Track and Trace
Tracking Distribution Through Data: Who Should See What?
Today’s tracking tools can produce a lot of data, but the challenge is to provide the right data to users and to regulatory bodies.

Make your own healthy salad, but do you know where all the ingredients came from? Chances are each ingredient has its own story to tell—but what if one of them is contaminated with a pathogen? FDA hopes to make each ingredient’s origin traceable quickly via modern technology. Image courtesy of Silvia from Pixabay
Most food safety management and ERP systems provide at least a one-step-forward, one-step-backward functionality when it comes to tracking and tracing products in the supply chain. The FDA and other government regulators would like to see more info available at any step along the supply chain. But does that mean that all participants need access to all the data? In this article, we look at the issues involved in tracking products through the supply chain and who should have access to the data.
Roadblocks to Data Access Along the Supply Chain
Tracking and tracing food products and ingredients through the supply chain has been a perennial problem—often due to many reasons, as Bryan Cohn, SafetyChain Software senior solutions engineer, points out. “Predominantly, it has been issues with older, siloed legacy systems and the lack of data normalization within company operations and the industry as a whole.”
The importance of a single database is a recurring theme. “Over the years we have talked about the requirement of ERP systems to integrate data from best-of-breed solutions, which is something that some ERP providers are better at than others,” says Maggie Slowik, IFS global industry director for manufacturing. She contends that an ERP system should combine multiple critical capabilities and maintain a continuous data thread (in a way a “digital product passport”) that tells the unique journey a specific product has undergone. This continuous data thread speeds up the retrieval of batch information, as required by FDA and/or other regulators.
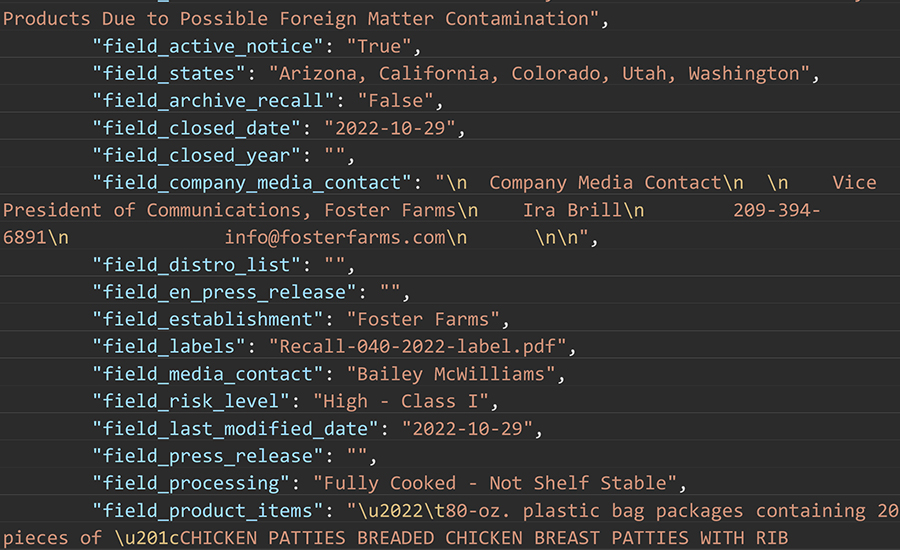
Getting everyone on board in the supply chain from farm to retailer has been a longstanding problem. “Adoption is still quite slow and primarily initiated by grocery retailers or relatively small-scale implementations aimed at paying a fair price to the growers, for instance, cacao and coffee,” says Marcel Koks, Infor industry & solution strategy director for food & beverage. “In many cases the value is not that obvious for upstream suppliers and farmers. Big drivers for adoption of multi-enterprise track and trace and transparency will be compliance with regulations such as FSMA 204 (establishes a foundation for end-to-end traceability in the U.S.) and the Digital Product Passport in the European Union.”
