CASE STUDY
Flexible Packaging Flexes its Muscles with Recycling Pilot
A single-stream mechanical recycling pilot demonstration produces the rFlex bale, a flexible packaging byproduct that could be used for future end markets and as a possible feedstock.

Image courtesy of Getty Images Recycle Man
According to The Recycling Partnership, 8 in 10 Americans report recycling is worth the effort. However, over half of household recyclables end up in trash bins instead of recycling containers that create economic and environmental costs.
A recent 2023 report by the Materials Recovery for the Future (MRFF)—an industry consortium of food and beverage companies, non-profit organizations, industry suppliers and more—found that residential sorting processes can integrate flexible plastic packaging (FPP) into a single-stream, mechanical recycling facility. Besides the functional demonstration of integrating FPPs, the pilot provided capital toward investigating end markets for an FPP end product, called the rFlex bale—which can be used as a material component in bale form or made into a feedstock.
TotalRecycle Inc.’s J.P. Mascaro & Sons facility was ground zero for this pilot demonstration. MRFF provided a $2.6 million grant to install optical sorting equipment on four lines at the facility so flexible plastic packaging could be sorted in an automated fashion. TotalRecycle Inc. funded the rest of the capital expansion.
“That was about a $5 million upgrade,” says Joseph Mascaro Sr., director of recycling and sustainability at J.P. Mascaro and Sons, back in 2020. “MRFF helped subsidize the installation of the equipment, and we are performing their pilot demonstration to actually prove that post-consumer flexible packaging can be recovered in a single stream at a material recovery facility."
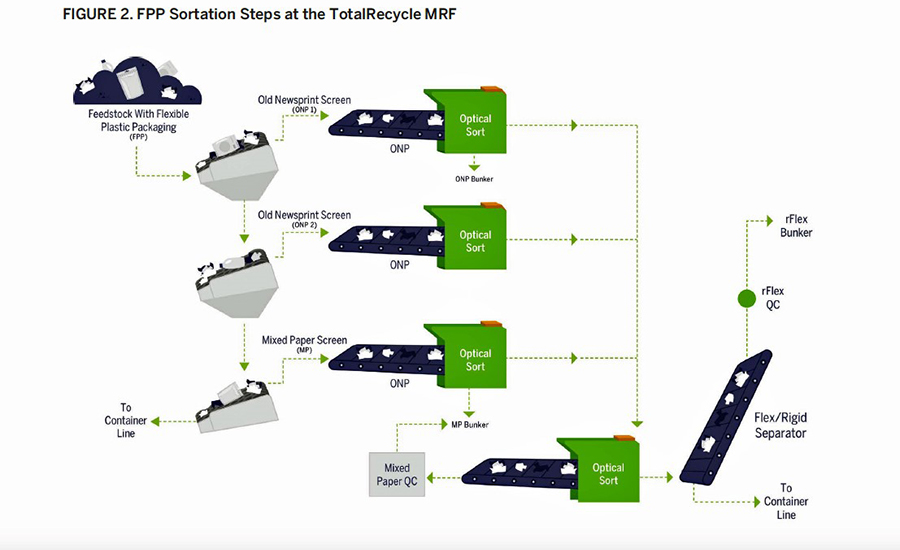
Fast forward to 2023 with the optical sorting lines in place for the demonstration, the pilot successfully recognized FPP material within the single-stream recycling process and the rFlex bales.
“Flexible packaging is the most sustainable packaging since it is source-reduced packaging, and this makes recycling FPP inherently less cost-effective,” says Claire Sand, CEO of Packaging Technology and Research, LLC. “When consumers do not have recycling systems for flexible packaging, they will continue to perceive flexible packaging as not sustainable since consumers connect recycling with sustainability.”
Consumer packaged goods (CPG) companies are demanding more PCR content to meet sustainability goals, which their customers want. “There simply isn’t enough recycled content today in the supply chain to reach our goals,” said Roberta Barbieri, VP of global sustainability at PepsiCo, back in 2020. “The only way to make more is to drive higher recycling rates.” To drive more recycling, the industry is pointing to extended producer responsibility programs to do just that.
"We are investing in innovative technologies and partnerships that are critical to helping us redesign packaging, eliminate unnecessary plastic, increase our use of recycled content, and influence the adoption of reuse models.”
— Rashida La Lande, Kraft Heinz
“Currently, there is no incentive for recyclers to invest in these technologies based on the current return on investment (ROI) as end-markets are still scarce, and the value of the rFlex bale will not pay for the upgrades,” says Alison Keane, president and CEO of the Flexible Packaging Association. “However, investment can and should come from the EPR programs being implemented in the four states that have passed laws.”
“Lack of sustainable funding is one of the greatest challenges for U.S. residential recycling systems,” says Keefe Harrison, CEO of The Recycling Partnership (TRP). “EPR provides a huge opportunity to unlock the environmental and economic benefits of recycling.”
