Spotlight on: Robotics
New Plant Products | August 2022
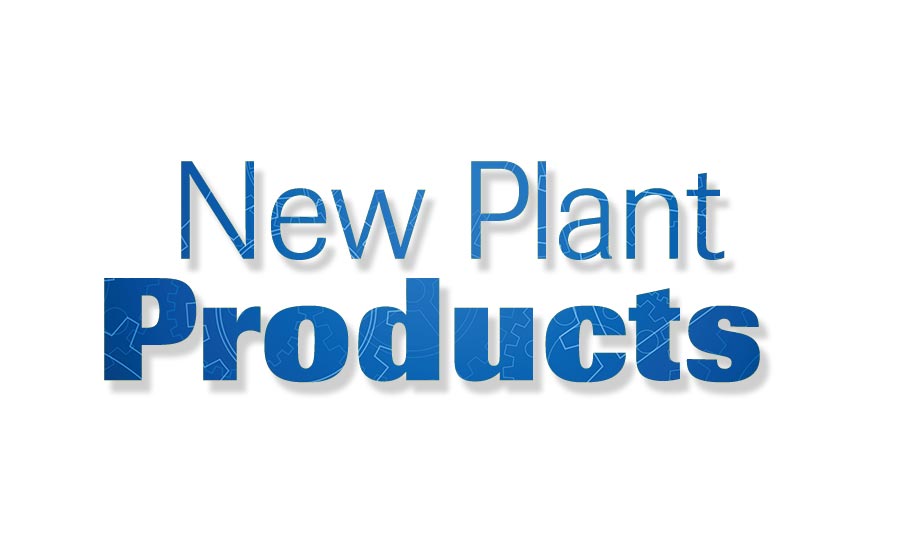
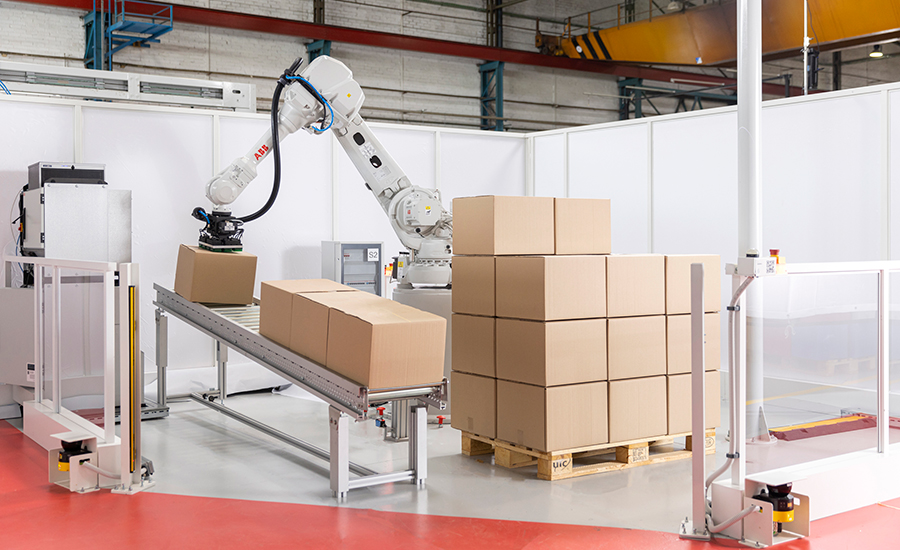
Robotic Depalletizer
Using machine vision software, this robotic depalletizer can quickly assess a range of box types, allowing customers to efficiently process assorted loads with very little engineering effort and short setup time. The unit’s software uses the information gathered by the vision sensor to provide the robot with a suitable grasping point for each box. The robot then picks up the box—weighing up to 30 kg—and places it on either another pallet or an outfeed conveyor. The speed and accuracy of the system enables it to work at a peak rate of up to 650 cycles per hour, 24 hours a day. The vision sensor enables the robot to detect specific carton boxes on pallets, allowing reliable depalletizing of several different load types. These include pallets comprised of a single type of box in defined layers; ‘rainbow’ pallets containing a number of different box types; and mixed pallets with a wide range of boxes with varying weights, shapes and materials.
