Tech to Enable Track and Trace
The FDA will require complete track and trace information within 24 hours.

Becoming law on January 20, 2026, the FDA final rule on “Requirements for Additional Traceability Records for Certain Foods” (Food Traceability Final Rule) establishes traceability recordkeeping requirements, beyond those in existing regulations, for persons who manufacture, process, pack or hold foods included on the Food Traceability List (FTL).
The FTL includes an array of foods that have been known to cause foodborne illnesses when not properly processed, cleaned, handled, inspected, tested and transported. Some of these foods include soft cheeses made from pasteurized milk, shell eggs, nut butters, fresh cucumbers, leafy greens and herbs, melons, peppers, fresh tomatoes, sprouts and more. Find the details on the FDA’s Traceability List.
FDA Deputy Commissioner Frank Yiannas gave a talk at the International Association for Food Protection 2022 annual meeting, where he said: “I’m asking you to imagine a future in which the global food system is so transparent and data-informed that we can immediately trace a food’s journey to its origin in seconds—not days. And we’ll know more than where it came from; we’ll know exactly how it was produced and handled at each step of the way—and will also know the impact that any disruptions related to that food will have on the food system and, ultimately, its safety and availability to consumers.”
Actually, the FDA reg asks for a response time of 24 hours, but with the right technology, there is no reason that seconds’ response time is not possible. For a processor/producer to be able to respond with traceability information within the seconds that Yiannas describes, technology can provide solutions. But a couple of challenges remain, for example having readily accessible data repositories for everyone in the supply chain, making the data available at no or low cost to supply chain participants, having standardized data communications both at the uppermost levels and at the network and sub-network levels, and keeping the data safe from hacking or intentional changes of dates or other relevant information.
Shortening the Supply Chain Can Help, but Isn’t Always Practical
While the recent COVID-19 pandemic taught us that long supply chains weren’t quite ready for prime time, it also showed that even shorter supply chains within a single state could be rendered ineffective when there is no transportation due to drivers being out. In Pennsylvania, for example, dairy farms within 100 miles of Philadelphia could not get their milk delivered to nearby dairies to process it—so they had to discard it at the farm. Thus, there were milk shortages in suburban and city groceries. Obviously, with longer supply chains, not only is food delayed when multiple legs of transit are needed, quality and food safety can be affected as well.
In a November 2020 FE interview with Kaiyuan Lin, then researcher with the University of Tokyo, Lin demonstrated a cost-effective track and trace method using QR codes and database technology for more localized supply chains where every participant had input to the technology. In a recent interview with Lin, who is now working with shorter supply chain solutions and QR/database systems, he suggested that in many parts of the Far East, this technology works where there are several farmers/producers, a logistics provider, and wholesalers and/or retailers. For example, he cited an application where pineapples are grown on farms in Taiwan and exported to Japanese markets. All those involved have participation in the supply chain track and trace system.
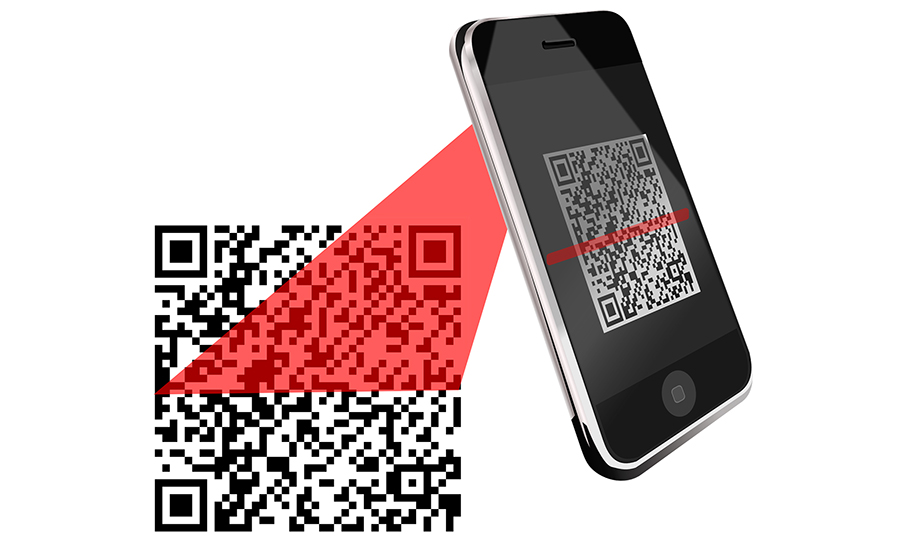
Extending Technology to Cover the Entire Supply Chain
Many small- to medium-sized enterprises still hesitate in adopting digital record keeping. “Despite fears of cybersecurity breaches, paper records actually bring higher risks than digital data,” says Eric Garr, regional sales manager at Fortress Technology Inc. (FTI), an inspection machine manufacturer. Not only can manually collated information be incorrectly recorded, forgotten or lost, results can also be deliberately falsified. If producers cannot prove when and where inspection of their products took place, food manufacturers may then be unable to demonstrate compliance and could be forced to re-inspect an entire batch. This not only slows down production, at worst it could trigger a product recall, says Garr.
