A Practical, No-Regret First Step to Complete Decarbonization
Setting an achievable ‘net-zero’ emissions goal is possible, however, it may require companies to lean less on renewables and more on a facility’s waste heat to make up the difference.

By now it’s clear that the major industries of the world must make radical changes to minimize the effects of climate change, and that includes revamping the thermal utilities that power our global food systems, which account for more than 34% of global greenhouse gas (GHG) emissions.
The good news is many of the world’s top food brands have already drawn lines in the sand, declaring “net zero CO2 emissions by 2050.” In the past year, dozens of other industry leaders and government entities have boldly announced their support of net-zero goals with plans to make and meet their own. The bad news is that few of those businesses and institutions have achievable and sustainable paths to meet the 2050 deadline. But that’s not to say paths don’t exist.
The U.S. Department of Energy just released its “Industrial Decarbonization Roadmap.” The report identifies four key pathways to reduce industrial emissions in American manufacturing, singling out energy efficiency as “the most cost-effective option for near-term reductions of greenhouse gas emission.” The report also said that this energy efficiency could be achieved through the implementation of software-driven, “smart” manufacturing systems and advanced data analytics that improve productivity related to energy use.
And, according to decades of research conducted by Armstrong International, a leading global thermal utility system solutions provider where I serve as CEO, food and beverage companies are uniquely positioned to achieve some of the greatest reductions in CO2 emissions without impacting their long-term output or bottom line. Unfortunately, the solution is not as simple as switching to renewable energy. We’re not yet at a place where renewables are viable, both from a cost perspective and availability. Not only is there not enough to go around, but industry-wide switches to renewables would overburden the current grid infrastructure and drive costs even higher.
The Solution Comes Down to Waste Heat
Within nearly all light industry manufacturing plants, especially food and beverage facilities, most of the energy consumed is not going into the product.
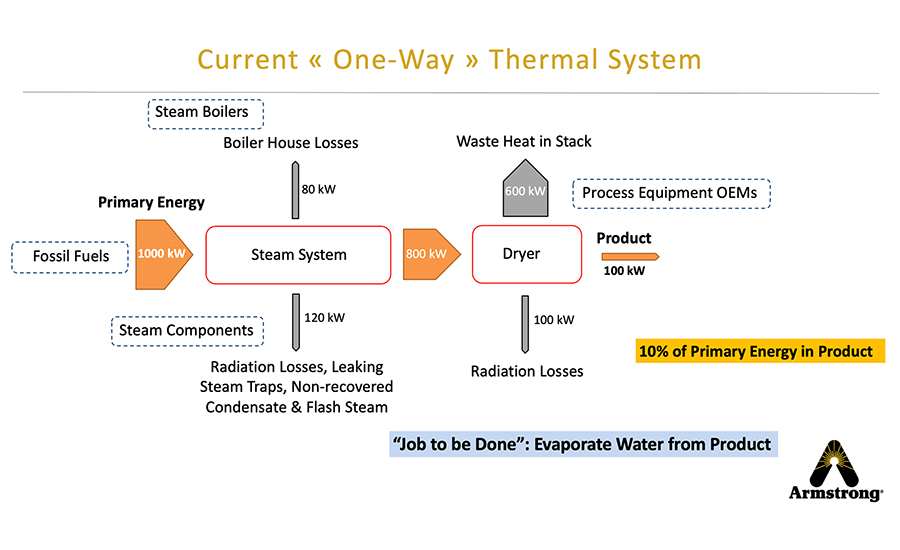
Armstrong's Circular Thermal approach aims to minimize the plant’s energy waste while optimizing its thermal energy efficiency and allowing plant managers to build a strategy for complete decarbonization. Credit: Armstrong International
Rather, it is released in the form of hot exhaust gases and radiating heat from hot equipment surfaces and heated products. For example, many of today’s food products require a lot of energy for cold storage and sterilization, which in turn produces waste heat that’s lost into the atmosphere. Meanwhile, the factory simultaneously needs heat at relatively low temperatures (below 250°F) to operate effectively—heat that could be pulled from the waste heat emitted during the cooling process.