https://foodmaster.com/directories/68-food-processing-equipment/listing/11873-abb-inc-robotics
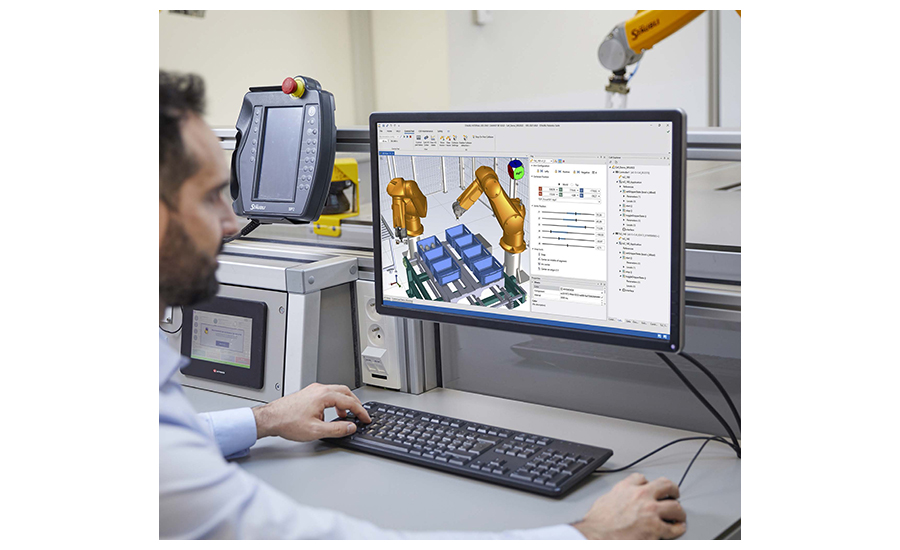
Robotics Suite
The company’s new Robotics Suite 2022 allows both standard and special solutions for complex automation scenarios to be readily visualized, simulated, validated and realized. New functions extend across all scopes of usage, from design, simulation and setup debugging to production and optimization.
A new feature is that parts can be selected from an integrated component catalogue. If individual parts or assemblies are used frequently, users can store them in such a collection. The snap function is used to position objects/components or to simply move the robot to a desired position without having to create position variables in advance. The position optimizer is designed to guarantee the automatic identification of the ideal position for the robot to reach every point desired within its available defined working area. The suite is enhanced by screen capturing, now an integrated feature. The control panel, also now integrated, supports the user in optimizing processes and movements during the simulation.
https://www.foodmaster.com/directories/68-food-processing-equipment/listing/12820-staubli-robotics
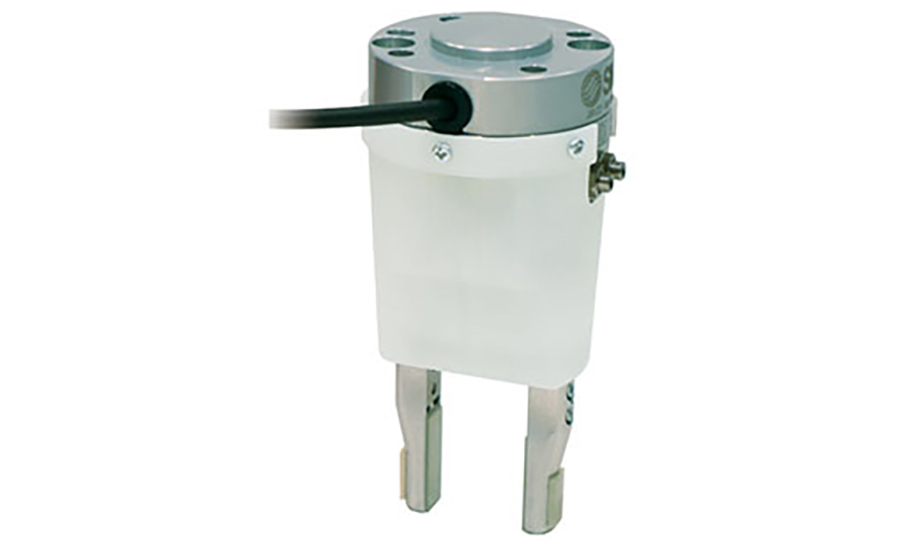
Air Gripper Unit For Collaborative Robots
JMHZ-X7400B is a pneumatic two-finger gripper designed for collaborative applications (cobot). It provides plug-and-play configuration for immediate use with URCap programming. Integrated solenoid valve and speed adjustment provides simple installation and setup, requiring only one air supply tube and M8 connections. Features include:
