Deploy Mobile Devices on the Plant Floor to Maximize Operator Efficiency
Mobile devices give operators freedom to move about, but user interface design needs careful thought before implementation.

Emerson’s Movicon.NExT software platform provides personalized visualization solutions via WebHMI, web clients, and augmented reality, supporting a wide range of user needs throughout all industries and applications. Image courtesy of Emerson
A year ago we looked at the legal and cybersecurity issues of allowing personal mobile devices—especially smartphones—on the plant floor. In this article we look at the advantages and technical considerations of deploying wireless devices on the plant floor. We especially look at user interfaces and their design, the handling of alarms, mobility issues and the future that brings AI and virtual reality/augmented reality to the world of mobile devices, freeing operators to accomplish tasks that weren’t easily possible with older, fixed HMIs.
Higher Performance Does Not Necessarily Make Technology Easier To Use
With the arrival of Wi-Fi 6 enabled hardware in late 2019 and Wi-Fi 7 scheduled to be ready in 2024—and 5G cellular systems having arrived in 2018-2019—the attraction to deploy wireless systems on the plant floor has become stronger than ever. Bandwidth is greater (albeit sometimes at a loss in range) and interference is generally less, resulting in improvements in data throughput. What this means in practice is the ability to transmit more sensor data and better-quality multimedia and video over a channel without buffering and stuttering. For example, with the recent replacement of an older Wi-Fi router, the extension to the 5 GHz band in Wi-Fi 6 allowed me to view nonstop, high-definition videos on my tablet, which wasn’t possible on 2.4 GHz—they would run for a few seconds before they would freeze, waiting for more data.
While all this improvement in performance is amazing, some apps on my tablet remain confusing, cumbersome and—quite frankly—difficult to use because they’re just not intuitive. Printing is a good example. While it’s easy to print on my Windows or Linux desktop from any application using the familiar CTRL + P keys, printing to the same network printers from my tablet is at best circuitous in nature and uses different printing apps to connect to an HP laser machine or Epson inkjet. Confusing is an understated term to explain printing from my tablet. Imagine having to shut down a packaging machine with such a counterintuitive system.
Fortunately, designers of industrial process control, MES and ERP software have intentionally designed user interfaces (UIs) that are not only intuitive, but place emphasis on the most important functions being upfront and easy to access and use. Web-based technology allows these UIs to resize automatically to fit the device in use—no matter the operating system. In addition, these interfaces are custom tailored for the specific personnel using them, that is to match their job functions.
According to Sanman Mehta, special projects engineer at IOTA Software Inc., forcing operators to switch between many UI systems can be inefficient and taxing in a fast-paced environment and introduces the possibility of human error and overload. “Our software is capable of supporting personnel in various roles, who could be working with the same machines and data but have different needs,” says Mehta. “For example, a rotating machinery engineer would be looking at certain mechanical key performance indicators (KPIs), which differ from those for which a process engineer would be interested. IOTA Vue software is elastic and can dynamically adjust to data and user demands, on any target UI device.”

What Apps Are Great For Mobile Devices?
“The ideal applications for wireless devices on the plant floor include HMI/UI for process monitoring and control, alarm notification, process KPIs, maintenance troubleshooting, VR/AR (virtual reality/augmented reality), and voice assistance (‘phone a friend’),” says Jim Vortherms, CRB senior director, control systems integration.
“Typically, we are observing applications primarily focused on the user interface, monitoring and control, as well as alarm notifications. The other potential uses are gaining popularity, partly driven by staffing shortages and knowledge loss due to retirements and attrition,” says Vortherms.
The next significant push appears to be in wireless maintenance and troubleshooting, providing maintenance technicians with access to troubleshooting guides, drawings, reference documents and remote assistance, adds Vortherms.
“Implemented systems often differ depending on the mobile platform utilized,” says Russell Weekley, manager, automation, Gray Solutions, a Gray Company and Control System Integrators Association (CSIA) member. “We commonly implement alarming notification and escalation for operations and plant-level KPIs and status for management needs delivered via smartphone devices. We have commonly been deploying HMIs utilizing tablet platforms to enable a mobile workforce with increased plant area control. The mobile technologies allow for fewer devices and more specific location-based securities to be implemented.”
From an application software provider’s point of view, such as ICONICS, the ideal applications for smartphones, notebooks and tablets on the plant floor involve getting machine statuses and information and, when warranted, fine-tuning or course-correcting machine performance via a setpoint change or initiating some type of maintenance work order based on the information, according to John Doto, director, professional services – Americas. For example, operators will be able to walk up to a machine and scan a QR code or dive into the app from their tablet to bring up live telemetry or real-time data for a particular machine status.
