Engingeering R&D
Get the temperature in a pipe without drilling a hole
No need to insert a thermocouple or RTD probe inside a pipe; this noninvasive technology simply straps/clamps onto the pipe in about five seconds

Ken Leibig, Omega Engineering’s director of engineering.
Take the temperature of a moving fluid inside a pipe without inserting a temperature probe, and get an accurate measurement through the external pipe temperature? You’ve got to be kidding. Is this some kind of a joke?
This was my first impression after spotting a new technology developed by Omega Engineering and presented in FE’s recent online Food Automation & Manufacturing Conference in the Exhibitors area (look under “Events” on the website). But I figured if anyone could pull it off, Omega could. After all, Omega wrote the book on temperature, literally speaking. I don’t think the over-1,000-page The Temperature Handbook is any longer in print, but you—like me—may have a copy of it sitting on a dusty shelf somewhere.
OK, my background is electrical engineering, so I’m not afraid of electricity. However, with plumbing and leaky pipes, that’s another story. Sometimes I feel like I have the reverse Midas touch when it comes to valves and piping. So, if you hate the idea of messing with pipes to get a temperature reading, this invention may be for you. You just strap or clamp it onto the pipe—something even I can do without upsetting the plumbing.
The HANI clamp-on temperature sensor can be installed in about five seconds; requires no cuts, drilling or welding; and provides immersion probe-level accuracy. Like what you might expect from an engineering company, the term HANI is an acronym that actually stands for “high accuracy, non-invasive.” As with other Omega sensor products, it comes with 4-20 mA output, and it can be coupled into standard controllers and PLCs with 4-20 mA temperature inputs. The device can also be coupled into a wireless gateway, and Ken Leibig, Omega’s director of engineering, tells me the company is also working on digital communications options as well.
Ken is the exuberant inventor of the HANI temperature sensor, and I spoke with him to find out more about this device and the work that went into the design of the sensor.
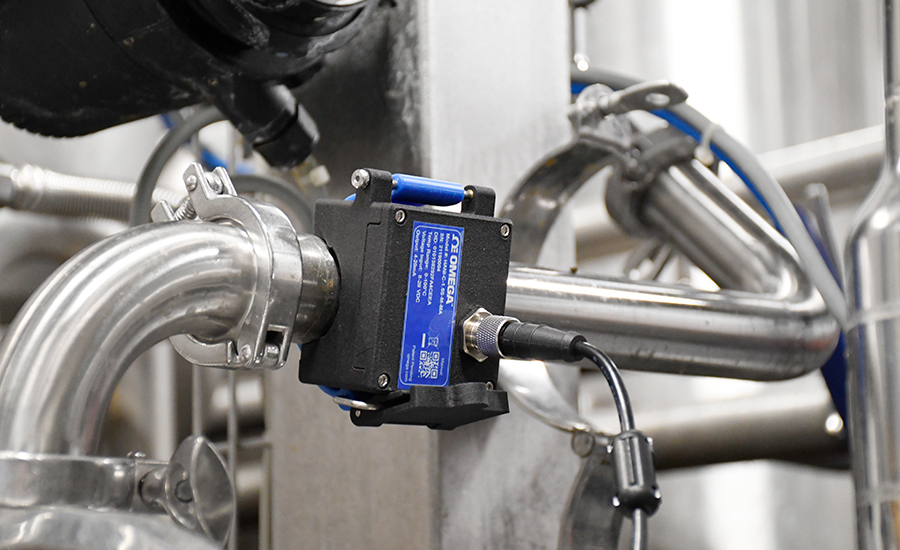
FE: Ken, there are no doubts that several industrial applications besides food and beverage could benefit from an accurate clamp-on temperature probe. What led you to develop a non-invasive pipe temperature sensor?
Ken Leibig: Here at Omega, we are always trying to make sensing and measurement as easy for our customers as possible. So, naturally, when we pitched the idea internally, it became an instant sensation. The use cases and benefits seem to grow every day.
FE: Food and beverage seems like a good application for this probe. Were you hearing anything from food and beverage people looking for particular solutions?
