What Sensor Companies Are Moving to and Why You Should Care
The importance of a digital sensor network is paramount to a digital transformation.

Over the years, sensors/actuators and their wiring have moved from purely analog (typically 4-20 mA or dc volts) to combined analog/digital (e.g., HART) and finally to 100% digital networks. During these years, plant engineers have seen more than their share of incompatible and proprietary networks, whether at the simple hardware, networking or application layer.
Recognized as an international standard, IEC 61131-9, IO-Link is a standardized, bidirectional communications protocol supported by sensors or actuators—which are connected through a master—which then connects to a controller, e.g., PLC, DCS, IPC or other. This networking solution provides users with more information about their devices, and it allows them to have remote access to the IO-Link master through industrial Ethernet networks, such as PROFINET or EtherNet/IP.
IO-Link is not another fieldbus. It was instead developed to reduce dependability on fieldbus support by manufacturers and users. It’s designed to be simple and universal, requiring only standard M12/M8/M5 cables/connectors, and it uses an open protocol.
Why IO-Link? Imagine you have a color sensor checking fruit color and it fails totally, stopping your sorting machine and the line. With IO-Link, the machine reports the broken color sensor. Since all the parameters of the sensor are stored on the machine and in the sensor, the maintenance department simply changes the sensor, and the machine then automatically re-parameterizes the new sensor, tests it and picks up operation where it left off.
Sensor and actuator companies have been signing onto IO-Link, and it’s been happening over the last couple of years in earnest. Keep in mind, making the switch to new wiring and networking protocols can be a costly undertaking, so it’s a serious step for both users and suppliers. Endress+Hauser recently adopted IO-Link, and I talked to Oliver Hansert and Karl Buettner, who are part of the team that is responsible for adopting and designing IO-Link into Endress+Hauser field devices.
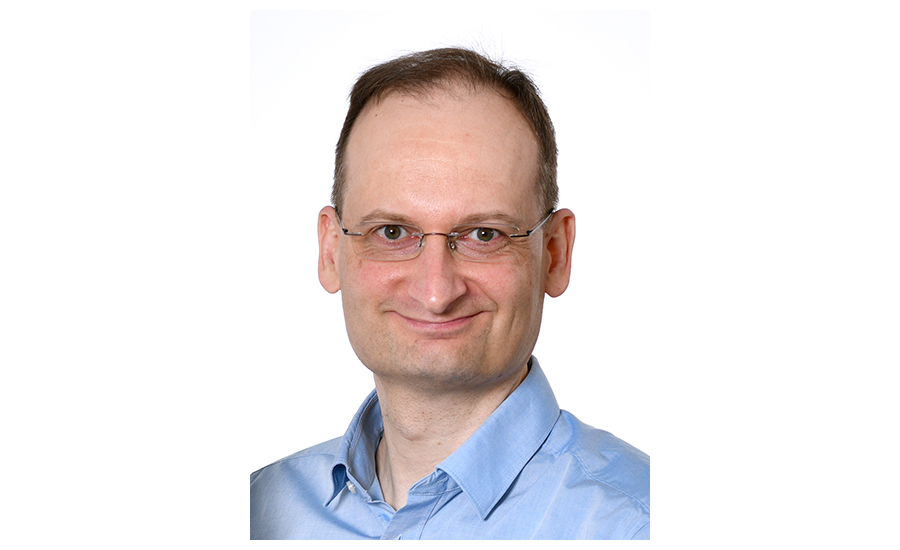
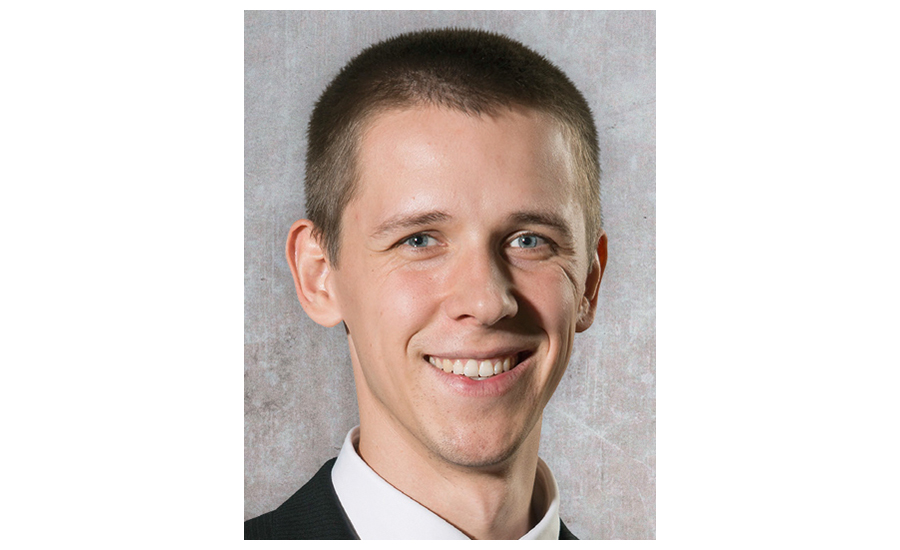
FE: Let’s start with the obvious first. What types of E+H sensors are now available with IO-Link functionality? How long has your team been working to make IO-Link sensors available?
Hansert: Today, we cover the most important areas of process automation within the food and beverage industry. This means, you will encounter various temperature, level, pressure, flow and analytical IO-Link sensors produced by Endress+Hauser.
Concerning development times, we have very thorough and lean processes. However, our main consideration before working on a new IO-Link device is an in-depth analysis regarding market needs and target applications.
FE: What was involved in migrating E+H sensors/transmitters to IO-Link?
