Sustainability
Packaging industry pumps up R&D to keep pace with green goals

ProAmpac’s ProActive Sustainability Product Groups include recyclable flexible bags and rollstock, pouches with PCR content, and packaging that’s compostable or made with bio-based resin.
Photo courtesy of ProAmpac
More and more people seek a greener food package that’s not going to end up in an ocean or landfill.
One after another, food and beverage companies have declared plans to cut waste and move toward the ultimate goal: packaging materials that are reused over and over. Packaging suppliers and designers are engineering solutions to drive this shift without compromising on processors’ other priorities for product quality, manufacturing efficiency and more.
Packaging industry insiders at the recent PACK EXPO in Las Vegas noted that many larger processors are rolling out sustainable packaging in one brand or a small number of products to start. The industry also is waiting for the supply of post-consumer resin to get steadier as the United States tries to improve its recycling rates to catch up with Europe.
In flexible packaging, the industry is starting to see more starch- and bio-based materials, but they’re still expensive compared with alternatives and don’t yet offer the same barrier protection, says Jorge Izquierdo, vice president, market development, PMMI, the Association for Packaging and Processing Technologies.
But he still expects growth in biodegradable films because younger people are open to spending more for higher quality and sustainable features. Economic downturns sometimes dampen people’s willingness to pay a premium, and the industry is keeping an eye on reactions to the U.S. slowdown, Izquierdo says.
He does not expect the market for bio-based materials to bottom out though. “What we’re going to see is more of these options growing slowly the next two, three years, but we’re expecting that growth will speed up three to five years from now,” he says.
And he notes that flexible packaging, which saves energy and cuts waste, has room to grow in the U.S. He predicts that Americans will get more drinks in pouches soon, already common in Asia and Africa.
PMMI’s 2019 “Flexible Packaging Assessment” details some new ways manufacturers are driving sustainability:
- 3D printing with significantly cheaper molds
- Stains in film to help plastics degrade much faster in landfills
- Consolidation to fewer films to maximize scale in order quantities
Engineering recyclability
Graham Packaging calls its designers “shape sleuths” who design for recyclability, says Tracee Reeves, chief sustainability officer. “This includes using shapes, process technology and design technology to promote recyclability and advocate for lightweighting and functional features that minimize the environmental impact of our packaging.”
A few of the company’s efforts:
- Committed to 100% of bottles containing at least 20% PCR by 2025
- Partnered with a customer to create a resin of mostly sugarcane that’s widely used in the industry
- Testing bottles made with varying degrees of ocean-bound plastic, working with customers to bring the containers to market
Using a lot of PCR adds to package costs, and “customers are not always able or willing to accept some of the design and cost hurdles that come with a bottle having a high PCR content,” Reeves says. Let’s take a look at some recent sustainable packaging innovations:
Bear Naked granola recyclable pouch
Fresh-Lock, Dow and Berry Global
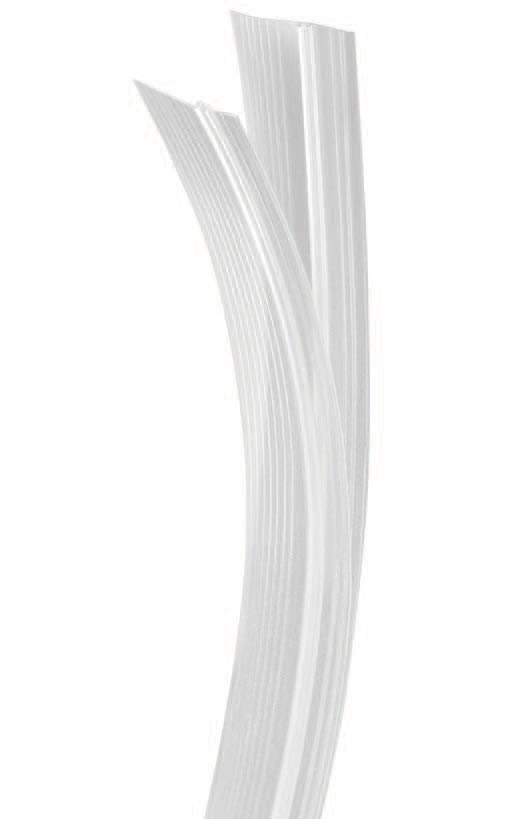
Fresh-Lock’s new recyclable zipper used for Bear Naked granola is compatible with film sealing systems.
Photo courtesy of Fresh-Lock
This partnership addresses an aspect of flexible packaging’s sustainability that consumers focus on heavily: how to dispose of it. Bear Naked granola from Kellogg Co. launched a fully recyclable standup pouch this year. Four companies partnered with the brand over 18 months to produce the packaging, ensuring each component met individual requirements for easy recycling.
