State-Based Control Uncovers Automation Gains
For an edible oil processor, the best way to efficiently manage unique characteristics of different products was by adopting modern control loop performance monitoring software with the ability to recognize different operating states.

Photo courtesy of Getty Images / Mediaphotosl
Most manufacturing operations are constantly faced with change, and therefore they must be designed to adapt. Change routinely presents itself in the form of different production recipes, varying material properties, irregular equipment availability, weather extremes and many other factors. What’s more, change often includes several of these variables concurrently, and each may interact with others—adding still more complexity.
If so many processes experience these complications, how can manufacturers apply technology to address the issue? Good automation system designs detect these conditions, and then they react by taking control actions to maintain production throughput, quality and efficiency. Even better control designs recognize not only varying conditions, but also unique operating states so they can tailor their control action in ways that are optimized for each state. Production plant control functionality must address changing situations, and similarly it does not make sense for their analysis to be based on averages from many varying states. Simply put: If a control system can respond dynamically to changing production states, then the facility’s controller analytics engines should be able to adapt as well.
One food and beverage manufacturer producing edible oils was faced with several operational challenges based on exactly these situations. It needed to produce different types of oil, but each version required its own unique tuning configuration for optimal results. Operators did their best with manual setting adjustments, and engineers applied model predictive control (MPC) to optimize runs for a given product. Despite these efforts, the results still fell short with each product changeover. A better approach was needed.
Semi-Manual, Semi-Automatic
For this edible oil production company, the equipment was tasked with refining two different types of oil, each with its own characteristics. A key part of the process involved dosing the oil with clay to “bleach” it. This removes the color, chlorophyl and performs other conditioning. The clay must then be filtered out. Each type of oil requires a different clay dosing rate, and in turn the filters need to be cleaned at differing intervals for best overall performance.
Before implementing control loop performance monitoring (CLPM) technology, some aspects of the company’s operations were manual and others were automatic. For example, when production began after a product changeover, operators would manually manipulate the system to achieve a steady state, and then apply tuning settings and setpoints corresponding with the product type. While this would result in product that was well within specification, it used more clay than was necessary.
As time progressed, local resources at the site attempted to improve the process through system tuning and eventually by applying MPC to optimize clay usage. Unfortunately, the process still failed to meet the expected performance levels. Product “A” seemed to respond well using MPC, but due to some combination of characteristics, product “B” controlled worse under MPC. Therefore, monthly reports showed no improvement in overall performance, and did not even reflect the improvements that had been made while the facility ran product “A.”
Another complication encountered was that readings of key product characteristics and control adjustments were based on grab samples that were intermittently and manually obtained by plant staff. The delays involved were detrimental to the control system’s ability to respond effectively. What’s more, inconsistency in the lab measurements themselves presented still more challenges for production staff.
If a property can’t be measured it can’t be improved, and if it can’t be measured in a timely manner then the response will be impacted.
Moving to State-Based
A complete solution would require some improved field instrumentation, incorporating a CLPM software platform with the ability to recognize varying operating states, and controls programming to implement the tuning results.
The first step was installing an inline colorimeter capable of providing the control system with immediate feedback on the product’s color. This eliminated the need for operators to gather and analyze samples by hand. Ultimately, the inline measurements were more accurate than lab analysis of grab samples.
Yet even if the right data is available, the complexity associated with multiple operating states and an overload of information makes it hard for anyone to tease insight without help (Figure 1).