Francine L. Shaw, cofounder of My Trusted Source and author of a new food safety book entitled Who Watches the Kitchen, points out other roadblocks and hurdles preventing widespread supply chain tracking:
- Lack of standardized systems and processes across different countries and regions can make it difficult to track products. Different countries may have different regulations, reporting requirements and data formats, making it challenging to integrate data from different sources.
- Many food manufacturers do not have real-time visibility into their supply chain operations. This lack of visibility can also make it challenging to coordinate with suppliers and retailers in different regions.
- Data silos—different systems and databases make access and integration difficult.
- Communication and language barriers plus different time zones and cultural norms can lead to miscommunication, delays and errors, which can disrupt the smooth flow of the supply chain.
- Cost constraints are a challenge in implementing technology solutions, especially for smaller manufacturers and farms.
- Companies may be hesitant to share sensitive information about their supply chain with external partners due to data security concerns, cyberattacks and data privacy.
- Lack of collaboration and partnership: Food manufacturers may be hesitant to share information and collaborate with competitors or suppliers for fear of losing a competitive advantage.
The last two bullet points are certainly valid reasons for supply chain participants to think that “one-step backward, one-step forward” is good enough. “I believe that the one-step approach is actually the best foundation to build from,” says Steven Burton, founder & CEO of Icicle Technologies Inc. “It’s precise, achievable—and clear focus is very practical from both a technical and business perspective.”
“What we’re lacking most is a mechanism to capture only the portion of the traceability chain, only when we need it,” adds Burton. “This is the only means by which, in my opinion, we’ll ever be able to move across every step of a supply chain. Everyone in the supply chain should be required to maintain their supply chain information in a standard format and expose it using a standardized application programming interface (API) available to regulators—and only regulators—on demand.”
“But the regulatory bodies are different, the frameworks they use aren’t necessarily cohesive, and if you manufacture or sell products across any borders the whole process gets a lot more complicated,” says Burton. “The harmonization efforts from organizations like the Global Food Safety Initiative have been a really good start. Also, it will be very interesting to follow the roll-out of the new FSMA traceability rule to see how the requirements are implemented and which countries will follow the FDA’s approach.”
Burton’s company is currently developing an API connector to the FDA recall alerts system, called Recall Enterprise System (RES), which will pull that information directly into Icicle, which will allow the passing on of FDA alerts directly to Icicle food and beverage RRP users.
Farmers and Producers Start the Chain
A stumbling block to extending track and trace beyond one-backward and one-forward has been the extra cost to already strapped farmers and producers. What solutions/tools are available to help alleviate the cost and time constraints that producers now experience in entering data? In other words, how do we make their job of entering data easier and at low- or no-cost to them, especially when they are selling to multiple—but unrelated—customers?
“Cost isn’t the only obstacle,” says Burton. “Farmers in many locations, even in North America, don’t necessarily even have electricity or internet connectivity available consistently. That said, one really valuable tool to boost traceability systems and address the standardization problem is the GS1 Global Traceability Standard, which is an internationally recognized protocol for barcoding that is interoperable between different industries, companies, technologies, etc.
“The great thing about GS1 barcodes is that they are very affordable and practical to implement, as are the scanners and label printers necessary to use them,” adds Burton. “With them, you can create a seamless flow of information that can be passed onto your carriers, customers, etc., as well as pulled from your own suppliers if they use the GS1 system, too (regardless of what other technologies they employ). That data flow doesn’t have to be entered manually or involve complicated operations—just simple scanners that are already useful for inventory management and generally improve logistics workflows, eliminate human errors and boost efficiency. While these systems have been broadly adopted by multinational corporations over recent decades, small and mid-sized companies have been slower to adopt them,” says Burton.