- Bore size: 16mm
- Compatible with UR3(e), UR5(e), UR10(e) and UR16(e)
- Weight: 430g (15.2oz)
- Gripping force: External: 32.7 N, Internal: 43.5 N
- Action: Double Acting
- Opening/Closing Stroke: 10mm
- Standards: ISO9409-1-50-4-M6
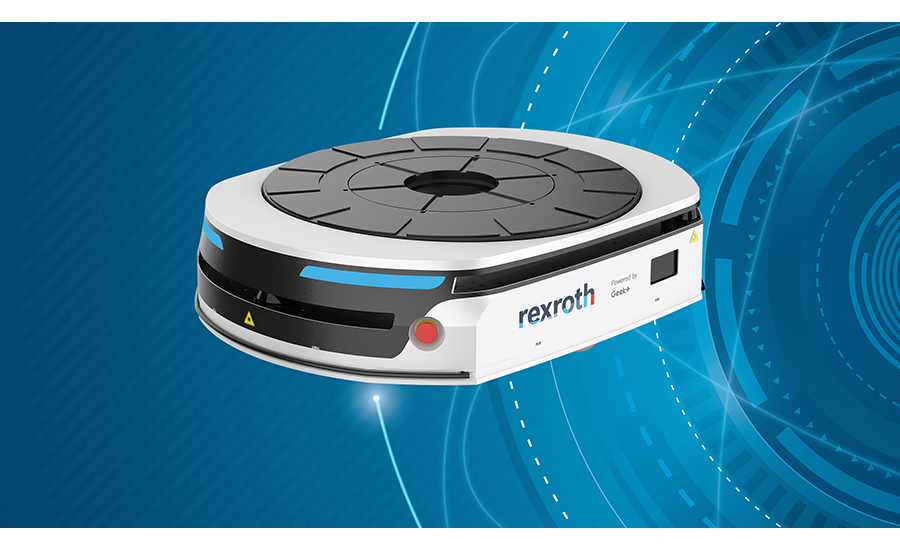
Autonomous Mobile Robot
The MP1000R is a new 1000 kg payload capacity autonomous mobile robot (AMR) that can automate material handling applications without additional external infrastructure. Using the company’s ROKIT Locator Software, the AMR is able to navigate autonomously in highly dynamic environments without additional infrastructure. This flexible and scalable solution can replace manual forklifts and tuggers in manufacturing spaces, leading to improved efficiency and help protect workers from potential injury. In addition to reducing safety risks, the robot can lift a max payload of 1000 kg on a standard rack or shelf base. It can also interface with customer-specific equipment using a square- or roller-top conveyor at customized heights. Its compact size and zero turning radius make it ideal for operating in tight spaces or down to aisle widths of 1400 mm (55 in). The fully loaded moving speed of 1.5 meters per second makes it suitable for moving pallets and shelves between warehouses or automatic storage and retrieval systems (AS/RS) to production areas or shipping docks.
