Engingeering R&D
Divorcing the plastic from our packaging not so easy without a new suitor
A startup company seems to have found that suitor: A natural coating from cellulose that can be recycled along with the packaging

Recyclable plastic-free pouches with Melodea’s barrier products, which protect food contents. Photos courtesy of Melodea
FE’s Manufacturing News lead story in November 2021 featured an article entitled, “Back to paper bags and cups: Old is new again.” The article looked at methods of reducing plastic packaging and going with what seems like yesteryear’s packaging materials—paper and cardboard—which, of course, are easily recyclable and usually biodegradable when compared to many of their plastic counterparts. While food and beverage companies are indeed interested in removing the plastic, the one deterrent is that paper and cardboard materials on their own aren’t very good at protecting their contents, nor keeping their contents from oozing out. Plastic materials just don’t have this problem.
Before plastic and Styrofoam®, paper/cardboard cups were wax coated to provide a protective barrier to cold contents. In years past, Kraft paper lunch bags often had no coating at all, so sandwiches were wrapped in foil or put in wax-coated sandwich bags.
And it’s not that food and beverage processors don’t want a divorce from plastic in packaging, but getting out of the relationship isn’t so easy. For example, in the news story noted above, Chobani’s new yogurt cup is 80% paperboard, but it still needs a thin plastic lining to protect its content.
While this combination of materials in a cup “is a step in the right direction” as Chobani Founder and CEO Hamdi Ulukaya says, it still presents a problem for some recycling companies, as the plastic-lined cups are not recyclable as plastic, nor are they necessarily recyclable as paper, leaving the only option to incinerate the material. Ulukaya says this is just the beginning in protecting the environment. What is needed, however, is a coating material that is recyclable along with the paper cup—but without the plastic lining.
New bio-based startup, Melodea, has come up with a solution to take on the plastic waste/recycling problem. The company has developed MelOx, a high-performance, plant-sourced barrier coating that protects packaged products from oxygen, oil and grease transmission. Melodea has also developed VBcoat, which protects packaged goods from water vapor, oil and grease transmission.
Melodea sources it barrier coating material for packaging from wood pulp, the same material used to make paper. The coating solution allows paper and packaging producers to move away from plastic coatings. These new materials are sustainable and recyclable, and do not contribute to plastic waste pollution. “Cellulose, the primary building block of the cell walls of all plants, is the most abundant biopolymer on the planet,” says Shaul Lapidot, PhD, CEO and co-founder of Melodea.
“It provides plants with extraordinary strength, and is a lightweight—yet strong—material. We found that this bounteous and renewable material can be utilized to produce novel, eco-friendly packaging alternatives for the packaging industry,” says Lapidot.
Obviously, when I heard about this, I had to ask Lapidot to provide some details. First, he said the company was originally founded as a spin-off project at the Hebrew University of Jerusalem by himself, together with composites expert, the late Tord Gustafsson, and Professor Oded Shoseyov, PhD, a renowned expert in nanomaterials and plant biotechnology who is on the Melodea advisory board.
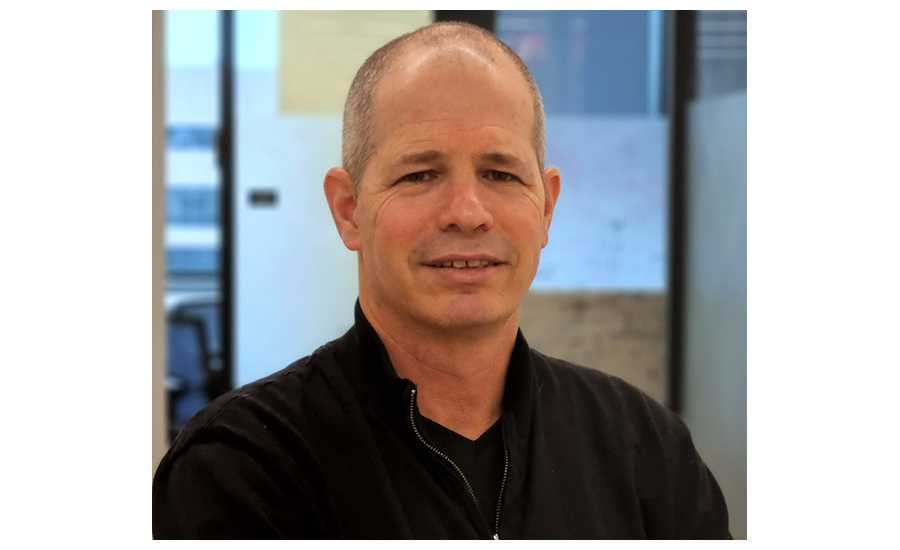
FE: Do you have patents on this new technology?