Also, these applications will allow operators to quickly look up documentation about the machine, like work orders or maintenance scheduling or information from other machines from other systems, adds Doto. Operators can also view trends of KPI metrics. And in the case of platforms with more advanced capabilities (like ICONICS CFSWorX), operators can be notified of an alarm based on their proximity to the problematic asset. For example, the maintenance technician closest to the machine would receive a notification to go to that machine to begin an investigation.
In last year’s article we mentioned various legal issues for not letting employees use their personal mobile equipment on the plant floor. But according to Maggie Slowik, IFS global industry director for manufacturing, there are other reasons for deploying company-issued devices. “The choice comes down to the user, nature of task, budget, preference, IT infrastructure, etc., but it’s important to ensure that all devices used on the plant floor are ruggedized or placed in protective cases to withstand the industrial environment. Within food plants, hygiene is obviously of paramount importance.” Therefore, it’s a good idea to keep employees’ personal devices in their lockers and away from food.
It’s important to remember that mobile devices do have limitations on the plant floor. INFOR offers a MES solution that has the ability to collect machine downtime, production count, scrap, inventory and quality data, according to Joe Russotti, senior director, sales. This type of data can be captured on tablets and PCs. People tend to use phones for looking at reports that are emailed. “Devices like phones are good for viewing data, not necessarily data entry,” says Russotti. “Touchscreen tablets have a larger screen than phones and are better suited for data entry for things like downtime reasons.”
Food processors provide mobile hardware when it is required for operations, says Eric Williams, digitalization group manager, Process and Data Automation (P&DA), a CSIA member. Most core control remains within structured HMIs and SCADA systems. Williams has many clients utilizing mobile add-ons to monitor remote equipment, either inside of a facility or of a larger enterprise—typically located away from facilities’ main processing equipment.
“Many of the systems we deploy are purpose-built for mobile,” adds Williams. “Quality systems that span many people and departments are a great example of this. Our Share to Act solutions for packaging line solutions also fall into this example as they have both multiple machines and a significant physical footprint, all coupled with a low operator count. Operators in these environments interact with not only the line controls but also the warehouse systems for raw ingredients and finished goods. They are also intertwined with maintenance functions, and our clients use them every day to access manuals, videos, and real-time connection to backend support from machine manufacturers.”
Optimizing the UI
It is very critical for end-users to access their data and screens in the appropriate format, be it a tablet or mobile device, says IOTA’s Mehta. Content builders should also be able to leverage the system in which they are building views, so that the end-user has the best experience without needing to switch between various configuration options.
Many of the most popular HMI applications today have the capability to resize the UI based on the device’s format, says CRB’s Vortherms. Many of these applications utilize a web interface or web-based technology, enabling dynamic resizing.
Typically, viewing relevant information for the operator is not an issue unless they are using a cell phone-sized screen. If there is a requirement to ensure that an operator sees specific job-related data on such a screen, a separate session with a dedicated application can be employed to manage the smaller screen size, adds Vortherms.
ICONICS calls dynamic resizing to fit the device and application “responsive design,” says Doto. Users can design graphics and dashboards to dynamically show and hide content based on real-time data, as well as the client device and the resolution. This technology can also resize and reposition visual aspects. For example, if you have a webpage on a laptop, you might see ten tiles across the page. But if you’re looking at this webpage on a mobile phone, the ten tiles might be placed in a single column that you can go through by scrolling down. Most personnel working on a plant floor have the necessary mobile phone/tablet savvy to understand and digest the reoriented visuals, so resizing to fit the mobile device is not an issue.
Wireless Mobile Devices—a Valuable Asset on the Plant Floor
Often-used mobile device applications (due to their immediate impact on productivity and efficiency) include—but are not limited to—the following:
- Machine status monitoring: Operators can quickly view the status of various machines, see if they’re operational, idle or down, and monitor other critical parameters without needing to be physically present at the fixed UI station.
- Real-time alerts and notifications: Mobile devices allow operators and maintenance personnel to receive immediate notifications of alarms, machine faults or other critical events, ensuring quick response times.
- KPI dashboards: Managers and supervisors can monitor key performance indicators (KPIs) in real-time, comparing current production rates, efficiency, quality metrics, etc., against targets.
- Remote control: Some applications may allow for remote control of certain machine functions, especially for processes that don’t require immediate physical intervention.
