CASE STUDY
Smart Flow and Weighing Technology Mean Sweet Process Success
Specialists in the centuries-old tradition of making candied fruit, APTUNION depends on modern Siemens instrumentation—from flow control to intuitive weighing technology—to ensure its sweet products meet the highest quality standards.

APTUNION produces 10,000 tons of dried and candied fruit products per year. All images courtesy of Siemens
BY CHRISTOPHE BARBIER AND ERIC PASCAL
Candied fruit has been carefully made in the south of France’s Apt region for more than 700 years. With a range of dried and candied fruit products used in everything from baking and pastries to chocolate and cereals, the company APTUNION formed in 1962 when several family-owned confectionery manufacturers joined forces.
The company’s 250 workers at this facility in Apt produce 10,000 tons of product per year—sourced from more than 200 local farmers across Provence. A skilled team of specialists designs production lines that can be adapted to customer needs, manufacturing complex products that comply with the highest quality standards.
One such production line makes fruit pieces (or fruit chips), which use a unique process that sees fresh fruit purees of raspberry, apple, strawberry or citrus fruits textured with pectin and then dried. Pectin is a natural gelling agent made from the skin of citrus fruits, rather than using additives like calcium.
Once dried, cut into sizes from 1mm to 1cm, and packaged in small to 10-kg bags, these fruit pieces are then shipped worldwide to manufacturers of products such as chocolate, cereal bars and energy bars in more than 50 countries around the world.
Smart Processes for a Modern Agri-food Plant
APTUNION recently undertook a project to create a new manufacturing facility, modernizing its production center and moving machinery from one site to another. Food safety certified BRC Grade AA, the new factory means the company could double its production.
Among the modernization efforts, technicians installed five Siwarex WP321 weighing modules, connected to a stainless steel Siwarex DB digital box. This system relays accurate and repeatable weight measurements directly to the control room so operators have the information they need for each of the varied products APTUNION produces.
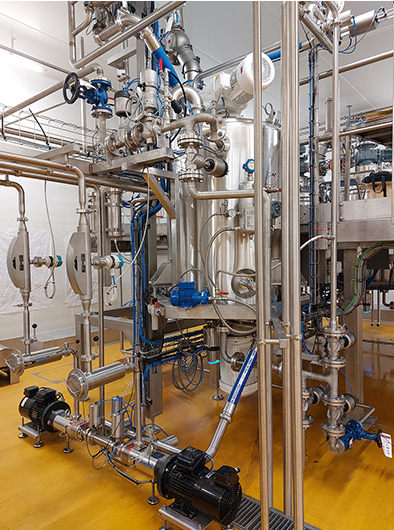
The Siwarex DB digital junction box excels in both retrofit or new-build applications—and paired with the Siwarex WP321’s four-million-part analog-to-digital converter, the weighing system delivers high accuracy with the plant’s existing load cells.
Siwarex DB combines the best of both worlds: The ability to retrofit the facility’s analog load cells while still benefiting from the diagnostic information available with digital load cells. The digital junction box’s features work well in brownfield plant builds: Technicians simply need to replace existing junction boxes with Siwarex DB instead of the more complicated—and expensive—task of replacing mechanics or cables.
The company also replaced its electromagnetic flow meters with five mass flow meters, which avoid volume conversions during the continual dosing of gelling agent and fruit in each recipe. And because the gelling agent is extremely viscous, flow instruments need to ensure a certain flow rate with a high viscosity amplitude.
One of the most compact Coriolis flow sensors on the market, Siemens Sitrans FCS300 did just that—providing operators with precise measurements of gelling agents to guarantee recipe control. The flow meters’ small size simplifies installation and replacement, giving plant designers the ability to optimize factory layout by fitting the multiple units into tight spaces.
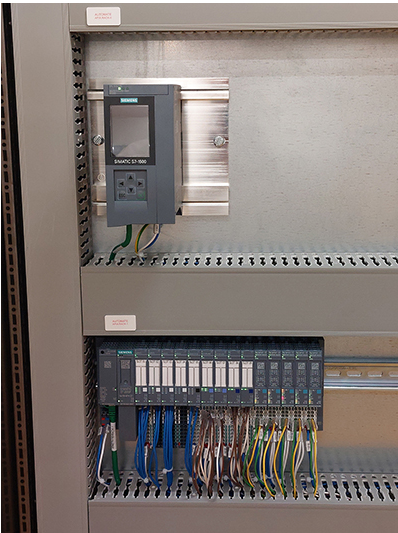
The Sweet Success of Smart Instruments
These eyes and ears of the manufacturing process are connected to the brain of Siemens’ Simatic S7-1500 PLC, which all of APTUNION’s maintenance engineers were already trained on before the company embarked on this modernization project.
With improved preventative maintenance, these operators can assess and diagnose any load cell issues remotely—since they receive error reports for each connected load cell either centrally at the Simatic controller or on the local HMI panel.
This continuous integration with Siwarex DB allows operators to analyze more comprehensive data than ever before—targeted monitoring of weighing processes with simplified services. For example, rather than checking the junction box manually at the scale itself—which can involve stopping production and often requires higher technical knowledge from a weighing specialist—APTUNION’s own plant staff get the information they need from the comfort of the control room.
“Without needing external service from weighing specialist, our operators can control the scales and ensure their proper functioning,” says plant manager Florian Latournerie. “We gain excellent process control across all of our recipes, meaning reduced product loss from non-conformities in manufacturing.”
As APTUNION continues its automation journey, Siemens instrumentation and weighing technology will be there to support them with process control and ease of use essential to their operations.
Looking for a reprint of this article?
From high-res PDFs to custom plaques, order your copy today!