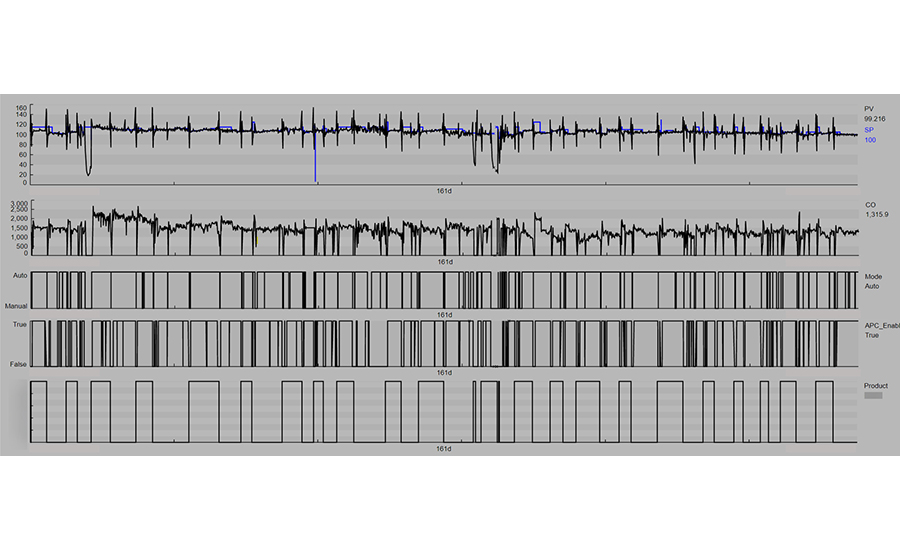
This manufacturing operation already used CLPM software to monitor and optimize individual PID control loops. However, when a process runs a given loop under varying states, standard CLPM software runs into trouble as unique details from each state are masked. The values of one state are averaged in with values from every other state. Standard CLPM fails to accurately distinguish and to characterize loop performance across a process’ different operating states.
Fortunately, the CLPM software selected by the manufacturer included state-based analytics, meaning it was capable of distinguishing many different operating states, and then dynamically analyzing loop performance within the context of the “active” state (Figure 2). States can be detected based on:
- Runtime conditions, such as flow rates or pressures;
- Operating phases, such as warmup, full production or cool down;
- Products: Often indicated by operators or following a recipe; or
- Any other detectable attributes, and any combination of the preceding conditions.
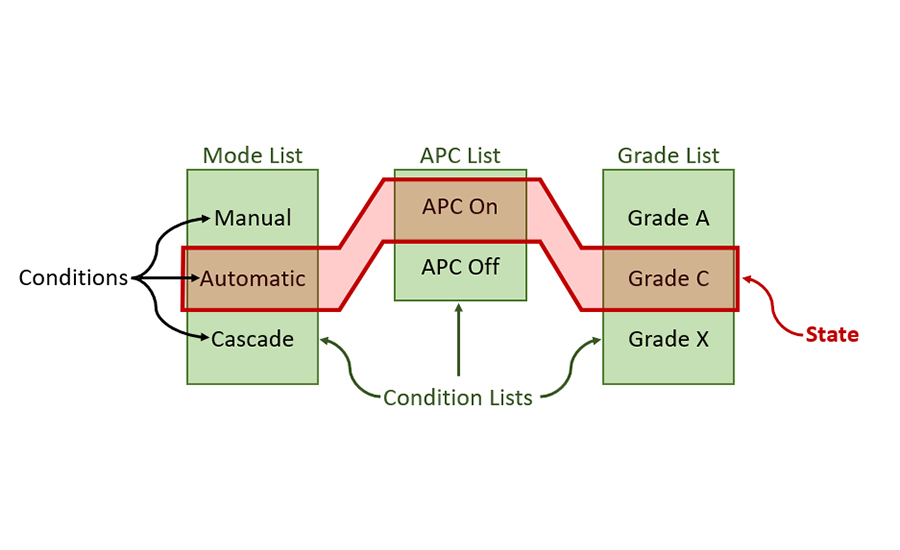
For this operating facility, the CLPM software simply needed to be informed of what product was running, which occurred automatically within the control system. Based on its use of state-based CLPM, the facility identified different conditions where MPC was not living up to expectations. While MPC generally improved the performance when running product “A,” a clear deviation in performance was made apparent when the process switched to running product "B." State-based CLPM was key to identifying the alternative states in which performance deviated.
Modern CLPM Advantages
This new generation of state-based CLPM software provides many advantages for users. For this edible oil processing facility in particular, implementation of state-based CLPM provided operators with an accurate assessment of live operating conditions for each product (Figure 3). This facilitated the calculation of optimal PID tuning parameters that could be applied in real time in conjunction with the MPC system. Supervisory control works best when the regulatory control layer is sound.