- Training and augmented reality (AR): With the rise of AR technology, mobile devices can overlay digital information—such as schematics or step-by-step instructions—on the physical world, aiding in training and troubleshooting.
- Energy efficiency: Mobile devices are helpful tools for tracking and controlling energy use. Operators and energy managers can see real-time data on how much energy is being used, find patterns and make changes to save energy.
- Inventory management: Operators can scan barcodes or QR codes using mobile devices to track raw materials, finished products or spare parts, ensuring accurate inventory levels and reducing manual data entry.
- Quality control and inspections: Quality inspectors can use tablets to input inspection data, view tolerances and standards and document any deviations with photos or notes.
— Chiara Ponzellini, Software Commercialization Product Manager, Emerson
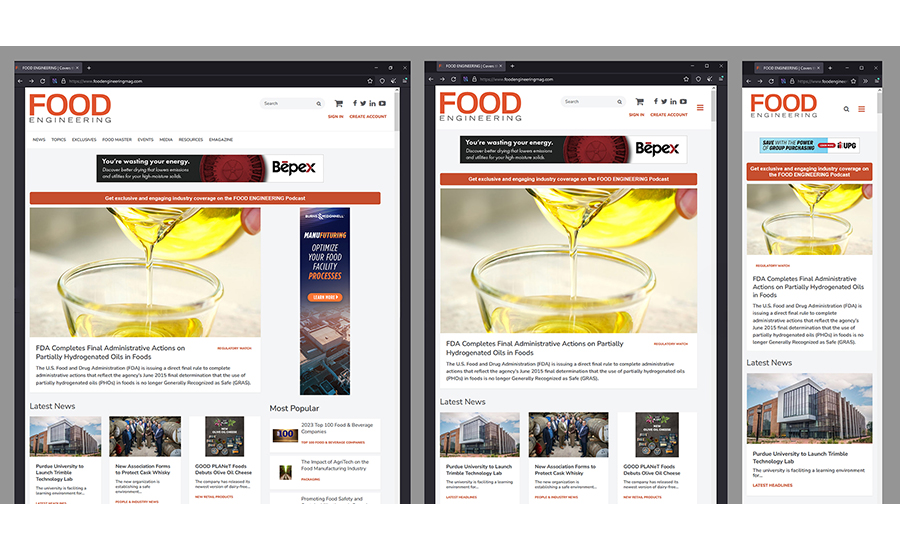
From a programming standpoint, UI developers should configure their graphics to meet the requirements of the application, says Doto. Of course, users can create a graphic that’s only legible on a laptop, but if their design didn’t make use of a responsive design approach, it won’t scale. When users build graphics with responsive design in mind, those applications very easily adapt to various resolutions and client devices and allow personnel to be mobile.
It is the type of application that determines which information should be displayed on which device, says Chiara Ponzellini, software commercialization product manager for Emerson’s controls and software business. For example, in a large food manufacturing company, in a control room, you can supervise the entire system, while at individual workstations, you can display details of the production line and machines. On pages viewed on mobile devices, only the most relevant data such as alarms or production efficiency data might be shown. All of this is possible through a single software solution and a unified development environment.
“For instance, one of our customers, a top Italian wine company producing over 300,000 wine bottles daily, wanted to show the status and efficiency of their bottling lines using pie charts on HMI Panels,” says Ponzellini. These easy-to-read graphics help operators keep an eye on how well machines like the depalletizer, filling machine, pasteurizer, labeling machine, packaging machine and palletizer are doing. The production line values in these charts show how efficiently the machines are working.
When processors use IFS on a mobile device, the page resizes and allows for the most pertinent information to be displayed, says Slowik. There should be no need to have separate versions for different devices. Each user will log onto the system with their user ID which will only allow them access to the transactions the system’s inbuilt security allows, (which is set by a systems administrator).
It’s important to remember that a small screen simply shouldn’t offer all the functionality of a dedicated HMI. Screens tend to become less graphically intense as they shrink, says P&DA’s Williams. “Furthermore, you must plan to remove controls for things that you don’t want operated via mobile, and this helps drive the operators to the equipment and local HMI for items that they should have eyes on before engaging for actual control.”
