TECH FLASH
Good chiller maintenance practices for winter
As the temperatures start to drop, the proper maintenance and cleaning of chiller systems after shutdown can help avoid future problems.
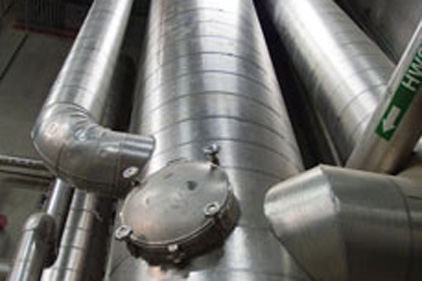
As the winter begins to creep in and temperatures start to drop, the proper maintenance and cleaning of chiller systems after shutdown can help avoid future problems.
“Our experience is that being proactive and taking a look at the chiller system in the early winter lead to better results in the spring when it’s time to start up the system again,” says Tim Kane, president and CEO of Goodway Technologies, a company that engineers and builds maintenance solutions for commercial HVAC systems. “Performing chiller maintenance as early in the winter as possible gives facility managers the benefit of finding major damage with plenty of time to fix the problems before the chiller needs to be back in operation.” Delaying maintenance, Kane says, can lead to more repair costs and lost production time.
According to a survey conducted by Goodway, 89 percent of respondents say chiller maintenance is performed once a year at their facilities, with more than half reporting this maintenance occurring between January and March.
To improve chiller maintenance and maintain equipment that runs properly and efficiently, Goodway recommends five steps:
1. Maintain a daily operating log: The Federal Energy Management Program (FEMP) recommends updating the log four times a day to monitor key operating parameters that will help indicate if any problems are developing.
2. Keep tubes clean: Fouling and scale can reduce efficiency. Regular monitoring can help identify when tube cleaning should take place; it is recommended at least once a year. Pressure loss can also indicate tube corrosion.
3. Ensure a leak-free unit: Leaks can affect the operation of the system and release hazardous refrigerants.
4. Sustain proper water treatment: Failure to perform chiller maintenance can also affect water quality. Keep a close eye on water treatment and chemistry.
5. Analyze oil and refrigerant: Refrigerant levels should stay within the manufacturer’s recommended levels. An air-purge timer, checking the refrigerant sight-glass for bubbles and checking at all joints and connections with a gas analyzer help track refrigerant levels.
“Chiller systems are some of the more complex pieces of equipment in a plant or facility, and it’s worth making the investment to take care of them,” Kane says.
Thirty-nine percent of respondents say they measure the efficiency gains resulting from chiller cleaning. Those who do measure efficiency gains use temperature monitoring (77 percent), pump pressures and other immediate indicators (41 percent), and energy costs over time (25 percent).
Looking for a reprint of this article?
From high-res PDFs to custom plaques, order your copy today!