How two industry leaders invest to save the water supply as scarcity grows
Kraft Heinz and Nestlé Waters North America sustainability leaders say protection of the lifeblood resource will require looking outside the factory walls

With water stress a growing concern, food and beverage companies are investing to cut usage, increasingly looking outside their factory walls to conserve a lifeblood resource for the industry.
Photo courtesy of Getty Images

In Poland, tomato growers for the Kraft Heinz tomato paste and ketchup brand Pudliszki suffered a severe drought in 2018. Most of the farmers don’t use irrigation, but they were able to salvage the crop that year because of sustainable growing techniques implemented with Kraft Heinz years earlier.
Photo courtesy of Kraft Heinz

One example of sustainable growing techniques used by Kraft Heinz farmers is locating fields in varied regions with different soil types, helping provide stable yields in different weather conditions.
Photo courtesy of Kraft Heinz

You can’t make ketchup without adequate water, and Kraft Heinz has goals to help protect the resource.
Photo courtesy of Kraft Heinz

Third-party hydrologists trek into Arrowhead Springs in California to conduct stream and spring measurements for the Nestlé Waters North America certification under the Alliance for Water Stewardship Standard.
Photo courtesy of Nestlé Waters North America





More and more, food and beverage processors are trying to slash water use to meet environmental protection goals that consumers favor.
That approach is somewhat of a turnaround from decades past when water conservation was more of an afterthought for the industry, among the top for water consumption. After all, water typically has been a less expensive and less volatile utility than other energy sources, and factories simply need certain amounts of water as an ingredient and for cleaning and processing.
Efficiency projects have always been welcome: reusing some water, monitoring usage with a sensor, or plugging a leak to save some money. Those projects that chip away at water usage are the building blocks of water sustainability initiatives in the industry.
But today, ubiquitous sustainability plans outline ambitious water-cutting goals that sometimes require investment without 100% ROI, and more manufacturers are starting to think about how to go beyond plant efficiencies to protect the water supply in the communities surrounding their plants. At many facilities, especially in areas that could face scarce water supplies in coming decades, food and beverage processors need to rack up all the smaller savings they can find, plus they often implement significant technology investments to secure larger reductions.
The prominence of water is rising, says Jonah Smith, global environmental social governance lead for The Kraft Heinz Co. People are paying more attention to how water impacts life because of varied recent concerns—from climate change and more extreme natural disasters to water supply threats like lead contamination in Flint, Mich., he says.
Learn more about the technology processors are using to reduce and reuse water
Though energy conservation savings outpace water reduction savings because energy costs more, Smith says the true cost of water becomes clearer when you think about the consequences if the supply were to become unstable. Hypothetically, if the company lost water intakes and was short of that key ingredient to make Heinz Tomato Ketchup (in 97% of U.S. households), the business impact would be significant, he explains. “That's the kind of true costing that as a company you want to assess in a more comprehensive approach—risk and opportunities,” he says.
Kraft Heinz and Nestlé Waters North America shared details about their water stewardship plans with Food Engineering.
▶ Kraft Heinz wants to protect water sources now to prevent shortages someday
▶ When you’re in the water business like Nestlé, keeping the resource renewable is critical
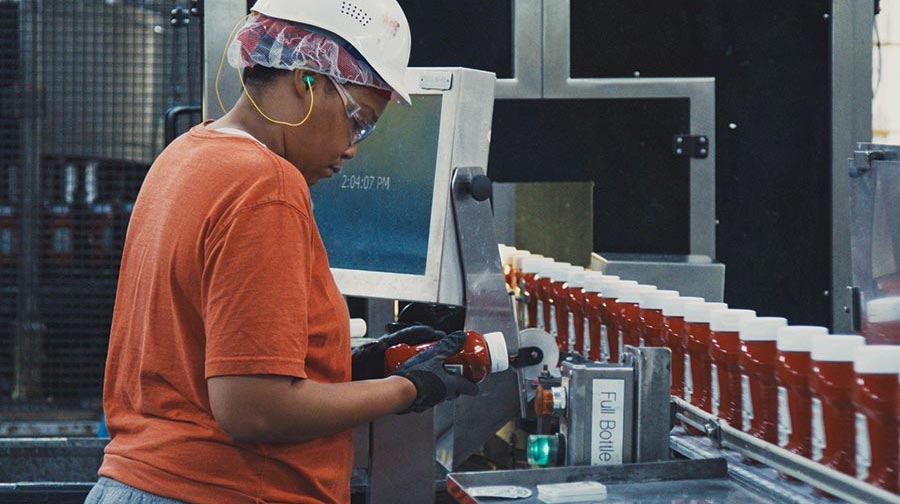
Kraft Heinz wants to protect water sources now to prevent shortages someday