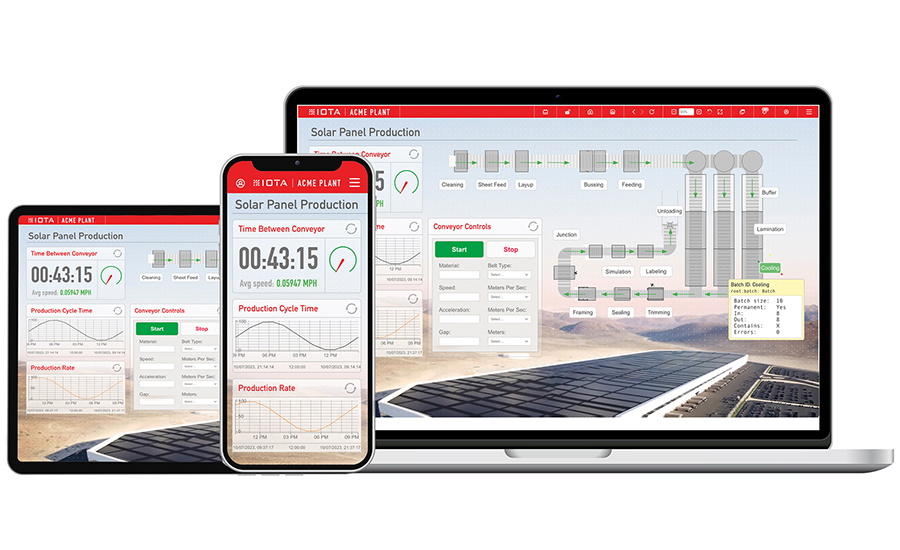
Optimizing Mobile Devices and Alarms
The first step in optimizing the UI for effective alarm monitoring is to conduct “Alarm Rationalization” on the system, distinguishing alarms from alerts, says CRB’s Vortherms. Alarms necessitate operator intervention, while alerts provide information or are part of the standard process.
When designing UIs it is important to understand the priority of the data to identify the most critical parameters that operators must monitor and to have a hierarchy of needed alarms, says Ponzellini. “Emerson’s Movicon.NExT provides a solution for configuring and sending alarm and event notifications to designated recipients, including on-call personnel, called Alarm Dispatcher. Using this solution, you can specify which events and alarms trigger notifications and choose the recipients. This is accomplished through various communication plugins, such as SMS, Email, VoIP, Telegram.”
How do you physically get the operator’s attention when an alarm condition comes up in a noisy environment? If operators are equipped with mobile devices and the plant floor noise levels are high, one option is to use Bluetooth-enabled, noise-canceling headphones, says Vortherms. These headphones protect the operator’s hearing while enabling message transmission or alarm notification. Integrating human-generated messages would require additional integration with the system. Another commonly used option in noisy environments is the use of lights to signal alarm conditions to operators. If operators have mobile devices with tactile notifications (vibrate), these can also be used to notify them of a text message or email from the control system.
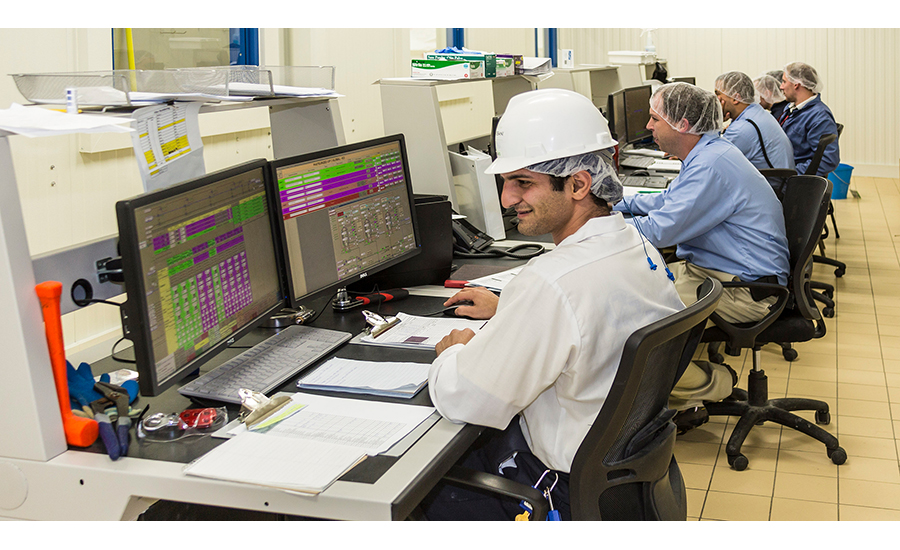
“We typically do not recommend headphones for use on the plant floor for communication or notification of alarms or status,” says Gray’s Weekley. The use of earbuds and many other headphone-type devices would not fit many manufacturers’ material safety policies. In addition, headphones typically provide a safety concern due to the distraction they would provide to the ability to communicate effectively in key situations.
