AI helps control greenhouse automation systems
A greenhouse automation system can’t afford to make mistakes, because losing control of a single crop is costly

Photo courtesy of Bowery Farming.
Indoor farming has seen a substantial increase the past few years, and the category continues to grow. Vertical farms can be controlled to maximize production year round, while using precise amounts of finite resources, like water, preventing waste in the process.
To realize an effective ROI for the cost of a vertical farm and its equipment, all the inputs—water, chemicals, lighting, temperature, humidity and more—need to be tightly controlled. While the process variables for growing produce indoors may seem simple, there are elements that must work together to be successful.
To get a thorough understanding of such a complex, slow-moving system with interdependent variables, applying artificial intelligence (AI) and combining it with machine learning (ML) makes sense. Kenneth Tran, PhD, founder and CEO of Koidra, a system integration company specializing in applying AI to practical operations such as greenhouses and manufacturing automation, is well versed in AI. Before Koidra, Tran was a principal applied scientist in the Machine Learning Group, Microsoft Research (MSR).
Recently, indoor grower Soli Organic has been partnering with Koidra to develop the systems for its controlled environment agriculture (CEA) facilities. We asked Tran where he thinks this technology is headed in the future.
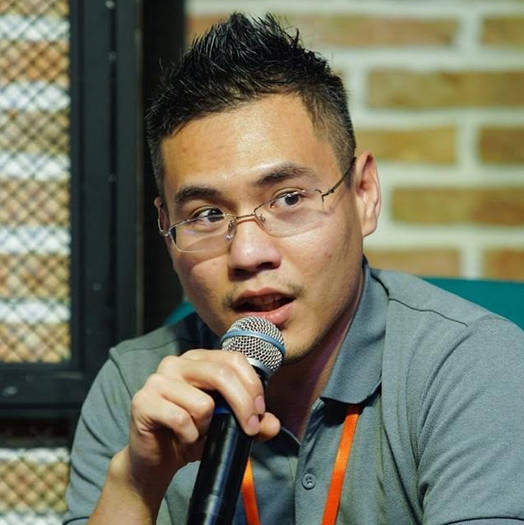
“Two major problems with CEA facilities are data silos and a lack of compatibility with common data interchange protocols.“
— Kenneth Tran, founder & CEO, Koidra
FE: Why is it important for Koidra to work with companies like Soli Organic?
Tran: CEA offers fertile ground for control innovations because of its life-science factor and complex processes intertwining physics and biology. This combination is a reason why we don’t often see the presence of mainstream automation companies in this market. However, if we can conquer the CEA market, we can conquer many conventional manufacturing domains.
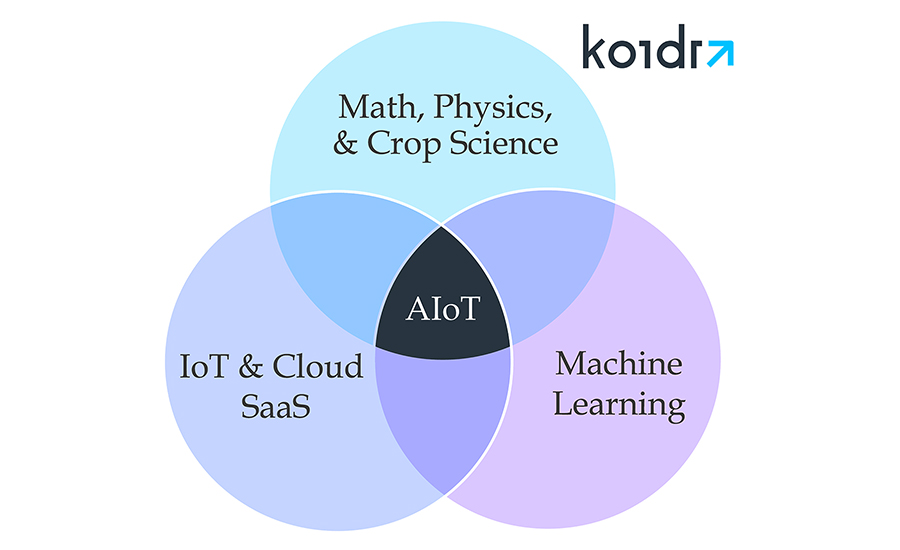
FE: What are you controlling in a CEA facility?