With inspection equipment and other production hardware, suppliers generally provide software applications to record data with timestamps. This timestamped data can be accessed by the supplier’s software and exported into systems such as MES and ERP to keep digital records that are acceptable to FDA and other regulators whenever they demand it.
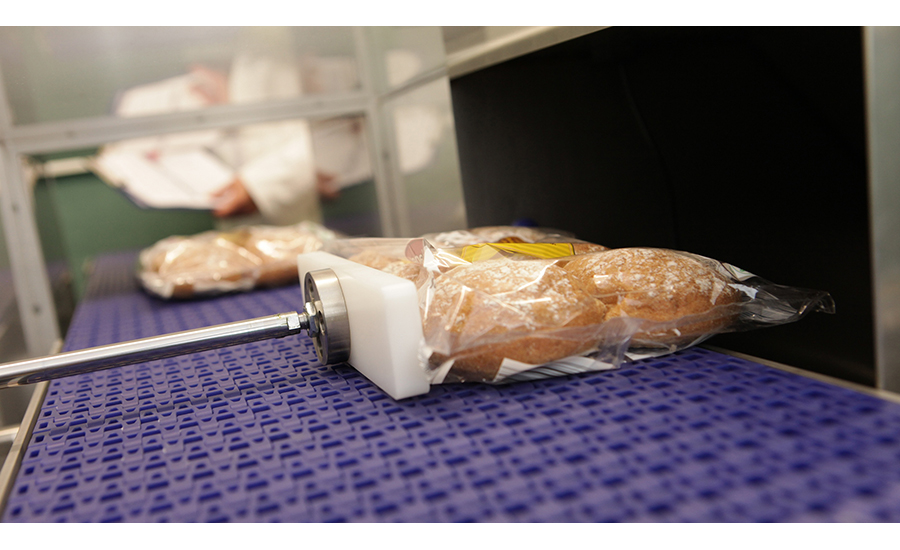
“While the final rule does require companies to provide an electronic sortable spreadsheet containing relevant traceability information to the U.S. FDA within 24 hours of a request, there are a number of technologies that are making track and trace more efficient and effective across the food industry,” says Angela Fernandez, vice president of community engagement at GS1 U.S. Some of the technologies that have been adopted include blockchain and radio frequency identification (RFID).
Blockchain enables an immutable and transparent ledger of information about the production, handling and distribution of food products through the supply chain, says Fernandez. And RFID technology can provide real-time visibility into the movement of food products through the supply chain, enabling expedited traceability to the source of foodborne illnesses and contaminants. RFID tags can be equipped with temperature sensors that can monitor the temperature of food products as they are transported and stored. This can help to ensure food products are kept at the appropriate temperature to prevent spoilage and other potential issues.
“The use and deployment of newer technologies may help food companies quickly and accurately track and trace their products in an automated way, which may help to ensure food safety, improve product quality and reduce waste and inefficiencies in the supply chain in real time,” says Fernandez. GS1 U.S. has been working with industry to address these opportunities through the adoption and use of GS1 Standards, the most widely used supply chain standards in the world.
