Packaging
How to avoid dreaded packaging downtime
Better design leads to improved uptime

Yaskawa Motoman’s Smart Series line of robots and controllers achieve quick changeover through a simplified programming experience.
Photo courtesy of Yaskawa Motoman

Harpak-ULMA will unveil a Mondini Trave 1000 VG full Allen Bradley Execution at PACK EXPO Las Vegas. Machines with the Allen Bradley systems will have diagnostic ability to monitor critical machine parameters and recommend preventative maintenance.
Photo courtesy of Harpak-ULMA Packaging

The Model XYRJ bagger from Triangle Package Machinery Company offers flexible packaging changeovers with a jaw that rotates 90 degrees. It runs pillow bags, three-sided seal pouches and standup pouches.
Photo courtesy of Triangle Package Machinery Company



When it comes to packaging equipment, preventing downtime is a priority.
To keep the machines running and minimize downtime, processors identify several attributes as deciding factors when buying or upgrading equipment:
- Flexibility for recipe, pack style and packaging to stay competitive long term
- Reliable technology to help with quick changeover
- Easy access for cleaning and maintenance, and a simple, fast changeover process
- Robust design to endure factory conditions and reduce mechanical failure
In addition, hygienic design is the cornerstone of not only keeping food safe, but also for maximizing uptime. The reason is simple: Better design equals less time spent cleaning.
A machine that’s easier to clean can save hours of idle time, especially in industries such as poultry, meat and shrimp where cleaning is a critical component of downtime, says Kim Magon-Haller, marketing director of Triangle Package Machinery Company.
The company’s machines offer access to all internal components to help processors not only clean machines more efficiently, but also more effectively.
“Remember, you cannot clean what you do not see!” says Magon-Haller.
As processors struggle to find enough qualified operators, more companies are looking to automate primary and secondary packaging. They want minimal tools or no tools for changeover and formats that aren’t cumbersome. And fast changeover needs will grow with the trend of small, personalized batches and custom product mixes.
If you’re looking for a new packaging machine, ask whether it offers easy access for maintenance and cleaning, preheating devices for tool changes and washdown capability. And to help minimize planned and unplanned downtime, you’ll likely need one of the burgeoning digital solutions to train and guide workers on operation, maintenance and cleaning.
Quick change
Magon-Haller describes the difference between machines with and without quick changeover capabilities using Triangle’s Flex 1 Cartoners as an example.
For companies running bag-in-a-box applications, the Flex 1 Cartoner – Gen 2 features simple changeovers in less than 20 minutes. “This is a great advantage over traditional cartoners, which can take hours to manually adjust components and settings in order to switch carton sizes,” she says.
An even faster solution is the Automatic Changeover Wizard that Triangle introduced last year on its Flex 1 Cartoner – Gen 3. It enables automatic, repeatable carton size changeovers in only five minutes.
“Operators need only push a button to launch a stored recipe for single package cartons, rather than dealing with complicated tools and manual adjustments,” she says. “In addition to saving time that may have been wasted making manual adjustments, they’re spending less time on training, gaining improved efficiencies and reducing product waste.”
With the Changeover Wizard, one customer with frequent switches reduced changeover time by 75%, Magon-Haller says. Plus, the feature eliminates “operator tweaking” that often happens with manual changeovers.
Good design=less downtime
Reducing downtime is the second most important factor to Harpak- ULMA Packaging customers after hygienic design/food safety, says Carlo Bergonzi, technical sales administrator. “It ultimately factors into the overall efficiency and value of the equipment. It is very costly to have labor units idling while production is effectively zero.”
A well-designed machine with minimal vibration and moving parts reduces mechanical failure, Harpak-ULMA Vice President Jim Ryan says. Weight helps too: The Mondini 590 XL tray sealer is 12,000 lbs. and has I-beam framing to cut vibration. The moving parts are limited to the belts, pusher arms, lower tool lift and springs of the upper tool.
“A machine with less moving parts is a more efficient machine,” Ryan says. “Less moving parts means less wear, thermal stress, vibration and fatigue loading, which can contribute to failures.”
The company’s machines have more reliable assemblies and less electronic components. The tray sealer only uses one heating element and thermocouple per lane instead of per sealing head to greatly reduce failure points, Ryan says.
How robots help
When Yaskawa Motoman robots help pack products, downtime reductions most often are achieved through a simplified programming experience, dynamic offline programming and simulation tools, says Dean Elkins, segment leader, material handling, Yaskawa America Inc., Motoman Robotics Division.