Leibig: Surprisingly, no one asked us for something like this directly. Food and beverage customers have lived with invasive probes being a necessary evil forever. Before the HANI, the only way to obtain a fast and accurate temperature reading was to get a probe in the process lines. After we came up with the idea, we went out and started talking directly to customers to validate our beliefs. During early development, we had a customer talk about the process of moving one of their invasive probes downstream to obtain a temperature reading closer to their canning line. The costs to shut their production line down for a day and bring in a sanitary welder just to move a sensing location by 8 ft. were tremendous. We have many smaller customers who simply can’t afford to add new immersion probe sensing locations. With the ability to clamp-on, read the temperature, clamp-off, and relocate in just minutes, the HANI is a game-changer. We also have larger customers who make food with inclusions (i.e. ice cream with chocolate chips). In these applications, immersion probes get coated in product and over time, they drift out of accuracy, respond slower to temperature changes, become difficult to clean—and sometimes even break off in the process. There are hundreds of use cases beyond just these two, and when you review all the pain points of immersion sensing together, it becomes a no-brainer that non-invasive sensing is the solution.
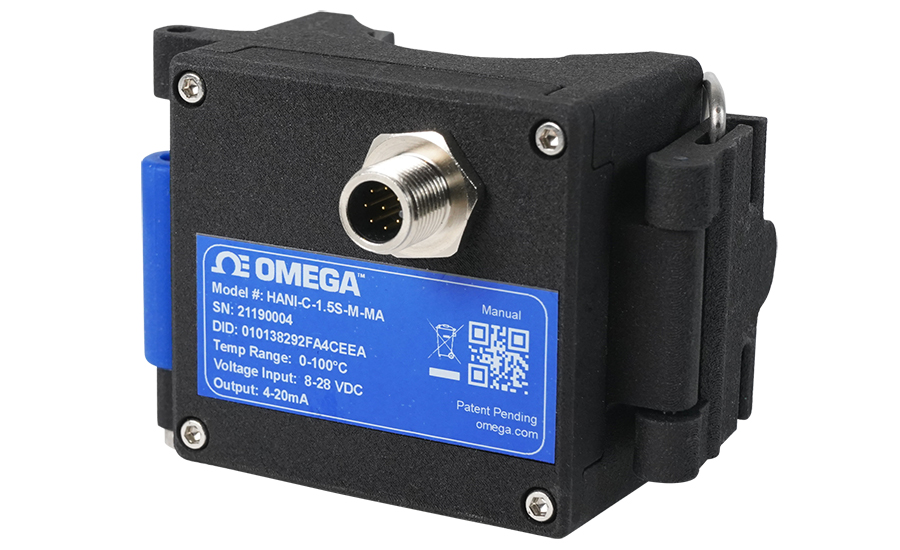
FE: Has Omega already applied for a patent?
Leibig: Yes, we filed a provisional patent application for this invention in February 2021.
FE: On what principle does the sensor work?
Leibig: The basis is Fourier’s law of heat conduction, q = -k∇T.
FE: Omega promises accuracy that is as good as an immersion probe. How do you do that?
Leibig: If we measure the temperature on the outside of the pipe, the amount of heat loss from the pipe and know a few common things about the pipe itself (i.e. thermal conductivity, thickness, and diameter), we can rearrange Fourier’s Law to determine the temperature on the inside of the pipe. We took this principle, packaged it in an innovative way and developed a proprietary algorithm to optimize the response time and accuracy of the sensor.
FE: What types of metal piping can be used and what thicknesses? What about diameters?
Leibig: All of them. The mechanical design is optimized based on the customer’s pipe diameter, but that’s the only thing that needs to be specified at the time of order. Currently, we can do any pipe size that is one inch or larger, but we should have something for smaller pipes soon, too. We left the pipe characteristics, like thermal conductivity, thickness and diameter, as user changeable input parameters to our algorithm. The sensors come pre-configured for stainless steel and standard wall thickness. We provide free software called Omega Sync that customers can use to change the sensor settings if they want to choose a material other than stainless steel or specify a thicker wall pipe. Since most customers don’t know the thermal conductivity of the pipes they’re using offhand, we pre-loaded a list of common materials that our customers use—such as stainless steel, carbon steel, galvanized steel, copper, brass and aluminum. Plastic and glass pipes are currently under development.