However, most light industry facilities operating today were built more than 50 years ago, during a time when energy efficiency was not as top of mind as it is today. As a result, most plants are not equipped to capture and utilize the waste heat that otherwise escapes. If that waste heat could be captured as usable energy, however, it could reduce as much as 80% of a plant’s CO2 emissions, leaving the final 20% of emissions to be removed with renewables like solar, wind, geothermal or another source—improving an organization’s bottom line and ensuring a clear and sustainable path to net-zero emissions.
So, the questions remain: How do we capture that heat as usable energy? How do we channel that energy to where it is needed? Fortunately, this can be accomplished with a few additions to the infrastructure. After implementing an internal process heat exchanger network coupled with industrial high-temperature heat pumps, a thermal utility expert can then conduct a process that Armstrong has coined “Circular Thermal.” The process includes de-steaming (conversion to pressurized hot water) all applications below 250°F, recovering direct heat when a positive differential temperature is available, and using the industrial heat pumps for raising the temperature of low-grade heat to the appropriate temperature needed. This Circular Thermal approach minimizes the plant’s energy waste while optimizing its thermal energy efficiency and allowing plant managers to build a strategy for complete decarbonization.
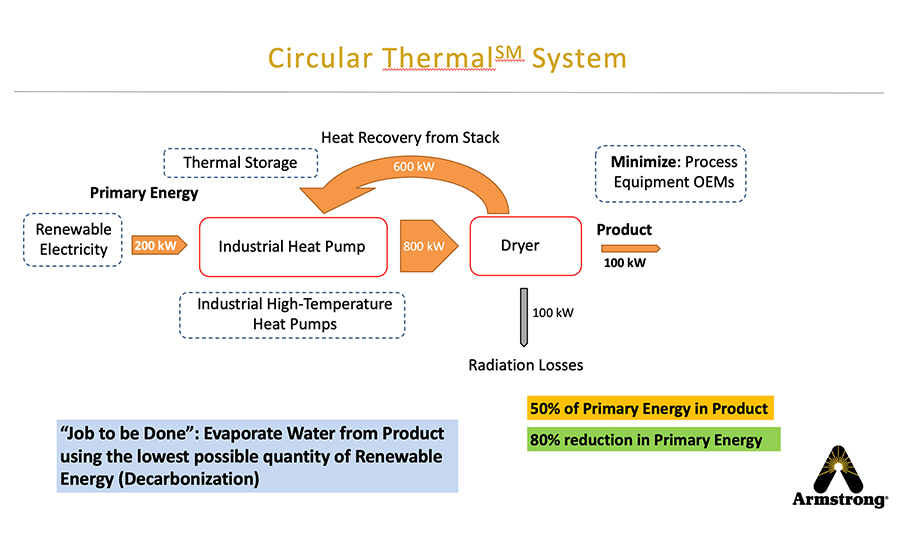
Armstrong's Circular Thermal approach aims to minimize the plant’s energy waste while optimizing its thermal energy efficiency and allowing plant managers to build a strategy for complete decarbonization. Credit: Armstrong International
Pinch begins first by performing a walkthrough of the facility to evaluate the performance of the thermal utility system, upon which a thermal utility expert establishes an initial baseline of the thermal utilities and identifies pain points within the utility infrastructure. Finally, the trained expert analyzes the data, utilizing a specific set of digital tools and software to help frame the approach, before developing the optimum strategy for integrating all heat sources within the facility in the most efficient way possible.

Minimizing energy waste while optimizing aging facilities is proven and backed up by the U.S. Department of Energy as the most cost-effective way to decarbonize light industry manufacturing plants. This practical, no-regret, first step to complete decarbonization not only improves a company’s long-term bottom line, but also serves as a guiding light to the rest of the world’s industries on how innovation can get us to net zero.
As our world continues to fight climate change, food and beverage companies are well-positioned to make a significant difference. Someday we may very well discover a renewable silver bullet solution for our energy needs, but why wager our future generations waiting for a solution when the energy problems we are currently facing can be solved with technology that’s available today?
Looking for a reprint of this article?
From high-res PDFs to custom plaques, order your copy today!