An EPR study from TRP, a non-governmental organization, researched the impact of EPR programs in seven jurisdictions worldwide and in six U.S. states to assess the effect on state-level recycling rates and came to this conclusion:
ERP’s impact on seven paper and packaging recycling programs “showed that across the board, EPR policy drove the collection and recycling of target materials to over 75% in British Columbia, Belgium, Spain, South Korea and the Netherlands, with Portugal and Quebec at over 60%. Across all materials, U.S. state programs performed far lower.”
“Adding an economic incentive to collect and sort is paramount to success,” says Packaging Technology and Research’s Sand. “We see this success in ‘bottle bill states’ which have higher recycling rates and how this economic is at play in the now 25+ year-old European EPR as well.”
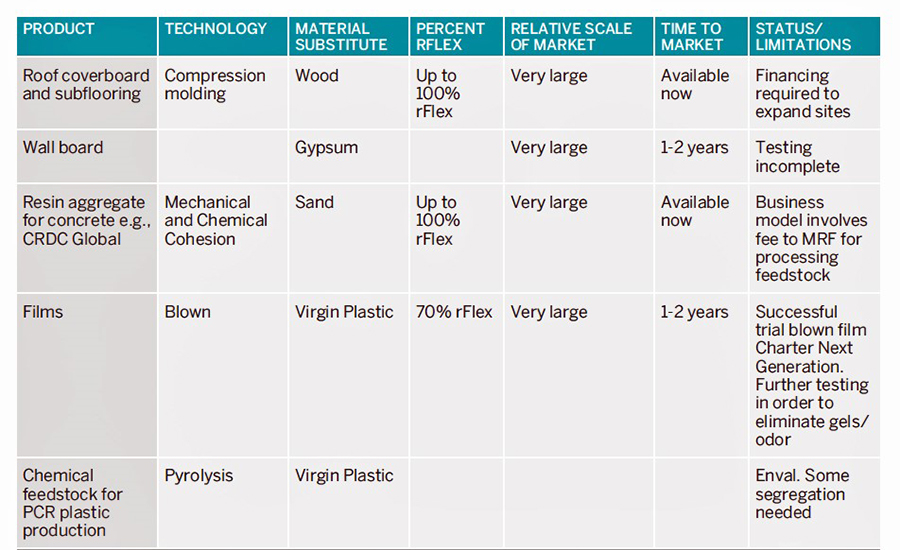
However, there’s been mixed messaging from CPG companies on mechanical recycling. The Coca-Cola Company recently announced a new venture capital fund “to spark sustainability innovations,” but older recycling technologies—i.e., mechanical recycling—are not part of the plan.
The new venture fund will include money for recycling but Coca-Cola says, “we are investing in startup companies with new, emerging technology or science in this space versus providing capital for existing recycling companies,” via Plastics Recycling Update media outlet.
Kraft Heinz said in July that the company will reduce its use of virgin plastic globally by 20% or more by 2030. “We are investing in innovative technologies and partnerships that are critical to helping us redesign packaging, eliminate unnecessary plastic, increase our use of recycled content, and influence the adoption of reuse models,” says Rashida La Lande, executive VP, global general counsel, and chief sustainability and corporate affairs officer at Kraft Heinz.
However, as of 2020, Kraft Heinz had “no goal for cuts in overall plastic packaging use or in use of virgin plastic packaging, no goals on reusable packaging, no goals on recycled content, no plastic use data disclosure, and no support for producer responsibility,” according to the watchdog group, As You Sow.
Takeaways from the Final MRFF Report
The pilot program at J.P. Mascaro and Sons has investigated these three essential mechanical recycling system elements: facility processing, end markets and community curb collection. J.P. Mascaro & Sons has been collecting loose FPP collected via single-stream recycling programs with the pilot, sorting this raw recycled content at its MRF facility, and creating rFlex bales to sell as is or as possible feedstock.
For the pilot, J.P. Mascaro and Sons’ facility uses three optical sorters to “eject FPP from fiber” and a fourth to “clean up” fiber from the resulting FPP stream after the three lines converge. The report states “these high-end optical sorters had a wide build that allowed them to eject material across an entire fiber belt and work at high speeds with material spread out as far as possible.” A flex/rigid separator was installed to separate rigid items, such as containers, from the FPP stream.
Mascaro Sr. told Waste Dive in 2020 that “using optical sorters on the paper line instead of air transfer machinery ‘makes a lot of sense to me as an operator’ because it produces a cleaner paper line and simultaneously recovers numerous flexible plastic grades.”
The upgrades at the facility have diverted more than 2,728,250 lbs. of flexible plastic materials from the landfill. The 2023 report states that the economics were most favorable in areas with higher landfill tip fees due to avoiding residue disposal costs. Produced by Resource Recycling System (RRS), the report states that “60,000 households in 10 municipalities recycled FPP in their curbside cart with other recyclables.”
“There’s a significant opportunity for MRFs, flexible packaging manufacturers and the paper industry to work together on equipment upgrades to increase the quantity and quality of PCR supply for post-consumer recycled content products,” says Susan Graff, VP of global corporate sustainability at RRS.