FE: How do you set up and calibrate the temperature sensor? What software is required?
Leibig: To mount, all you have to do is wrap the sensor strap around your pipe and pull the quick-latch mechanism, which automatically sets the tension for the specified pipe diameter. One of our brewery customers described it as “literally the easiest thing I’ve ever done.” It takes 10 seconds to unbox and mount. Electrically, there are two ways to connect. The first is with a loop powered 4-20mA analog system, which is usually the preference when a customer wants the sensor hard-wired in for long-term monitoring and control. If you would rather take easy ad-hoc digital temperature readings, you can use an IF-001 M12 to USB cable to connect the sensor to your laptop, and use our free Omega Sync software to read and log the temperature data. Every sensor gets a standard two-point calibration from the factory; so if you’re using a standard-wall sanitary stainless steel pipe, the sensor is plug and play. If you’re using a different pipe material or non-standard wall thickness, just use the M12 to USB cable and Omega Sync to change the settings.
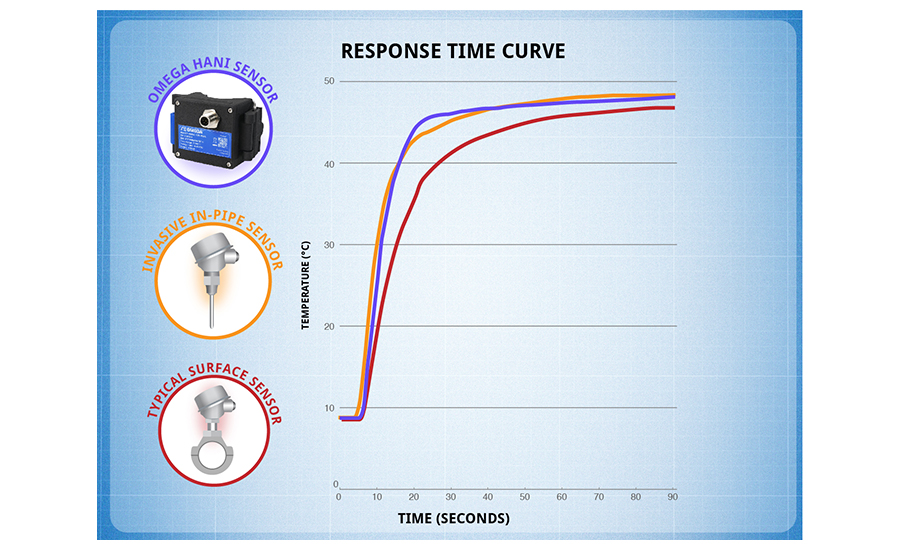
FE: What are the process media that can be measured? What is the recommended ambient room temperature where piping temperature will be checked?
Leibig: Currently, we support most liquid process media. We do not yet support fluids in gas form. The accuracy spec (±0.5°C) was developed around water-based fluids and has been validated in customer applications for fluids such as beer, ice cream, tomato paste and 50/50 glycol/water mixtures. We suspect that fluids with low thermal conductivities, high viscosities and low flow rates will be less accurate out of the box—but through Omega Sync, customers can perform a one- or two-point calibration in their own application to bring the accuracy within the advertised ±0.5°C for sanitary applications. The recommended ambient room temperature is between 0 to 40°C.
FE: Since this device makes no internal connection to the process media, is it authorized for sanitary applications?
Leibig: The current sanitary industry standards (like 3-A) are primarily concerned with the product contact surface requirements (i.e. surface finish, minimum radii, etc. or all the food contact surfaces). Since the HANI doesn’t contact the process media, most of the standard requirements don’t apply. Of course, there are some general guidelines on non-product contact surfaces (mostly around cleanability) that we have designed around. We plan to move forward with official 3-A certification in the coming months, but none of our existing food & beverage customers have required it, since the HANI is completely non-invasive.
