Building a Future Food Factory, Part 5: Labor
How to get the workers you need to run highly automated food and beverage plants
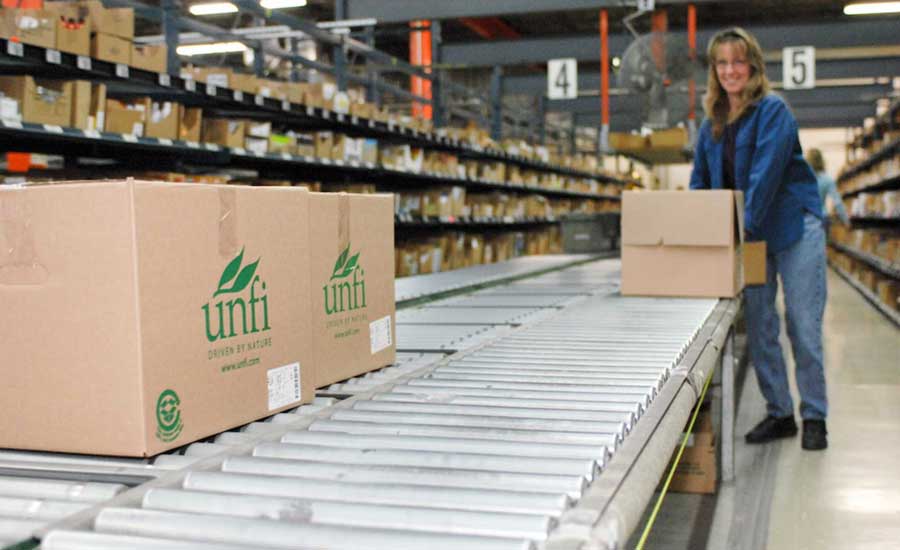
After several months of evaluation, United Natural Foods Inc. chose to build two distribution centers in Wisconsin—a 425,000 sq. ft. facility in Sturtevant, Wis. and a 300,000 sq. ft. facility in Prescott, Wis.
Source: WEDC.
In this series, we are taking a look at site selection issues and what really matters when choosing where to put your new food or beverage plant. All of these articles are based on the presentation made at the 2017 Food Automation & Manufacturing Conference by Karl Linck, vice president of engineering for Sargento Foods.
In part four, we discussed how the increased level of automation is affecting food and beverage operations. As noted in Food Engineering’s State of Food Automation, automation is the number one trend in the food and beverage processing industry. However, the number two trend is staff-related issues, particularly companies struggling to find qualified, skilled workers.
See more articles in this series:
So how do you ensure you get people with the right skill sets when picking a location for your new food or beverage plant? The first thing to consider is identifying an area’s tech school base and that they focus on what you need done at your plant.
“Wisconsin is an industrial state that has had to recover from losing a lot of industry. So their tech schools are primed and ready to go,” says Linck. “Most of the tech schools have a manufacturing center of excellence.”
In these centers, surrounding companies have donated to the schools to help train the students on actual equipment. Linck says Sargento Foods has contributed a new bagger to a local tech school and now that school offers a high-speed bagging degree.
“You may want to set up some custom training at tech schools,” he says. “Wisconsin’s tech schools not only do custom training, they’ll do evaluations of your employees. They’ll tell you what training they need, and they’ll do evaluation on the job.”
Another factor to consider is setting up in-house training programs and having in-house apprentices. This is when a company takes existing employees and foots the bill to put them through four-year programs. At the end of these programs, the workers are journeymen-level mechanics or electricians.
Linck advises companies look at installing friendly return-to-work programs, such as General Motors has called “Second Chance” geared towards women that have left the workforce to raise a family and are looking to get back in.
“A new thing by us (Wisconsin) is called ‘Youth Apprentice,’” says Linck. It’s a state program that allows Sargento to bring into its plants youth that are under 18, something usually barred by child-labor laws. “They shadow both in manufacturing and in our maintenance group because we really need those kinds of skill sets. And the kids are amazed.”
He says they are impressed by the production lines and equipment in Sargento’s plants. After those programs, the participating youth are inspired and can see a future for themselves doing those jobs.
“Their concept of manufacturing is lifting a case here to here,” Linck says. “They don’t understand the complexity of manufacturing today.”
To get the right people, it also helps to be the preferred place to work, Linck adds. And that is about treating people right.
But communities can help signal to food and beverage companies that they have the right area to locate a new plant by certifying sites as “shovel ready.” Frank Spano, managing director of Austin Consulting, says communities can do that by successfully completing a site certification program.
He says that having a certified food site can add “additional credibility to a community’s recruitment efforts by having the detailed site information documented and completed, which shows the community understands the importance of the site location process.”
In the next article, we will cover important legal considerations of selecting a site for a new food and beverage plant.
Looking for a reprint of this article?
From high-res PDFs to custom plaques, order your copy today!