, manufacturers have no way to extract anything meaningful from the massive amounts of data generated on the plant floor—data that holds untapped insights into questions like:
- How is a particular feature or product performing across different production lines or shifts?
- Are quality checks being performed on time?
- How is yield performing across multiple plants?
- Where do the greatest opportunities for quality improvement lie?
- What best practices can be applied organization-wide?
The next-gen difference: Today’s SPC software not only offers a greater wealth of statistical calculations and KPIs than traditional systems; they also provide advanced analysis and visualization tools that can help manufacturers cut through the deluge of data and quickly find those “golden nuggets” of valuable information.
A great example is stream grading. This quality tool automatically analyzes data streams coming from various products, lines, and sites, and then summarizes performance with a simple letter-number combination representing potential and yield. Supervisors, plant managers, or executives can jump right into the grading dashboard to easily compare performance—region by region, plant by plant, or product by product—and then prioritize resources and plan improvement efforts accordingly. This level of speed and clarity simply wouldn’t be possible using a legacy system.
4. Your system is overly complex
Modern manufacturing environments have become increasingly complex, with advanced technologies like automation, intelligent sensors and controllers, and robotics now common on production lines. Unfortunately, legacy SPC systems have not seen that same level of innovation and are now more of an obstacle than a solution.
Legacy systems have become difficult to use, understand, and manage, thanks to layers upon layers of features, functionality, and bug fixes tacked on over the years. As a result, they often require a high level of knowledge and training to use effectively.
The next-gen difference: Modern SPC software is designed with simple, highly intuitive, web-based user interfaces that make it easier than ever to learn and navigate the system. Some solutions offer configurable, role-based dashboards. Users can rapidly access only the information that is relevant to their work responsibilities, reducing information overload and keeping everyone on top of their tasks.
5. You’re spending all your resources
Legacy SPC software has a high cost of ownership, when you consider the resources required to procure, implement, deploy, and manage it. Software licenses must be purchased up front, as well as all the associated infrastructure. Moving forward, the software vendor may or may not provide any further innovative upgrades, and internal IT teams will be on the hook to handle any maintenance issues or support.
What happens when that system does not meet an organization’s evolving needs? The choice is either to use the system—drawbacks and all—or write off what was likely a significant investment. And if a manufacturer focused on expansion wants to scale their system, they will be investing in additional software licenses and new infrastructure. All those costs add up significantly.
The next-gen difference: Software-as-a-Service (SaaS) solutions are transforming the way manufacturers “own” SPC systems. Their cloud-based infrastructure and subscription-based models make deploying—as well as scaling—a new system quick and easy. There is no need for special hardware, new servers, or fixed workstations; all that’s needed is a subscription and a device that can connect to the internet.
SaaS vendors also must deliver continuous improvements through innovative updates to ensure the continued use and expansion of their solutions. Automated updates reduce the costs of maintenance, as well as the burden on IT teams. In short, almost everything is taken care of by the vendor.
Changing the game
The manufacturing world has evolved significantly since legacy SPC systems were originally designed, purchased, and implemented. We’re seeing impressive levels of digital innovation across every sector, and it’s time for SPC software to keep pace. It’s here that modern cloud-based solutions are a game changer, making it easier than ever for manufacturing organizations like yours to leverage the full power of SPC.
Looking for a reprint of this article?
From high-res PDFs to custom plaques, order your copy today!