FE: How does this technology compare with other temperature sensors on the market? Is anyone else making this type of sensor that you know about? If so, how does HANI differ from others?
Leibig: The HANI is the only temperature sensor on the market that uses a thin-film heatflux sensor to assist in the temperature calculation. This and the proprietary algorithm are the basis for the patent application and are what enable the Omega HANI sensor to have the best accuracy (±0.5°C) and response times (t63 = 5 sec) on the market for non-invasive temperature sensors. In fact, the HANI is the only non-invasive temperature sensor that has response times and accuracies comparable to an immersion RTD temperature sensor. It’s also the only sensor of its kind that can be mounted in just a few seconds and without any tools. And, I should also mention, the HANI is less expensive than the other non-invasive temperature sensors on the market.
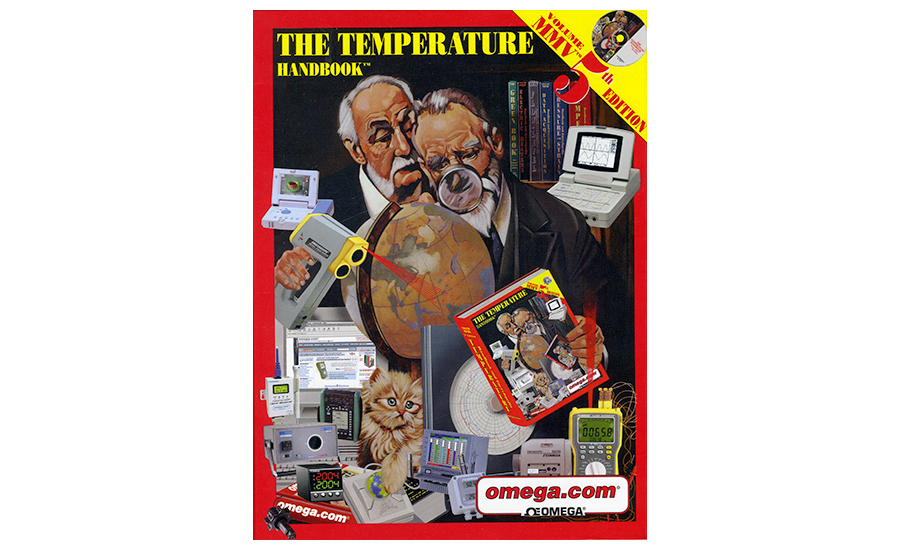
FE: Is this sensor available now? Is there anyone in food and beverage using the device, and if so, what have been their reactions?
Leibig: You can purchase both industrial and sanitary pipe versions of our HANI on our website. We have many customers in food and beverage already using the HANI in breweries, milk pasteurization plants, ice cream plants, yogurt plants, canning lines and more. Through the development of this product, we’ve met a lot of great people who were willing to test it out and give us some great feedback. Their initial reaction is: “Wow, how do you do that?” And then: “Great, where can I buy one?” We had a booth at the Craft Brewer’s Conference in Denver a couple months ago, and I must have heard “This is perfect for my knockout!” about a hundred times. Saucy Brew Works in Cleveland was one of the earliest breweries to adopt the technology.
FE: What’s next for this technology?
Leibig: We’re continually releasing new pipe sizes on our website as we find new applications, but pipes are only one of the application interests we currently have. Actually, we are now working with a few OEMs to develop this technology for tank and kettle F&B and Pharma applications.
FE: Anything I forgot to ask that is important?
Leibig: The HANI has a 4-20 mA analog output, but is also a smart sensor that is IIoT/Cloud ready for wireless monitoring with Omega’s Layer N Ecosystem.
For technical information, read Omega HANI User’s Guide: https://assets.omega.com/manuals/HTS-HANI-CLAMP-S_Manual.pdf.
Looking for a reprint of this article?
From high-res PDFs to custom plaques, order your copy today!