What are GS1 standards?
- GS1 Standards are a solid foundation for building or refining the food safety traceability systems of food businesses. GS1 Standards facilitate the identification, capture and sharing of information between trading partners. They include:
- Product identification via the Global Trade Item Number (GTIN), which can identify foods at harvest, processing or movement and help prevent confusion caused by internal numbering schemes.
- Location identification via the Global Location Number (GLN) identifying locations such as a farm or field, a packing house, manufacturing plant, a distribution center, a supermarket or a restaurant. They help a company unambiguously map each stop a product makes along the supply chain.
- Automated data capture for traceability with GS1-128 barcodes applied to product cases. Trading partners are able to encode data such as expiration dates, batch/lot/serial numbers, quantities, weights and other information into these barcodes, ensuring the identity and core data about products is connected both digitally and physically.
- Physical event data sharing via EPCIS (Electronic Product Code Information Services) to translate transaction and transformation events into a common language to tell a complete history of a product from stop to stop along the supply chain.
GS1 Standards bring structure to the data being collected and make interoperability between systems possible, so the data is meaningful to all trading partners. Once companies can recognize the benefit of leveraging GS1 Standards, there’s potential to improve efficiency, enhance food quality and safety, increase transparency, enhance competitiveness, improve risk management, and ultimately help prevent disruptions along the supply chain.
A stumbling block to extending track and trace beyond one-backward and one-forward has been the extra cost to already strapped farmers and producers. “Track and trace should start at a product’s source of origin,” says Jim Bresler, Plex director of product management, food & beverage. Thankfully for farmers and food producers with low budgets for technology investments, their upstream supply chain partners can help support end-to-end track and trace adoption. Food manufacturers that are trying to enable end-to-end tracking can take advantage of solution integrations like those offered by Kezzler for external track and trace capabilities across the supply chain, adds Bresler.
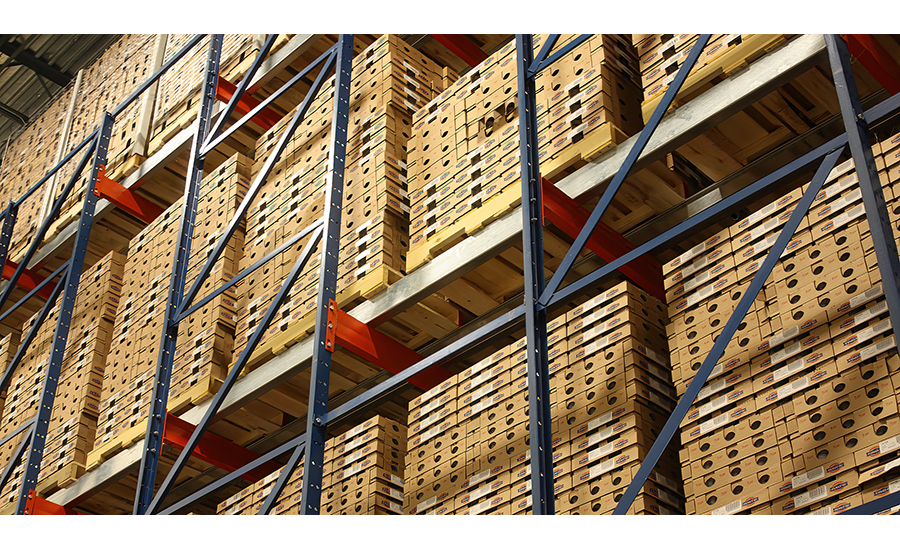
Kezzler was selected by FrieslandCampina to provide global traceability services for its top infant formula brands. Infant nutrition brand FRISO launched FRISO TrackEasy, a smart packaging innovation that enables parents to experience the journey of FRISO’s formula milk at their fingertips, starting from the company’s Holland-owned farms. FrieslandCampina integrated Kezzler’s traceability platform within its existing IT infrastructure, providing serialization and unit-level traceability, meeting government requirements and giving consumers the ability to trace back the complete ancestry of infant formula products.