Kellogg had used a service that required granola buyers to sign up for a program and ship flexible pouches for recycling. They can bring the new pouches to retailers using the How2Recycle drop-off.
Berry Global’s nine-layer Entour film structure provided the single-source polyethylene. The pouch has a clear window to showcase the product, is stiff enough to stand up on store shelves and is hermetically sealed easily.
The film uses Dow Chemical’s RecycleReady Technology that includes PE resins approved for How2Recycle. Dow also provided a high-performance sealant for fast production line speeds.
ColorMasters applied its registered matte to the pouch, providing extra heat resistance to run more efficiently on machinery.
Fresh-Lock developed a line of closures that people can recycle along with the film. “Sustainability is more than a fad. It is a consumer demand that brands need to not only recognize but also implement,” said Brad Hansen, president of Presto Specialty Products, a business unit of Reynolds Consumer Products.
Speeding monofilm projects
Mespack, Dow
Dow will use a Mespack horizontal form fill seal machine at its Pack Studios in Freeport, Texas, to speed up recyclable standup pouch projects and test customer film. The machine can run Dow’s RecycleReady films for store drop-off. Mespack, a Duravant company, notes that processors that already own its equipment can retrofit machines to use recyclable material.
“Every day another CPG company is committing to utilizing 100% recyclable material,” says Santi Alberich, marketing manager, Mespack. “We love that we are helping our customers and the environment at the same time.”
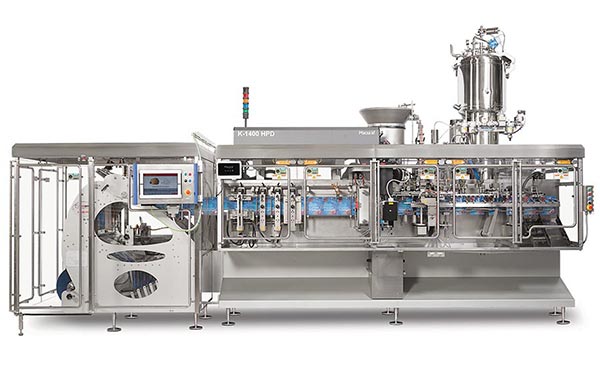
Dow will use a Mespack HFFS machine to test customer film.
Photo courtesy of Duravant
New vertical bagger for monofilm
Bosch Packaging Technology
Bosch introduced its SVE 2520 DZ for vertical form, fill and seal with a polyolefin monofilm. The machine produces up to 100 Doy Zip bags a minute. The speed and product protection compare favorably with conventional materials, Bosch says.
The company also is testing the optimum format part contours for forming paper that’s free of cracks and wrinkles. The material is stiffer than plastic films, and folding at some seams is a challenge. Plus, it is more likely to tear at high speeds.
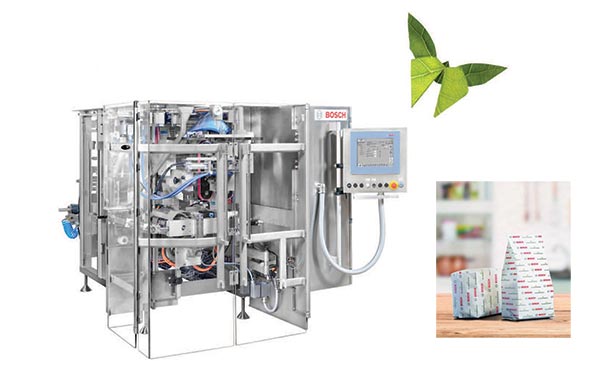
Bosch is working out the wrinkles in running paper pouches and has a new VFFS machine for mono bags.
Photo courtesy of Bosch Packaging Technology
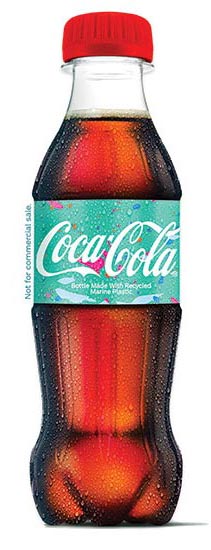
Coca-Cola Co. says this is the first plastic drink bottle made from recycled plastic ocean debris.
Photo courtesy of Coca-Cola Co.
First Coke bottle from marine plastic
Coca-Cola Co., Ioniqa Technologies, Indorama Ventures and Mares Circulares (Circular Seas)
Coca-Cola Co. introduced its first sample bottles made of recycled plastic taken from the ocean. The 300 Coke bottles used 25% recycled plastic collected from the Mediterranean Sea and beaches.
The proof of concept shows that enhanced recycling technology can convert used plastic of any quality into high-quality material for food and beverage packaging, the company says. Ioniqa Technologies uses a cost-effective proprietary process to break down lower-grade plastic components and strip out impurities.