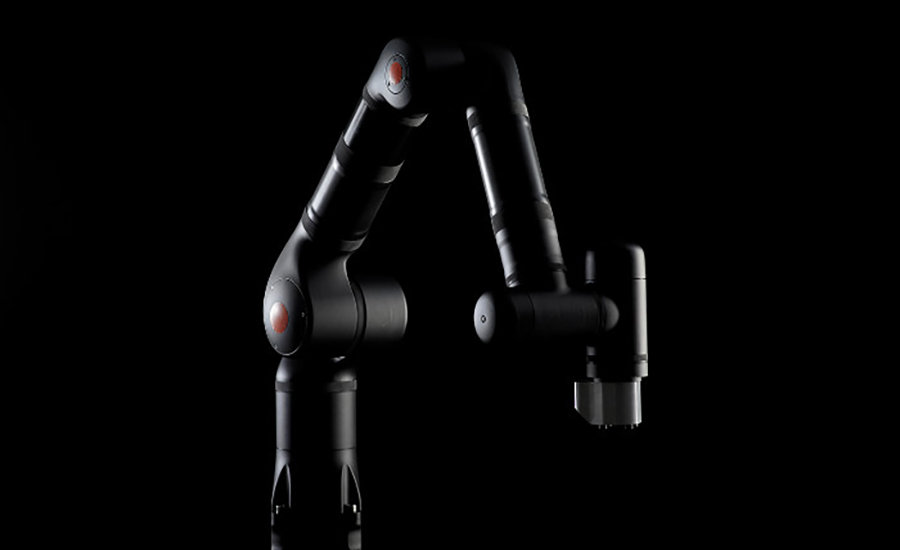
Lightweight Cobot
The KR810 has a payload of up to 10 kg, a reach of 850 mm, speed of 225 degree/second and 7 degrees of freedom. It requires fewer safety restrictions while offering increased maneuverability, making it suitable for working alongside humans in an industrial environment in machine tending, assembly, limited-space retrofits and related applications. The unit is suitable for industrial applications involving human-robot collaboration due to the unique seventh axis or “wrist” joint and safety-compliant designs inherent to the cobot class of automated material handling solutions. The KR810 is easily programmed by any technical expertise level, from engineer to machine operator. Programming the robot is a simple task of moving it into position and recording the key points. The company’s software does the rest.
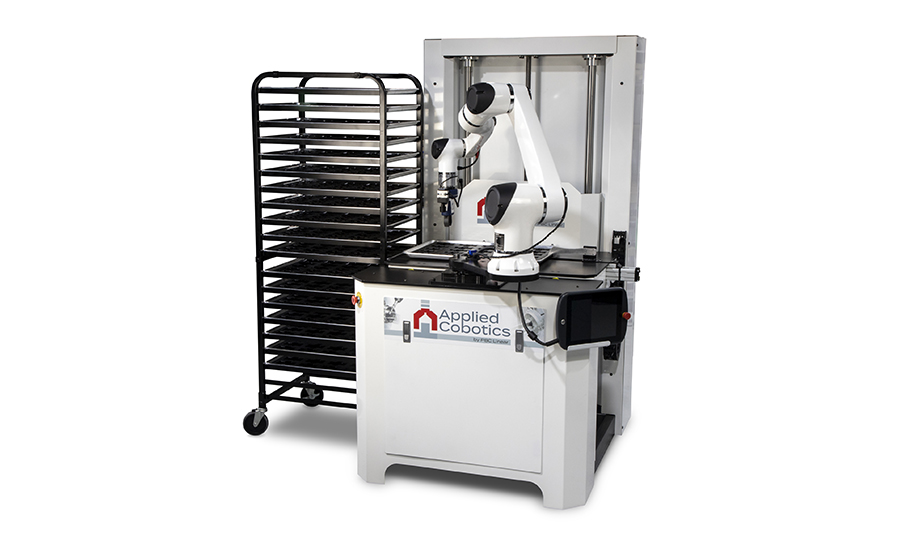
Applied Cobotics ASRS
This automated storage and retrieval system (ASRS) is de¬signed to assist collaborative robots and other types of automation robots by consis¬tently loading and unloading material dunnage trays within the cobot/robot-accessible work area. The machine features a vertical lead screw-driven shelf, and a horizontal tray loader/unloader that provides accurate and repeatable motion. Each ASRS base package comes with a dunnage tray/rack tower that is engineered to lock securely in place with the ASRS. It is capable of holding up to 17 trays, eliminating the need for a worker to period¬ically remove and reload material from the cobot work zone. It also offers open-spaced shelving that accommodates various part sizes up to 18 in. in height, and offers station-to-station mobility. The result is a significant boost in robot productivity from 10x to 20x that of standard means. A standard fixed robot mount offers 45° of adjustability and a custom bolt pattern that is compatible with any cobot/robot. The robot mount can be upgraded to a more flexible swivel stand and moved to different angles quickly and accurately.
Looking for a reprint of this article?
From high-res PDFs to custom plaques, order your copy today!