Kraft Heinz, like so many food processors, wants to trim water use at plants—up to 20% at facilities in areas facing water stress in the coming years.
But beyond those goals, the company wants to expand its water sustainability efforts to work with nonprofits, other businesses and communities to help proactively protect the water supply itself, instead of reacting to a possible problem in the future, says Jonah Smith, global lead, environmental social governance.
"We know water is vital to life. It's vital to our business. It's a key ingredient in our business throughout our value chain. So we understand the value of water, and we understand how Kraft Heinz can be a good steward for our business, as well as the environment.”
Amid a flurry of recent news about the Kraft Heinz turnaround plan, including $2 billion in cost cuts over five years and increased marketing investments in high-growth products, the company released its second Environmental Social Governance report since the two giants merged in 2015. The plan outlines 17 sustainable development goals for the environment, agriculture and healthy communities, such as improved packaging recyclability, sustainably sourced tomatoes, salt and sugar trimming, and water use cuts of 15% by 2025 across all facilities.
Smith finds it interesting that water likely impacts most of the goals. “On so many of them (the goals), you could plaster water there and show how that also impacts life on land, that also impacts industry, that also impacts communities, that also impacts health and well-being. Water is really a tying ingredient, not just throughout our entire value chain but throughout the entire world."
At the plants, Smith says water reduction efforts will vary based on individual challenges and opportunities, including any number of operational or technology adjustments, such as:
- clean-in-place systems
- short interval controls
- dry lube on conveyors
- waterless cleaning and sanitation methods
- HVAC optimization, using condensation water
- real-time monitoring for any helpful changes, such as tracking boil time so it doesn’t last longer than needed or fixing a leak immediately instead of getting to it weeks later
The water reduction goals will be a challenge because the company’s water use across manufacturing facilities increased by 1% from 2015 through 2019, missing 15% reduction targets.
But Smith says the company learned from some successes, including an effluent water recycling project that saved 86 million gallons a year at its Oscar Mayer plant in Newberry, S.C. The plant leveraged its dissolved air flotation system to cool vacuum pump seals.
Accountability is built into the plan, with team members all the way up to the CEO assigned KPIs on water conservation and other initiatives, Smith says. Plus, the company’s goals are augmented by its new commitment to the CEO Water Mandate, requiring global water conservation measures, such as upgrading water treatment plants or encouraging growers to save water.
While some plants will need a major savings project like the one in South Carolina, Smith says smaller efforts can add up when implemented at the global scale for a company the size of Kraft Heinz. “There are going to be sometimes where we can get the low-hanging fruit: ‘Hey, there's a leak there, stop that leak.’ It's a half a percent gain, but wow, over time, that's significant.”
While companies have to balance business goals with sustainability efforts, internally weighing priority projects, ROI is not the determining factor for whether to pursue a project or a change to hit sustainable development targets, Smith says.
Kraft Heinz wants to provide food to the growing population and make money as efficiently as it can with the least impact possible on the environment, he says. “It's good for our company, it's good for our shareholders and everything, and it's also good for the world because now we can do more of that. We can have a bigger impact … More people get food.”
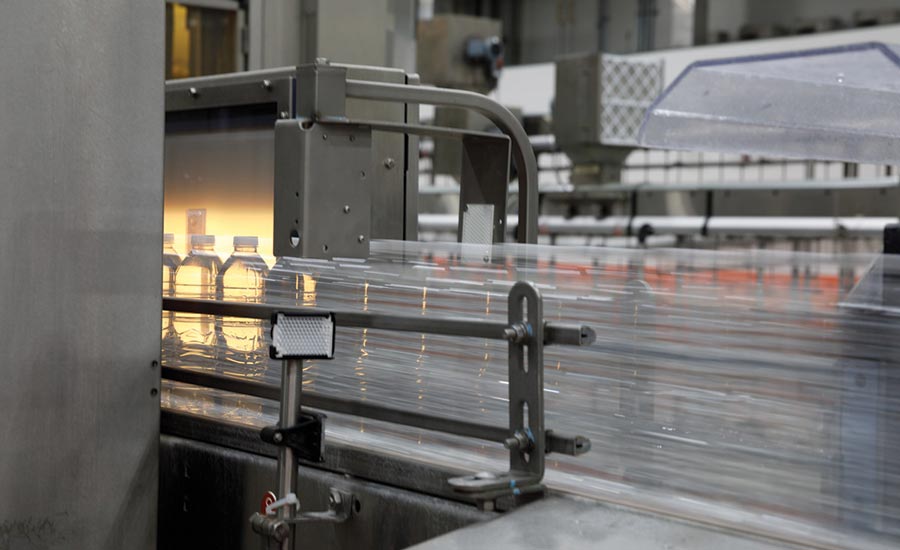
When you’re in the water business like Nestlé, keeping the resource renewable is critical