In connecting distributors to farms and producers, the former may need to assume most of the burden in connecting to producers, says Shaw. “This could require special programming and coordination between the fresh produce distributor and other supply chain participants. In order to ensure accurate and efficient passing of grower information, the distributor may need to work with its IT team or a specialized integration vendor to create connections between their ERP or food safety management system and those of their supply chain partners. This could involve developing APIs or using middleware platforms that can translate data between different systems.”
In some cases, there may be standard data exchange protocols in place, such as EDI (Electronic Data Interchange) that can be used to facilitate the transfer of information between different systems, adds Shaw. However, if the data structures are significantly different, there may need to be custom mappings and transformations implemented to ensure that the data is properly formatted and understood by both parties. To avoid potential programming issues, the fresh produce distributor should proactively communicate with its supply chain partners and establish clear data sharing processes and protocols.
“The process must be approachable,” says SafetyChain’s Cohn. “This is where the power of integrations can play a significant role in helping get data to where it needs to go. If, for example, some of the key data elements already exist within another system but need to be communicated in some other way, an API integration can carry that data from one system to the other. Or if the data elements are produced on a case label or pallet label, simply scanning that label and pulling the information into your software is a great way to quickly pick up the data you need without disrupting the normal flow of operations.
“The bottom line is that you need to understand the employees’ and supplier’s specific movements—and how you will tap into the information they have without disrupting their routine or flow,” adds Cohn.
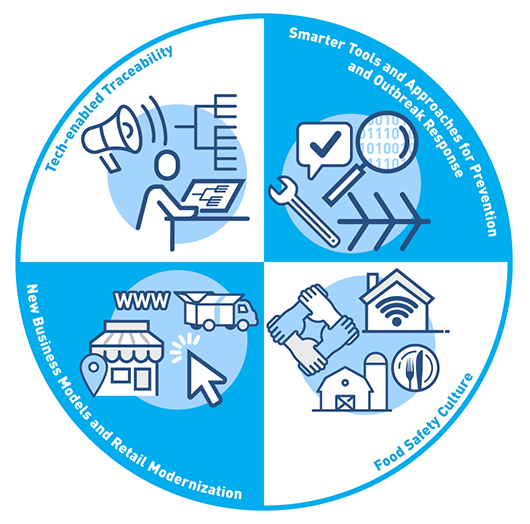
Sophisticated data/system integrations: This is another capability that is key for today’s modern ERP providers, but still to an extent, underestimated, says IFS’s Slowik. IFS Cloud comes with open Rest APIs allowing food and beverage manufacturers to easily integrate with other systems, for instance LIMS and/or systems that might allow them to trace “further” beyond the one step forward/backward in the supply chain.
While software interconnectivity can be achieved to its fullest, Icicle’s Burton suggests it still comes down to people. “The key to successful traceability is to ensure that your systems don’t silo traceability data [by those responsible for managing it] in one part of your company. Organizational change is 60% of any technology initiative; if workers aren’t in the habit of recording data, it’s really hard to change that culture. You need to sell the workforce on adopting new ways of doing things, and the best way to do that is to make their job easier. That’s what we do, we try to improve worker’s day-to-day lives.”
Compensating for Different Supply Chain Software Systems
If a fresh produce distributor is using one supply chain system (may be part of ERP or food safety system), and the grower something else, then how does the buyer of these fresh products pass along this grower information to the next distributor or food processor, especially when supply chain participants are not using the same ERP or food safety management system? Does this require special programming? Couldn’t a fresh produce distributor find itself with lots of programming issues as it seeks to sell to multiple customers?