Tran: Everything that can be controlled with electrical signals, including: lighting, HVAC, CO2, irrigation, and recently plant density control—physically moving the plant locations in relation to each other. We’re participating in the 2022 Autonomous Greenhouse Challenge, and in this edition, we get to control the mobile gutters as well.
We also control other non-CEA applications, such as boilers, pressers, wood debarkers, and more. So, anything that has sensors, motors and actuators is within our domain.
FE: What are the challenges in developing controls for an indoor growing facility?
Tran: Two major problems with CEA facilities are data silos and a lack of compatibility with common data interchange protocols, such as APIs or OPC UA. While CEA is large, it hasn’t been large enough for companies to be pressured to support interoperability. However, the pressure is growing and this is changing quickly. Mainstream PLC/SCADA companies nowadays all support OPC UA as a protocol.
However, Koidra has turned that challenge into an opportunity. That motivated us to develop an innovative feature in our IoT Suite platform that can integrate with most existing systems. Hence, we can help customers unify data from multiple data silos.
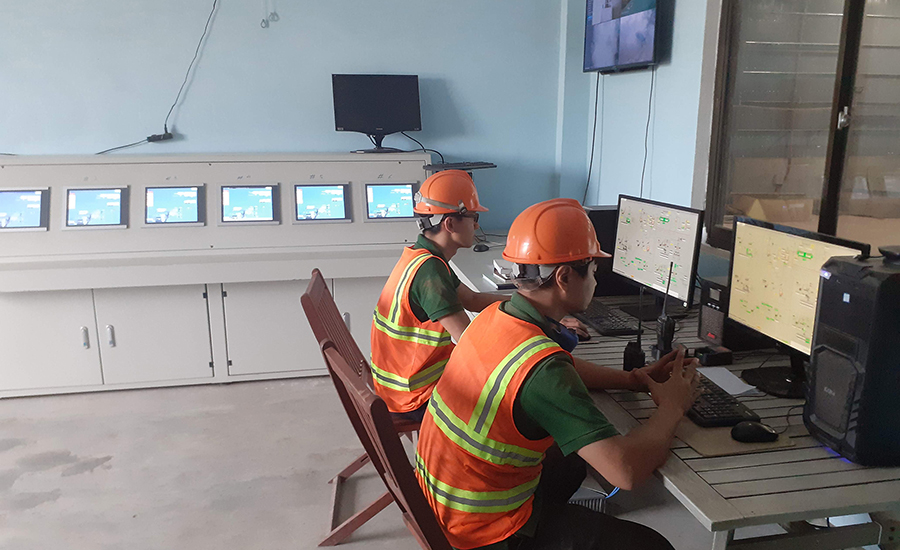
FE: Indoor facilities can occupy a large area. How do you place sensors and controls over such an area?
Tran: Indoor farms are somewhat homogeneous, compared to other conventional farms. It’s common that a multi-acre greenhouse grows just one crop and has the same climate settings.
That being said, the number of sensors and controls doesn’t necessarily correlate with the size of the farm. The sensor and control density is more dependent on business use cases—like growing multi-crops or mono-crops—existing infrastructure to support granular controls like compartments with walls and climate uniformity as a result of farm design.
FE: Did you develop specialized hardware or could you use off-the-shelf equipment for a CEA application?
Tran: We don’t develop specialized hardware yet. Our philosophy is working with the best-in-class commercial off-the-shelf (COTS) equipment.
FE: Was there any COTS software already suited to this CEA application?
Tran: Not at all. Autonomous growing is a new concept and still an active challenging research area. It requires an interdisciplinary approach that combines hard sciences such as physics, crop science, and machine learning with new technologies such as Industrial IoT (IIoT).
Even for the seemingly simple and non-AI problem such as integrating data from multiple data silos, there was no COTS software yet. So, we had to do it.
Looking for a reprint of this article?
From high-res PDFs to custom plaques, order your copy today!