Dependent on natural springs for its bottled water, Nestlé Waters North America needed outsiders to weigh in on whether the company is doing enough to protect the water supply and use the resource responsibly.
The business started putting its water practices to the test a couple years ago, with a goal to certify all U.S. plants by 2025 under the first comprehensive global standard to measure responsible water stewardship. Changes to save water in factories are just a small part of the requirements to meet the Alliance for Water Stewardship Standard.
Nestlé Waters North America likes that multiple stakeholders review its efforts to use water responsibility from not only an environmental perspective, but also across social, cultural and economic criteria, Chief Sustainability Officer David Tulauskas says.
“This is an investment in our future. We make decisions not for the end of the quarter but for the end of the century. We rely on these springs, and we need to manage them responsibly so that they are a renewable resource.”
The certification efforts are paying off: A bottling plant in Ontario, Calif., recently became the first food and beverage factory in the world to earn the highest certification under the rigorous standard. To achieve platinum status, the plant documented measurable impacts from its work with leaders in the area to protect the watershed, with projects ranging from forest restoration to efforts in an area getting more attention called WASH, which stands for safe water, adequate sanitation and hygiene education.
For example, plant engineers coordinated with a local water district to share information and best practices to help with groundwater mitigation, which generated 250 million more gallons annually that had been decontaminated.
In North America, the company is the only one of any type to reach the advanced certification. The achievement has raised the bar for the company and its other factories, Tulauskas says.
“We want to earn a license to grow. We want to continue to be the largest, the best, the most important, the most respected bottled water company in the U.S. These are investments to keep us in that leadership position.”
Learn More: Technology to Aid Your Sustainability Efforts
After your plant has trimmed water usage where it can, the facility will want to handle its wastewater as efficiently as possible.
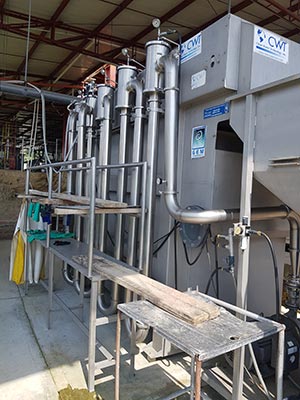
The Gas Energy Mixing System, or GEM, from Clean Water Technology Inc. replaces traditional dissolved air flotation treatment. The company cites these sustainable advantages of GEM versus a DAF system:
- Delivers significantly higher removal rates while using less chemical dosing.
- Flexible and adaptable in terms of loading and flow. When a processors’ waste stream changes, the GEM System can adjust to higher flow rates and increased loadings.
- The process management capabilities and unique hydro-cyclone action combine to maximize efficiency and effectiveness.
- Occupies much smaller space. The GEM System provides the greatest capacity per cubic foot of space occupied versus conventional DAF technologies.
- Generates drier sludge resulting in fewer loads to transport, which not only saves money, but also reduces fuel emissions and road wear/maintenance.
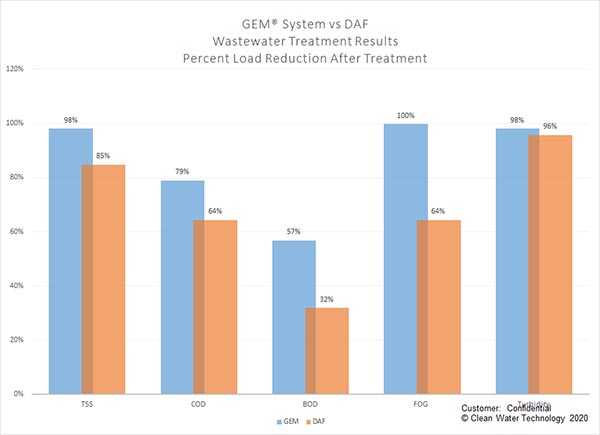
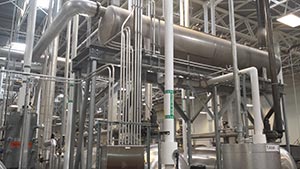
Instead of allowing retorts to vent steam outside, Allpax uses a recovery system to convert that energy into hot water.
The retort steam recovery system can reduce water usage in the retort room by up to 50%, the company, a ProMach brand, estimates.
Food Engineering has previously featured the recovery system that Allpax installed at a Hormel Foods facility in Iowa, where canned, shelf-stable meat products are sterilized in their containers with a saturated steam retort process. At that plant and others, the Allpax system uses the steam to create 180°F water, used in plant operations.
For more information:
Alliance for Water Stewardship, www.a4ws.org
CEO Water Mandate, www.ceowatermandate.org
Kraft Heinz, www.kraftheinzcompany.com
Nestlé Waters North America, www.nestle-watersna.com
Looking for a reprint of this article?
From high-res PDFs to custom plaques, order your copy today!