The combination of increasingly digital, connected supply chains and the addition of user-friendly, intuitive, mobile applications and software access can greatly improve the ability of end users and companies to track across the entire supply chain, adds Bresler. What tools and systems are used at the end point is dependent on the type of end user, and what information they can access is dependent on how well the supply chain upstream is connected digitally. However, Bresler observes, recent supply chain shocks and disruptions will drive companies and industries to invest more heavily in better connected, digital supply chain solutions that benefit everyone from the industrial user to the farmer.
Standard Data Communications
Fortunately for food producers and processors, moving data from equipment to equipment and to MES, ERP and track and trace systems is becoming transparent and no longer an issue.
At the equipment side of things, by utilizing automated data integration protocols like OPC/UA and Ethernet/IP, standard communications can be implemented more easily, says FTI’s Garr. These standard methods of industrial communication also provide a robust, simpler and safer way to rapidly stream data within the firewall of a business network. Data tags defined by each food plant are converted in real time to an internal business database, providing valuable oversight to support flexible production.
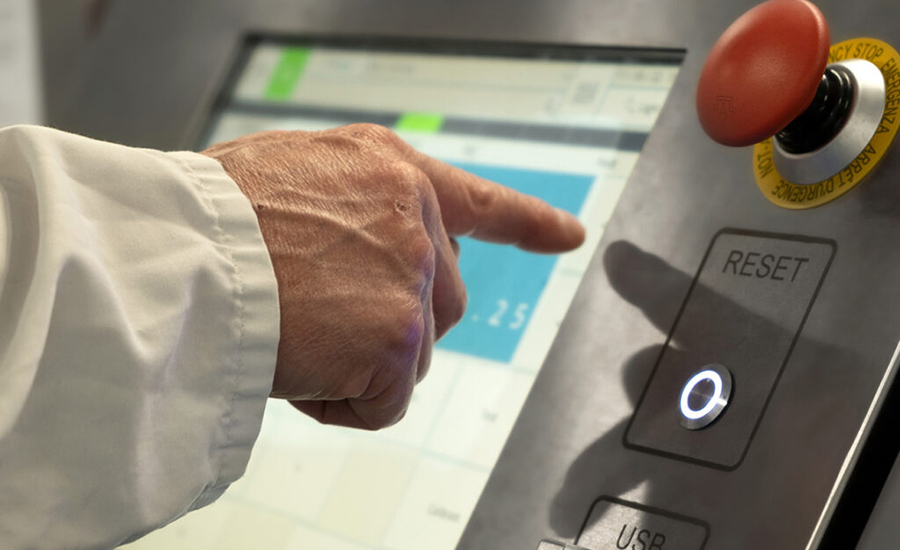
“We are entering a new Internet of Things (IoT) era where everything that can be connected will be connected,” says Garr. Knitting together the extraction of data and bridging the gap between machines and humans helps predict—rather than react to all types of—production scenarios.
At the tracking side, barcodes provide a means of tracking pertinent data. “Companies that offer advanced traceability in their software use barcoding as a standard and invaluable tool for digitally tracking material—both work-in-process (WIP) as well as upstream and downstream of production—so that there is a digital thread of information about that material,” says Bresler. “When finding a tracking and barcoding solution, ensure that the vendors and tools you evaluate meet your specific needs, enabling you to quickly gather the information required for audits and for tracing material to and from suppliers and material origins.”
“The barcode—leveraging GS1 Standards to uniquely identify products, assets, locations and more—improves end-to-end traceability in the supply chain,” says Fernandez. “Why? The standards are technologically agnostic and can be used with a variety of different solutions and systems. The barcode itself is a simple, visual representation of data that can be easily scanned and read using a barcode reader.”
Future Trends
As more and more of the equipment in food plants becomes connected, increasing volumes of data will afford operators and suppliers ever greater control, improving efficiency, ensuring food safety and providing full traceability, says FTI’s Garr. “The standout factor that makes data so valuable is how it is analyzed, spots trends and patterns—and as a result informs better business decisions.”