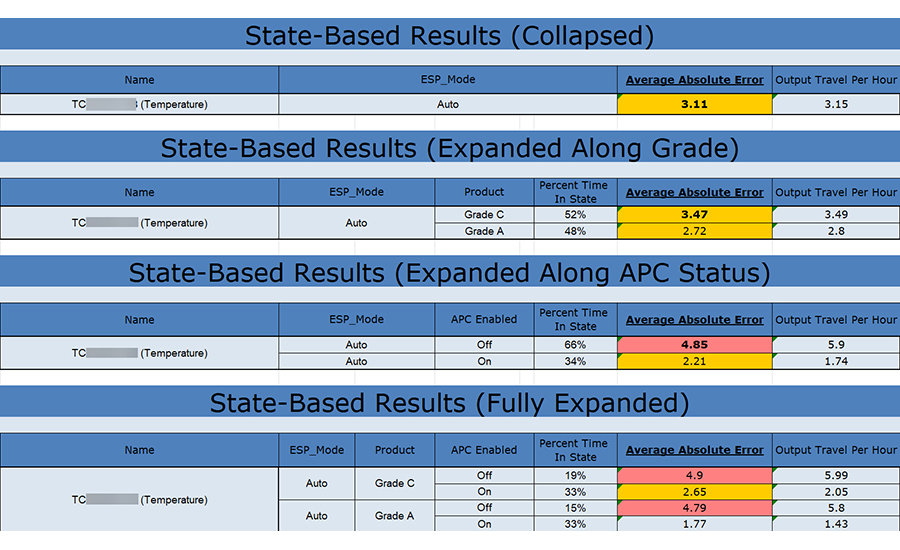
The manufacturer had already made investments in field instrumentation, software configuration, and engineering work to interpret and apply control changes. Once connected to the corresponding controller tags, the CLPM software provided a more precise data-based approach for understanding and solving operational problems.
Operators, engineers and managers now have clear visibility into how the plant is running. Some of the metrics delivered by the CLPM software have entered into the operational dialog, and those metrics provide clarity among workers as they communicate during shift and plant changes (Figure 4). Personnel productivity also increased because lab analysis of grab samples is no longer needed, and sustainability improved because grab samples no longer need disposal.
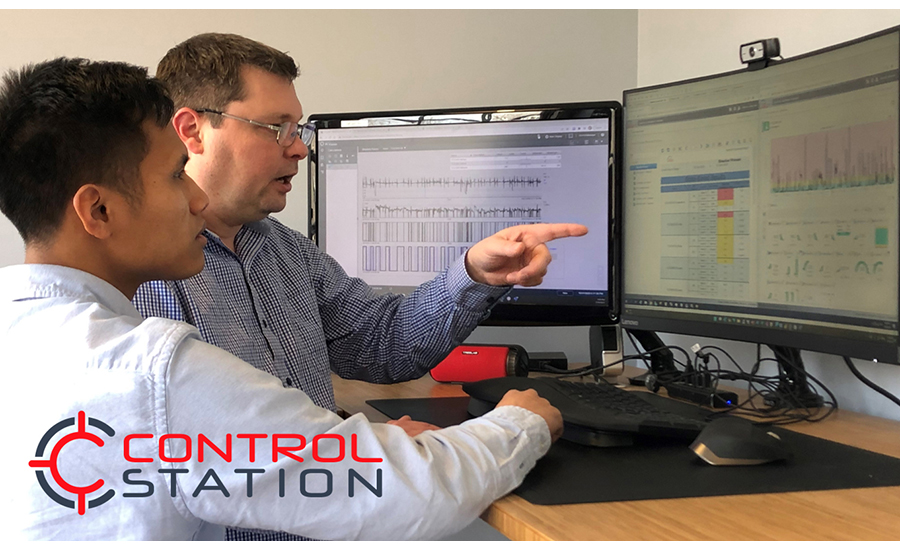
State-based CLPM was initially proven for the localized part of the process where clay was first dosed and then filtered for the facility’s various products. The technology was quickly extended to make improvements in other PIDs, including control of the bleaching process’ back-end temperature loops. These successes have led to an initiative to identify similar opportunities for control improvements within this individual facility as well as across the company’s more than 100 other sites operated globally.
CLPM software is now part of the standard toolkit for the company to improve operational performance, and to then maintain and sustain that performance over time. Analytics on their own don’t fix anything. But putting useful and accessible analytics in the hands of users, through software with advanced features like state-based control, empowers plant personnel to implement continuous improvement.
Looking for a reprint of this article?
From high-res PDFs to custom plaques, order your copy today!