New sustainable packaging line
TC Transcontinental
TC Transcontinental Packaging launched its vieVERTe line of compostable and recyclable products, which include post-consumer resin options. The company has pledged that all of its packaging products will be 100% reusable, recyclable or compostable by 2025. The company custom engineers proprietary structures to fit customers’ needs for rollstock or finished bags.
To help keep plastic from becoming waste and to reduce its footprint, TC Transcontinental will invest at least 1% of its packaging sector’s revenue to amp up its R&D efforts in this area. “We are taking an all-out approach to build out our vieVERTe brand products,” says Alex Hayden, senior vice president, R&D, innovation and sustainability.
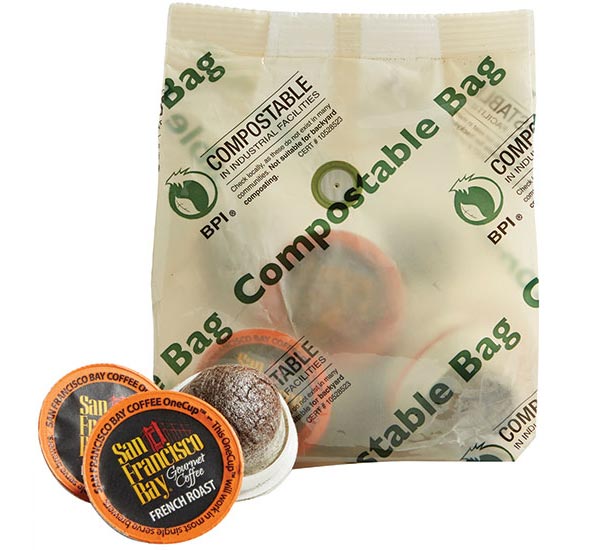
An example from TC Transcontinental Packaging’s new line of compostable and recyclable options.
TC Transcontinental
Recyclable pouch innovation
Coesia Group
Volpak has introduced technology to allow customers to make recyclable pouches of plastic or paper-based films. It’s available on new machines, and processors can upgrade existing Volpak equipment. The company says its SI-280 HFFS pouching machine is one of the only ones capable of running recyclable materials. Volpak started a research and design center called PouchLAB for sustainable pouches.
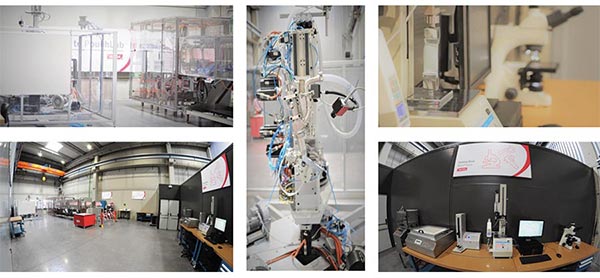
Volpak has a new R&D center for greener pouches.
Photo courtesy of Coesia
High PCR pouch, greener options
ProAmpac
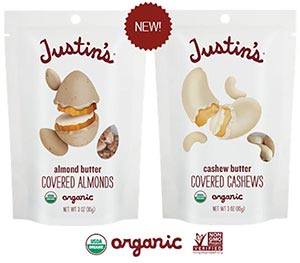
ProAmpac’s pouch made of a quarter post-consumer resin.
Photo courtesy of ProAmpac
This year, ProAmpac introduced a high-barrier pouch with 25% PCR for Justin’s Nut Butter Covered Nuts. The company says it’s one of the first commercial food pouches to use such a high proportion. ProActive PCR can incorporate FDA food-contact compliant PCR content into the sealant layer or print web of a package to meet sustainability goals.
The company debuted its ProActive Recyclable R-1000 high-speed VFFS and HFFS rollstock. It also offers recyclable premade standup pouches and a recyclable option for its Signature Surfaces Paper Touch coating. (See FE June 2019, “Flexible pouches offer touchable finishes.”)
ProAmpac CEO Greg Tucker says CPG pledges for packaging to be reusable, recyclable or compostable by 2025 pose a huge challenge.
“We’re delivering more sustainable flexible packaging options to our customers today and developing even more for the future,” he says.
For more information:
Berry Global, www.berryglobal.com
Bosch Packaging, www.boschpackaging.com
Dow, www.dow.com
Fresh-Lock, www.fresh-lock.com
Ioniqa Technologies, www.ioniqa.com
Mespack, www.mespack.com
ProAmpac, www.proampac.com
TC Transcontinental, www.tc.tc
Volpak, www.volpak.com
Learn more about the latest trends in food & beverage packaging
Looking for a reprint of this article?
From high-res PDFs to custom plaques, order your copy today!