“As production runs decrease in size, it is very important that fast changeover occur via a simple control interface and simple manual changeover routines,” he says.
Activities such as changing robot programs, tool changing, and the adjustment of conveyor guides and rates are often accomplished through a setup in a human machine interface. “While this requires upfront programming to accomplish, time is saved on the backend due to minimized keystrokes required for the changeover to occur,” he says.
A major bagged snack manufacturer that uses Yaskawa robots has its entire manufacturing line programmed through a PLC, Elkins notes. The robot motion and tooling are completely driven via the ladder logic associated with the PLC. One-touch changeover is accomplished in tooling adjustments and robot motion changes through the HMI.
To help speed cleaning time, Yaskawa always strives for higher IP ratings to make the robots more impervious to moisture.
A risk assessment for worker/machine safety that takes all changeover aspects into account should be performed on a work cell, he advises.
Service requirements
With worker shortages, evaluating the quality of the training and maintenances services from OEMs is more important than ever.
Yaskawa Motoman offers remote courses on operation, programming and maintenance through its training academy to help ensure workforce readiness. Its easy-to-use, web-based RobotPro software allows customers to access maintenance and repair solutions for specific robots.
Bosch’s Maintenance Assistant is a visualization app for operators, maintenance and service staff. Directly connected to the machines, it provides real-time data and helps operators to reduce downtime for scheduled maintenance, such as cleaning, adjustment or replacement, says Stefan Kleinmann, director of marketing and business development, business unit food, Bosch Packaging Technology.
Engineers and plant managers can create step-by-step descriptions, including text, images and video for specific operations, such as cleaning or format changes. Storing documentation and sharing data in the network improves processes.
“We offer digital solutions that empower and guide employees as to what, when and how to do the right tasks on the shop floor in a quick and easy manner,” Kleinmann says.
Harpak-ULMA is moving toward full Allen-Bradley systems that will have diagnostic ability to monitor critical machine parameters and recommend preventative maintenance. These machines will allow the company to collect data to refine processes and develop predictive maintenance models to prevent failures using artificial intelligence, Bergonzi says.
In September, the company will unveil the Mondini Trave 1000 VG full Allen-Bradley Execution at PACK EXPO Las Vegas. It will have Allen-Bradley PLC, PanelView HMI, and servo drives and motors.
Harpak-ULMA also introduced an augmented reality technology called Chalk that allows technicians to communicate with operators on the floor. “Harpak-ULMA troubleshooters can mark and indicate through the Chalk interface in three dimensions, which allows the operator on site to clearly see in real time the area of the machine that needs to be addressed,” Bergonzi says.
New operators can use the AR feature to learn instantly how to perform changeovers and other tasks. “This allows us to quickly get workers up to speed and skill in regards to the equipment,” he says.
Not ready for a new machine?
Sometimes the best solution is not replacing machines but retrofitting or partially modernizing the equipment you have.
Rebuilds can be very effective in returning a machine’s efficiency, Bergonzi says. Harpak-ULMA often rebuilds long-lasting Mondini tray sealers.
“We have recently rebuilt three E590 VG grind line tray sealers that are nearly 15 years old,” he says. “Depending on what comprises the line, it is possible to replace a sealer and maintain the existing filling and conveyance equipment.”
This provides upgraded technology without full capital expenditure. Soft rebuilds include replacing gaskets and other small wear parts.
With robots, processors often can place them in spaces to mitigate the need for a custom conveyor or transfer device, Elkins says. “The beauty of robots is that they can fit right into systems that cannot be completely redesigned.”
In many cases, Triangle can retrofit a machine to run a new bag style, Magon-Haller says. The company continually is finding ways to make updates work for existing platforms, such as control box upgrades with the latest hardware and software.
Specific needs, specific help
An OEM should form a close relationship with processors to learn about plant processes and product characteristics that will affect downtime. Bosch uses specific requirements to create new products and services, Kleinmann says.
He points to sticky bars and nut products as an example. Machine design helps customers minimize cross-contamination without sacrificing efficiency. “A comprehensive hygienic design directly influences the cleaning time requirement for a system,” Kleinmann says. “The lower the accumulation of contaminants and the easier the machines are to clean, the shorter the downtimes for cleaning.”
Triangle’s Automatic Changeover Wizard is an example of collaboration between engineers and customers, Magon-Haller says. It resulted from the request of a Fortune 500 food processor looking for a recipe-driven, simple changeover process. “In response, we created an all servo changeover system based on visual prompts and instructions built into the HMI,” she says.
