Field Reports
Robots aid Expansion of New Zealand Apple Company
Rockit Global uses MHM Automation’s tube-filling machines in its state-of-the-art apple packhouse

MHM Automation’s H&C apple tube-filling machines from automate the task of picking and packing apples at Rockit Global. Photo Courtesy of MHM Automation
The introduction of robotic technology is one of the driving forces behind a New Zealand apple exporter’s expansion. Rockit Global, which exports snack-sized apples packed into tubes for on-the-go consumption to more than 30 countries, unveiled its new state-of-the-art apple packhouse in Hastings earlier this year.
The company installed four H&C apple tube-filling machines, which each contain three robots, to automate the picking and packing of apples into Rockit’s tube packaging. The robots were custom -designed by global food processing technology company, MHM Automation.
Described by Rockit Global’s CEO Mark O’Donnell as the biggest innovation in the new packhouse, the robots are equipped with specially designed tooling to receive the tube and then place the apples into it.
“While packing apples into tubes sounds simple, in reality it is incredible technology.”
— Mark O'Donnell, CEO, Rockit Global
An integrated vision system identifies the height of each apple to allow the robots to select the correct sized apples to perfectly fill each tube.
“While packing apples into tubes sounds simple, in reality it is incredible technology,” says O’Donnell. “The robots are reading the size and shape of each apple as it goes past and working out which apples to put into their tube to maximize the fill of that tube; it’s really clever stuff.”
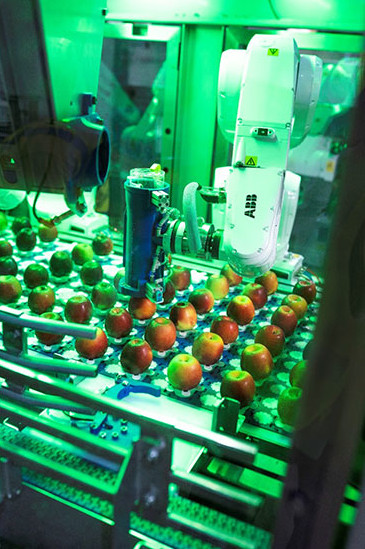
With sales of their apples continuing to grow significantly annually, Rockit Global recognized automation as the key to enabling the company to scale up its packing operations to keep up with customer demand.
The company engaged MHM Automation as a strategic partner in the design of its new packhouse.
“MHM Automation was a natural choice as they are a global leader in their field. As an added advantage, they also happen to be just down the road from us,” O’Donnell says.
Tasked with automating the labor-intensive task of picking and packing the apples, the MHM Automation team rose to the challenge of developing a system specifically to meet Rockit’s needs.
“Our product development process included design, prototyping, testing and proving, and then fine-tuning the design, before producing the final machines now installed at Rockit Global,” says MHM Automation’s CEO, Richard Rookes.
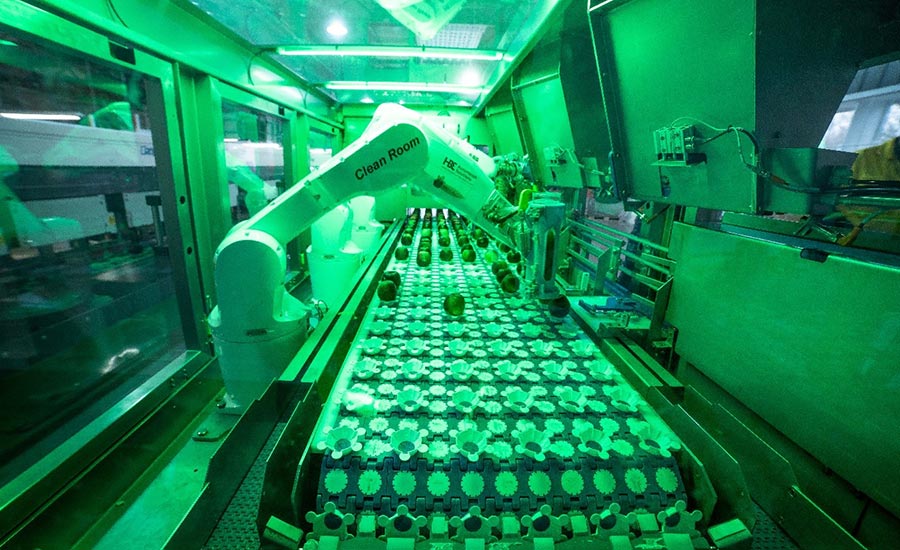
“Working on a unique challenge like this, where we are automating a task that has never been automated before, is what gets us really excited. The apple tube-filling machines are one-of-a-kind and as such, are world-leading technology,” he said.
Installation of the apple tube-filling machines has enabled a threefold increase in Rockit Global’s packing throughput, to 20 tubes and 100 apples per minute. MHM Automation continues to work with Rockit Global on further lifting its capacity through automation, with the focus now turning to automating the orientation and placement of apples onto the infeed conveyor, prior to filling the tubes.
Rockit Global expects throughput in the first year of the new plant’s operations to total 100 million apples, with a goal to increase that to 400 million apples in future seasons as additional automation is introduced.
Online only: For more information, visit www.mhmautomation.com
Looking for a reprint of this article?
From high-res PDFs to custom plaques, order your copy today!