“In the plant environment, we typically propose and implement alarm notification via HMI screens with a combination of ISA 101 style alarm depiction and ISA 18.2 guided alarm management to provide operations with key alarm information in a prioritized manner,” says Weekley. “For key alarm scenarios that require more immediate attention, we often will implement light stacks to give visual indication to the existence of a problem. On the plant floor, audible alarm horns may also be installed, but we typically reserve the implementation of these devices as a last resort.”
Another option is the use of large, overhead easy-to-read displays/monitors, which allow operators to quickly identify alarms and their source, says Slowik. “I imagine quite a few manufacturers still use visual alerts (attention-grabbing colors and flashing) because they are more reliable in noisy environments and can be integrated into the machinery itself.”
Looking Forward
Operations and maintenance assistance represent valuable applications for AR/VR technology when combined with mobile devices, says Vortherms. These technologies can be employed to enrich the information available to technicians or to facilitate remote subject matter experts (SMEs) in assisting from a remote operations center.
Suppliers like Emerson are already integrating AR solutions for its HMI/SCADA systems, for example its Movicon.NExT platform. With wearable AR devices like Android smart glasses and Windows 10-based HoloLens, operators can easily manage processes and access real-time data. AR systems usually complement traditional workstations rather than replacing them, says Ponzellini. For maintenance, AR systems let users view onscreen guides, like manuals and troubleshooting videos, and communicate with the operations center wirelessly. This helps prevent mistakes during procedures by giving users instant access to the right info.
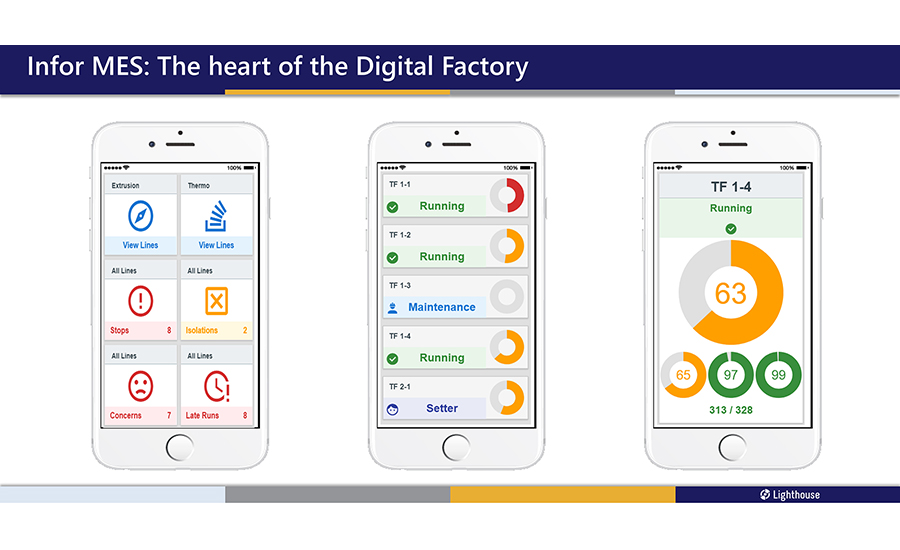
According to ICONICS’ Doto, the combination of AR and mobile devices will help operators/technicians to ensure product consistency by overlaying quality control checklists and guidelines onto products moving along production lines and guarantee quick and accurate completion of maintenance tasks through access to step-by-step instructions, diagrams and even remote assistance from experts.
With VR and mobile devices, operators and technicians will be able to create simulations to practice maintenance and repair procedures on virtual equipment. They can also create immersive simulations to practice operating new and unfamiliar machinery or deal with emergencies in controlled environments, says Doto.
Finally, in conjunction with mobile devices on the plant floor, the use of AI will give operators and technicians additional insight to process optimization, energy efficiency, predictive maintenance, and quality control, just to name a few, says Doto. For one, AI can analyze production data to identify areas to improve efficiency and send recommendations for process adjustments to operators/technicians. Additionally, AI can analyze sensor data to predict when maintenance is required. Operators/technicians can be alerted prior to issues, so they can take appropriate measures. AI is also being used for quality control to inspect products and predict which manufacturing aspect needs adjustment/attention. Overall, mobile-friendly technology allows operators/technicians in the food industry to have more flexibility when interacting with their systems. And with advanced software users can customize a set of features that best suits their needs.
Looking for a reprint of this article?
From high-res PDFs to custom plaques, order your copy today!