Numerous suppliers sponsoring this pilot are evaluating the rFlex bale as feedstock and other end-user markets. The sponsors are a who’s who of suppliers in the food and beverage market, including Dow, Amcor, Charter Next Generation, Lyondelbassell, SEE (formerly Sealed Air), the Flexible Packaging Association, the Association of Plastic Recyclers, Chevron Phillips Chemicals and Westlake Chemical, to name a few.
Chicago-based Charter Next Generation is evaluating using rFlex as feedstock—pellets—and converting this material to produce blown films. CNG produces specialty films in 12 facilities across the U.S., and one of its facilities makes numerous types of PCR material into blown or cast film: high-density polyethylene (HDPE), low-density polyethylene (LDPE), low-light density polyethylene (LLDPE).
For this pilot project, CNG has added moisture additives to the rFlex PCR resin and successfully produced a film that can be used by film suppliers. The report says, “several film-to-film recycling end markets have reviewed rFlex bale composition data, visited the TotalRecycle MR, and /or tested the bale.”
Roof cover board manufacturers have been the primary buyer for the rFlex bale. Kraft Heinz, an MRFF research sponsor, launched a pilot project to demonstrate the use of rFlex at three of its manufacturing plants. Kelly Green Products, a commercial roofing company in Waterbury, Conn., is the most consistent buyer of rFlex bales, which are converted to roof cover boards. 2001 Company, the parent company to Kelly Green Products, has 50 to 60 clients using the rFlex bale roof cover board.
According to the MRFF report, Kelly Green Products is expanding from one to three board production board lines and will increase the ratio of post-consumer material of rFlex from 30% to 35%. Kelly finds the rFlex bale to be a low-cost, environmentally preferable feedstock compared to traditional materials like gypsum used to manufacture this type of board. The analysis also shows that using rFlex bale reduces CO2 emissions by 52% versus gypsum-based board production.
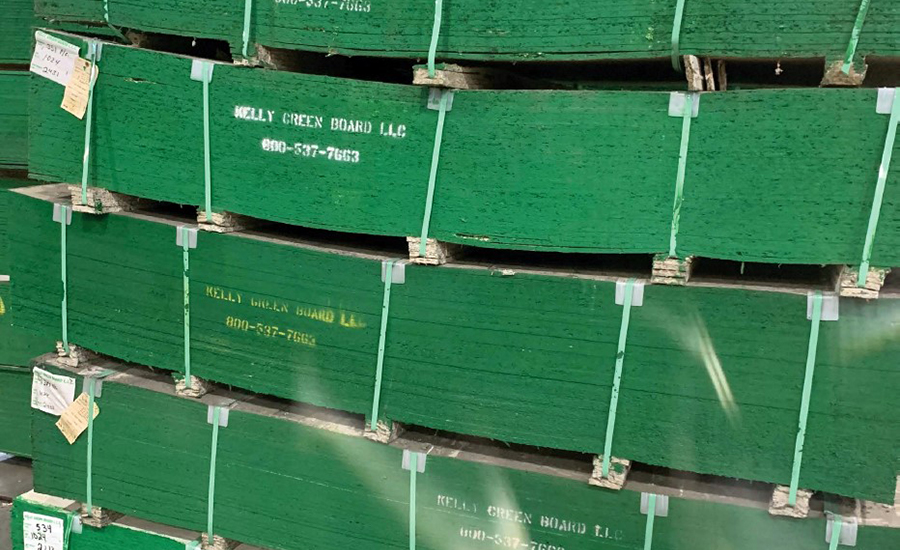
Mechanical Versus Chemical Recycling
As mentioned, with its recent venture capital announcement, Coca-Cola seems to be moving away from mechanical recycling to chemical recycling.
The bottom line is CPG companies need more PCR material to funnel back into their packaging to reduce virgin material use. Chemical recycling adoption rates are much higher in Europe due to robust recycling mandates like EPR, and the wind may be blowing in this direction. In late 2022, BASF announced it was supplying StePac with a chemically recycled polyamide 6 for food contact packaging. The new brands of resin will offer “built-in humidity control, which slows respiration inside the packaging, delays the aging processes, prevents microbial decay and preserves the quality and nutritional value of the produce during product shipment,” says BASF and StePac Ltd. Thirty percent of the packaging material will be composed this new recycled resin.
“Fundamentally, our joint vision is tackling the problem of high-performance flexible packaging materials that can’t be mechanically recycled with current technology,” says Christian Haupts, CEO of CARBOLIQ. “We aim to make them recyclable and therefore compatible with future needs.
While chemical recycling may be making inroads, many industry experts believe a comprehensive approach will be needed.
“Brands and packaging suppliers have an opportunity to work in the value chain to prioritize the economical recycling of flexible packaging by linking material and design choices with the collection, sorting, recycling of FPP and all packaging,” says Sand. “Procrastinating makes our collective future worse.”
Looking for a reprint of this article?
From high-res PDFs to custom plaques, order your copy today!