A barcode scanner allows operators to easily match the code on a product recipe in the HMI with the product or film roll to confirm that they’re running the correct package. The verification cuts downtime.
For Harpak-ULMA, continuously improving efficiency features requires taking feedback from processors and rolling out new options that attack the issues head on. Specific characteristics or challenges often require custom solutions, Ryan says.
Harpak-ULMA developed special infeed conveyors for Mondini tray sealers for products that deposit grease onto the transport surfaces. And it offers special sealing heads for tough lidding skin applications. The company customizes pusher arms and rail systems to accommodate each product.
Sometimes, some good advice from an equipment manufacturer makes a difference in packaging line efficiency.
Harpak-ULMA may advise customers to use multiple fillers to avoid additional sanitation time during changeover, for example, Ryan says. “A comprehensive view of a packaging line is often required for the proper solution.”
Yaskawa Motoman often is involved in the very early stages of packaging design to consult on whether a design is suitable for automation, Elkins says. Designing for automation allows for a more predictable outcome of the overall packaging solution, including conveyor and gripper designs.
Monitoring production variables through software, such as Yaskawa Cockpit, which allows internet monitoring of robot work cell performance to maximize output, helps ensure that the system is running efficiently after changeover operations occur, he says.
More ideas to trim downtime
Triangle collaborates on solutions to minimize downtime in a variety of ways. For example, the company began offering ultrasonic cold sealing technology as an option on vertical form fill seal baggers to help its produce customers improve seal integrity and reduce rejects. The technology saves time normally required for sealing jaws to heat up and seals right through product, pushing it completely out of the seal area.
The feature has helped customers in produce and powders, such as baking mixes or spices, significantly reduce downtime. “After a changeover, the first bag (and all subsequent bags) is a ‘good bag,’” Magon-Haller says. “There is no tweaking necessary, which is an advantage not offered with heat sealing.”
Here are some features its X-Series vffs bagger features that help cut downtime:
- Simple tool-less changeover of forming tubes, sealing jaws and film rolls. On the typical model, changing the sealing jaws takes less than two minutes.
- Center-lining feature using color-coding methodology to allow users to make fast and precise forming tube and film roll changes.
- Convenient start/stop button on the back of the machine for quicker film roll changeovers.
- Optional dual position film roll feature, which enables roll changes in less than a minute.
- Accommodates a 24” diameter, 31.5” wide film rolls in many models for considerable downtime savings.
A confectionery company’s quick-change cartoner search
Brunberg OY, a Finnish family business known for its truffles and chocolate marshmallow kisses, was looking for a new solution to package its chocolate marshmallow kisses into cartons. The cartoner needed to be highly efficient, yet flexible enough to respond quickly to changes in packaging style and/or product. Other important criteria were related to user-friendliness: an intuitive HMI, fast format changes and cleaning, as well as ease of operation.
The Sigpack TTM1 from Bosch Packaging Technology, designed for secondary packaging of virtually all primary wrapped food, proved to fulfil the company’s requirements. Scalable up to 100 cartons and up to 1,500 products per minute, it features patented changeover with vertical restart. This is easy, fast, tool-less and reproducible from the first carton onward. The candy maker can run diverse package styles and formats on one machine. The Sigpack TTM1 is reliable thanks to 100% carton control, designed for 24/7 operation and optimal OEE.
Brunberg’s chocolate marshmallow kisses are produced in various flavors and packaged in two carton formats. At an output of 200 products per minute, six chocolate marshmallow kisses, three pieces in two rows, are packed in a small retail carton. The second format is a large display carton with a total of 25 chocolate marshmallow kisses, five pieces in five rows. The Sigpack TTM1 allows the company to further improve its performance and introduce new pack styles in the future.
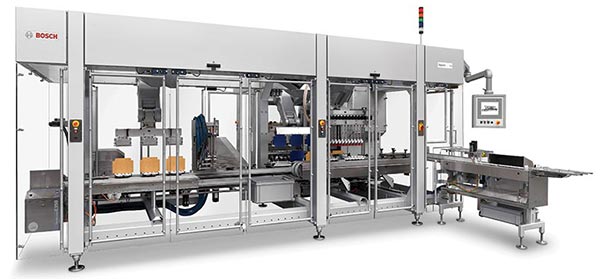
For more information:
Bosch Packaging Technology, www.boschpackaging.com
Harpak-ULMA Packaging, www.harpak-ulma.com
Triangle Package Machinery Company, www.trianglepackage.com
Yaskawa Motoman Robotics, www.motoman.com
Looking for a reprint of this article?
From high-res PDFs to custom plaques, order your copy today!