“Even before the final rule, traceability had already been a priority for industry to create a better, preventive food safety system and avoid costly food recalls—even dating back to the 2006 spinach recall,” says Fernandez. “There has been widespread industry collaboration within the Produce Traceability Initiative with the goal of utilizing GS1 Standards to enable better traceability processes as well as GS1 U.S. industry initiatives across grocery and foodservice.”
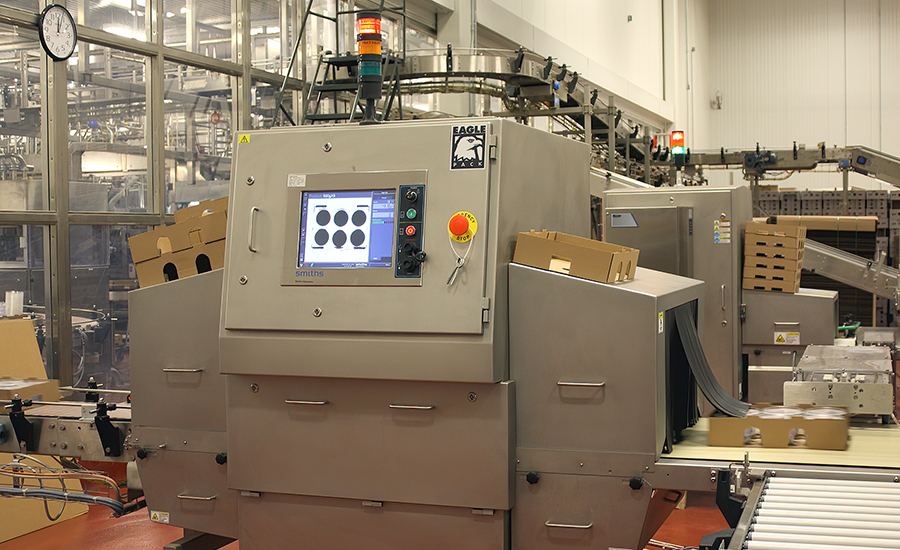
GS1 Standards provide a common language for business that is interoperable—meaning different technology solutions can speak to each other and, ultimately, enable trading partners to gain a shared view of products as they move through the supply chain. This supports scalable solutions for the industry given not everyone will be on the same platform or software system, says Fernandez.
“Based on the conversation at the recent North American Food Safety and Quality Summit in Chicago, it seems that the call to action—to unify in support of an optimized supply chain with backwards and forwards track and traceability—is gaining support,” says Plex’s Bresler. “The number one way to achieve this is through thoughtful digitization that connects across and beyond the organization.”
There’s also a non-food related issue that may be important in the digital data accumulated on a particular product as it moves through the supply chain, says Bresler. “This is going to be increasingly critical as companies commit to net-zero initiatives to reduce the impact of manufacturing operations on the environment. To meet goals for sustainability, manufacturers will need to report on Scope 3 emissions, which come from suppliers. Manufacturers will need to be able to track, document and evaluate Scope 3 emissions to validate net-zero compliance.”
“In addition, some processors/manufacturers can, as part of their enterprise software agreements, enable suppliers and customers to access information about their orders within that manufacturer’s supply chain at no cost,” says Bresler. “This makes those suppliers and customers active members of the process, enabling them to get real-time information about their products to help solidify delivery dates, potential bottlenecks, and allows for continuous improvements.” Plex is one vendor that enables its users to give their suppliers and customers access—at no additional cost—to their order information from anywhere in real time, says Bresler.
Resources:
“Remarks by FDA Deputy Commissioner Frank Yiannas at the International Association for Food Protection 2022 Annual Meeting, 1 August 2022,” FDA Website; accessed Jan. 2, 2022
“Blockchain is the tracking method preferred by industry right now,” FE, April 15, 2020.
“Creating a track-and-trace system for the rest of us,” FE, Nov. 13, 2020.
“Grass to Glass Traceability & Consumer Engagement,” FrieslandCampina case history available on Kezzler’s website, www.kezzler.com
Looking for a reprint of this article?
From high-res PDFs to custom plaques, order your copy today!