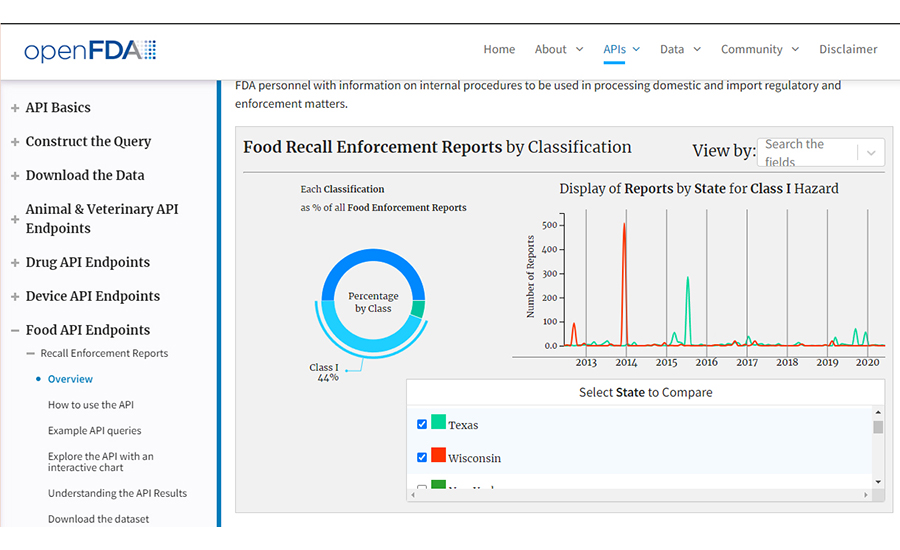
“The short answer to the first part of the question is that you shouldn’t even try,” says Burton. “The last thing that a distributor is ever going to do is share information on their suppliers with their customers, nor is it reasonable to expect that customer to maintain data that isn’t their direct concern. Mix into that problem the linguistic and technological diversities that abound in the global supply chain with the high costs of integrations, and you have the perfect recipe for failure.”
On the second question, Burton says the only viable solution is to require, at a regulatory level, everyone involved in the supply chain to expose a standardized API that can be called upon by the regulators to query a particular product when needed. This would allow them to piece together a single traceability chain upon demand, one step at a time. If there were an outbreak of foodborne illness that was traced to a salad, for example, the supplier of that salad could be queried for their one-step backward information. The produce suppliers disclosed in that query could then be queried in the same manner with the process continuing until the farms where the lettuce was grown are identified.
Note that this is essentially the same process that regulators use today, except they do it all manually, adds Burton. “Adding a standardized API infrastructure to automate the process would be highly effective, especially if augmented by AI. This is in contrast to requiring the last step in the supply chain to have all the traceability information for the entire supply chain immediately on hand at all times for all products, which is a crazy idea with no hope of success.”
“The FDA with the FSMA 204 regulation and GS1 with the Global Traceability Standard have defined a common data structure for the industry,” says Infor’s Koks. Blockchain would help the growers, distributors and food processors by sharing the information from their own distributed ledger with the distributed ledger of their customers, and from there via an interface with the customers’ ERP or track and trace platform. Parties in the food supply chain can get the information in their distributed ledger through an interface with their ERP, via file upload or mobile app, says Koks.
“The sending and receiving of logistics data between supply chain partners can always be tricky,” says SafetyChain’s Cohn. “There will always be different systems and methods between retail and supply chain partners, and there are multiple ways to account for that. But it only matters if you use a unified data structure such as the GS1-28 standard. If you are moving—or planning on moving—products at scale, the only way to exchange logistics effectively between partners is by using GS1-28.”
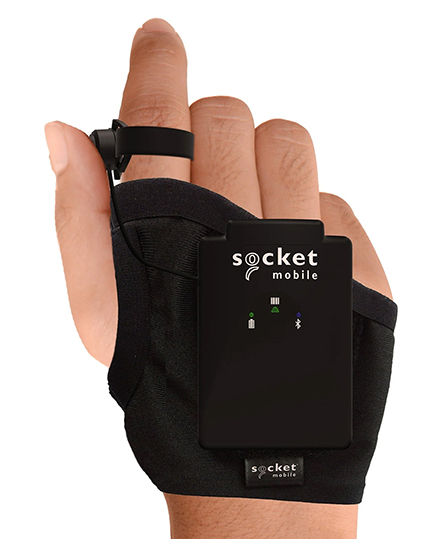
Building Blocks to the Future
While emerging technologies point to a much-improved tracking system for food products, collecting data for data’s sake and to provide for multi-step tracking within the supply chain may be counterproductive. However, My Trusted Source’s Shaw lists five emerging technologies that can help provide multi-step tracing capabilities: blockchain technology, internet of things, RFID technology, AI and mobile applications.