Hansert: There are multiple aspects which need to be mentioned here. In each case, the instrument must be a good fit for the digitalization interface. We believe that IO-Link is a suitable connectivity option for some of our basic measurement instruments. IO-Link has been designed for rather simple sensors, which we know from a multitude of applications, for example within the field of food and beverage facility automation. Endress+Hauser gives customers freedom of choice when it comes to digital communication.
Buettner: For devices requiring more advanced communication capability, many end users prefer industrial Ethernet, such as with EtherNet/IP. But for other devices, we offer more basic protocols, such as IO-Link. We put a lot of effort to provide uniform usability, for example looking at the IO-Link data and services available with various instruments. This is important because, per the IO-Link specification, many features are actually optional.
FE: The network architecture involves a master connected between the sensors and a controller. Is the master simply a hub, or more? Can any supplier’s master work with any manufacturer’s sensors?
Hansert: The master is actually the brain within any IO-Link communication system. An IO-Link device is just a slave instance of such an IO-Link master. As long as all IO-Link participants are implemented according to the official IO-Link specification documents, which are issued by the IO-Link community, any manufacturer’s master will work with any other manufacturer’s device. As IO-Link itself is a standardized technology, cross-manufacturer interchangeability is a widely appreciated advantage.
Buettner: The IO-Link master translates data from its attached IO-Link devices to an upper-layer controller (PLC), typically via EtherNet/IP or PROFINET, using concepts similar to remote I/O systems. This is seen as an advantage for machine builders and end users because field connectivity stays within the IO-Link system, and depending on the machine or region, the provider can then connect the IO-Link master to upper-level systems using a wide variety of protocols.
FE: What are the key benefits that an IO-Link enabled device provides in terms of remote accessibility, auto-device replacement and diagnostic capabilities? Didn’t these exist in earlier digital sensor networks?
Buettner: That claim is true. Most of the benefits can be condensed down to a comparison of analog (0-10 V, 4-20 mA, PNP/NPN, etc.) versus digital (IO-Link, HART, PROFINET, Modbus, etc.). The general benefits of digital communication are the supply from field devices of the full resolution of measured values, multiple values from one device, and diagnostic capabilities beyond “not connected,” “short circuit” or “current limit violation.”
When comparing different digital communication protocols on a higher level with respect to diagnostics and other functionality, we do not see a significant difference as each will provide device status information (Good, Fail, Function Check, Out of Specification or Maintenance Required), as well as error codes, causes and remedy information.
Hansert: Many IO-Link masters offer a web server that can provide information about attached IO-Link devices via remote access from any platform capable of hosting a web browser, such as a cell phone, laptop and/or tablet.
Compared to field devices with direct Ethernet connectivity, IO-Link devices are not directly accessible from upper-level systems, such as asset management systems, as users must tunnel through the IO-Link master. Nonetheless, this is a lot faster in comparison to tunneling via HART due to higher communication speeds.
The simplicity of automatic device exchange via IO-Link is significant and very helpful for IO-Link users. For instance, an end user can exchange an IO-Link device without any knowledge of control system integration, as these devices are truly plug and play.
FE: What is the approximate installed base of IO-Link devices?
Hansert: The official IO-Link node count in 2021 was approximately 27 million IO-Link nodes worldwide. I assume this high deployment rate, along with strong growth, is seen as an important advantage by all IO-Link community members.
Buettner: When using IO-Link, end users can be assured that they are investing in a mature and growing technology, with tens of millions of devices deployed worldwide.
FE: If a manufacturer has an existing Foundation Fieldbus (FF) sensor network or HART network, what is involved in making the move to IO-Link? For example, wiring changes, design changes, reconfiguring I/O, drivers, application software?
Hansert: In brownfield plants, the communication technology is typically not changed as this would require replacing the field devices and masters, along with all wiring between these two items in some cases. Replacement might also be necessary for wiring from masters to higher level systems, depending on the protocol. This type of change might be done when a bigger revamp or plant extension is required for other reasons.
New communication technologies are more likely to be introduced in greenfield plants and for new machine designs.
Buettner: For planning and engineering of IO-Link systems the IO-Link community offers guidelines and a system description. Endress+Hauser also offers trainings and supports customers with their IO-Link projects. Looking at the topology, IO-Link is actually quite similar to 4-20 mA cabling (star topology), but the 20 m spur cable length limit and non-compliance of IO-Link with hazardous areas must be dealt with.
FE: When making the switch to IO-Link, can the actual sensing elements remain in place (i.e., just change the electronics)?
Hansert: Generally, IO-Link devices are small and highly integrated, thus they are in most cases exchanged completely. This is especially valid for most insertion devices, which are easy to replace. For our flagship devices we offer transmitter conversions of the I/O in some cases, but these devices typically communicate via industrial Ethernet.
FE: What are the cost/benefits in making the switch from HART to IO-Link?
Buettner: If the cable length is suitable and there are no requirements for hazardous area protection, IO-Link can be the better option. I think that in most cases the change happens from analog technologies, like pulse or 4-20 mA (without HART) to IO-Link.
Changing from analog to digital using IO-Link provides a number of CapEx benefits for machine builders, including faster engineering, commissioning and startup.
OpEx benefits for end users include fast device exchange, higher accuracy, multiple measured values per device and greatly improved diagnostics. Often end users use this type of information to get better insights into their processes and seize optimization potential.
FE: Are masters also available with a wireless option? What kind?
Büttner: We do not manufacture IO-Link masters. We test various IO-Link masters using our digital communication certification process and our Open Integration program, and we give recommendations to our customers.
As far as I know, for IO-Link wireless there is a specification, and first devices are available on the market. Endress+Hauser monitors this niche, and in the future there could be scenarios where this technology fits.
Looking for a reprint of this article?
From high-res PDFs to custom plaques, order your copy today!