Technology Sourcebook
Vertical blender

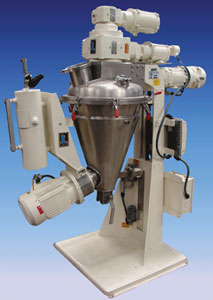
Charles Ross & Son Company; 800-243-ROSS; www.mixers.com
Looking for a reprint of this article?
From high-res PDFs to custom plaques, order your copy today!
Charles Ross & Son Company; 800-243-ROSS; www.mixers.com
Looking for a reprint of this article?
From high-res PDFs to custom plaques, order your copy today!
Copyright ©2025. All Rights Reserved BNP Media.
Design, CMS, Hosting & Web Development :: ePublishing