“Overall, the future of track and trace technologies is moving toward interconnected systems that can provide real-time and multi-step tracing capabilities,” says Shaw. “This will not only improve traceability, but also enhance food safety, reduce food waste and build consumer trust in the food supply chain.”
“I can’t wait to see how well this statement ages, but as I sit here and write this, I genuinely believe the future of track and trace technology does not belong to one company or method,” says SafetyChain’s Cohn. “Traceability comes down to good organization between all the software systems and best practices within your organization. We have to let go of siloed software systems and pen-and-paper processes. All of your systems need to work together, like a symphony, to provide the visibility you need up and down your supply chain and within the four walls of your manufacturing environment.”
“We believe that multi-enterprise track and trace will become more and more important not only for food safety reasons, but also to pass on accurate and trustworthy scope 3 greenhouse gas emissions,” says Infor’s Koks. “Over time the number of data elements will grow with additional sustainability information, such as water withdrawals, use of fertilizers and pesticides, etc. Because of this, automation of data exchange and an expandable data structure are key.”
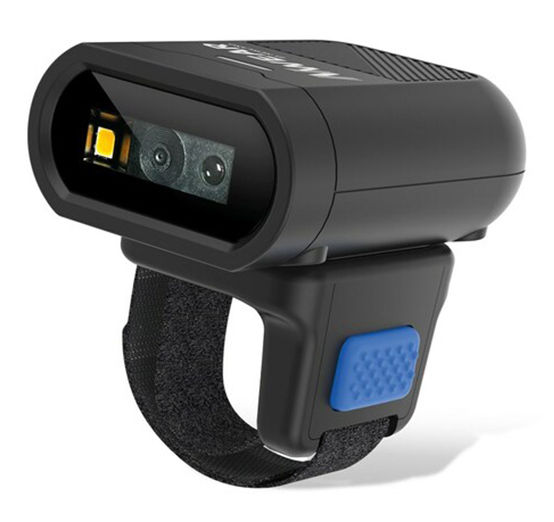
Serialization is another way to drive traceability (and authentication), says IFS’s Slowik. Serialization is the process of putting a unique number on a product and/or the selling/packaging unit, rather than batch level. IFS Cloud supports this, and the practice is already quite common in the pharma industry. Serialization allows manufacturers to incorporate information such as date and location of production, lot or batch number, product description and the manufacturers’ GTIN (Global Trade Identification Number).
But how much data is really needed? “I do think the one-step approach is a solid foundation for manufacturers, but from the perspective of public health and regulatory institutions,” says Icicle’s Burton. “I think the way to improve on our current system is not to create a massive repository of data but to take a more targeted approach. Data can be collected by manufacturers using whatever system they choose, as long as that system exposes an API that regulatory authorities can access to extract only the information they need and only when they need it. Since an API is a technical connector between different applications, you won’t need a centralized or uniform system for the concept to work. If there’s a recall, then the regulatory authority would use the API to send queries (data requests) to the different companies involved and get back the exact information they need for their investigation. With a model like that in place, one-step-forward, one-step-back is actually what is required from the average company in the supply chain.”
Resources:
“FDA Food Enforcement Review,” openFDA, https://open.fda.gov/apis/food/enforcement/
“FSIS Launches New Data Tool: Recall and Public Health Alert API,” FE, 20 OCT 2023
“Tech to Enable Track and Trace,” FE, 10 FEB 2023
Looking for a reprint of this article?
From high-res PDFs to custom plaques, order your copy today!