Dr. Shaul Lapidot: Melodea’s technology is protected by 14 patents, including several covering its production processes and product portfolio. Melodea was a winner of two of the most prestigious awards in the packaging field, the Packaging Europe 2019 sustainability award and the WorldStar Award for 2020, granted by the World Packaging Organization. We are positive that our products will make a tangible positive impact on reshaping the trillion-dollar packaging industry, helping to transform it into a more circular and sustainable industry.
FE: What drove you to inventing MelOx and VBcoat—and starting Melodea?
Lapidot: Since its incorporation, Melodea focused on the production of Cellulose Nanocrystals (CNC) as a bio-based raw material for various applications that would serve both the relevant industry and the environment.
We recognized the need of the packaging industry and more correctly the entire world—to find solutions for the plastic waste challenge. We already had in hand the strong bio-based material CNC that we produce through a patent protected process. We believe that the solution for a sustainable packaging industry grows on trees—as the industrial forest is the best source for bio-based raw materials such as CNC. The CNC provides protection from oxygen transmission but cannot stand in high humidity. Therefore, we invested in the development of a unique formula that has high performance in high humidity conditions—MelOx. In order to offer our clients with the entire solution for their sustainable packaging that has high performance while being recyclable, we also developed the Melodea VBcoat that offers protection from moisture transmission.
FE: Can you tell me about the process used for making these coatings?
Lapidot: Our production process for CNC is patent-protected and sustainable as it includes recycling of up to 95% of the materials in the process and requires low amounts of energy and water. As we believe that the solution for a sustainable packaging industry grows on trees, we use the pulp made from industrial forests. Any pulp can be used for our production. Last year Melodea launched an industrial production site for CNC in Israel. We currently produce the MelOx and Melodea VBcoat at a site in Israel and we are currently setting up a new site in the United States for the production of MelOx and Melodea VBcoat that will serve our clients in that area.
FE: What is involved in adhering these coatings to substrates?
Lapidot: Both MelOx and Melodea VBcoat can be applied by standard coating machines, including gravure, rod coater and slot die without the need of special equipment. Almost any substrate can be coated including paper, paperboard, bio-plastic and plastic.
The reason for coating paper is obvious. So why do we coat plastic?
Getting rid of all plastic on earth will not occur in one day or even a few years. However, we can reduce the amount of plastic and make recyclable plastic packages by applying our products instead of different types of plastic or aluminum.
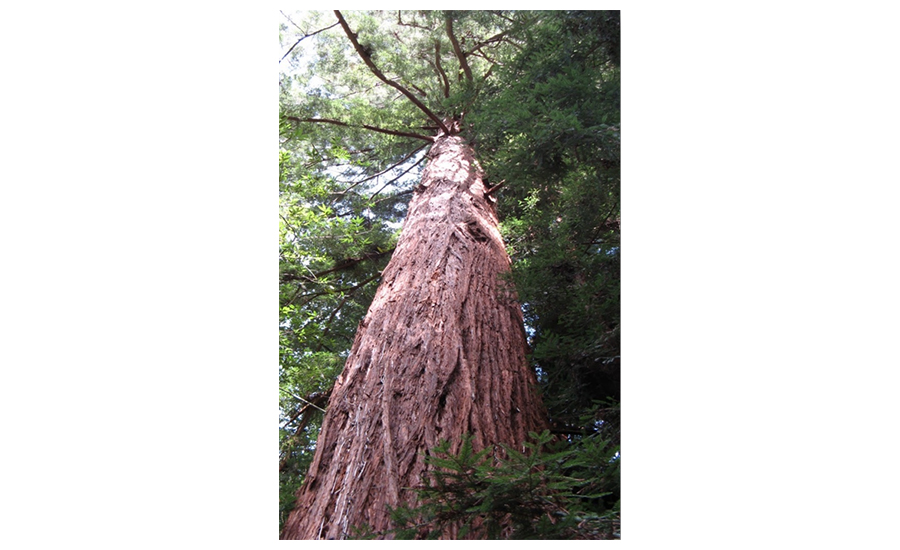
FE: What are the differences between MelOx and VBcoat?
Lapidot: Melodea has two different recyclable barrier products—both can be applied on almost any substrate by standard industrial coating machines.
MelOx is for protection from oxygen and oil and grease transmission and is based on a bio-based material produced by Melodea from the industrial forests—cellulose-nanocrystals.
Melodea VBcoat is for protection from water vapor transmission. It can be applied by itself or on top of MelOx.
MelOx and Melodea VBcoat can be applied together on paper or bio-plastic to replace plastic products, and MelOx can be applied on recyclable plastic to replace non-recyclable plastic packages.
FE: What applications best fit MelOx and VBcoat?
Lapidot: MelOx and Melodea VBcoat can serve different types of flexible packaging such as paper and plastic pouches, tubes, lids and more.
FE: Is there a theoretical shelf life of these coatings once applied to packaging materials?
Lapidot: Shelf life should be similar to the current shelf life provided by standard packaging on the market.
FE: Let’s say that one of the coatings is applied to a paper yogurt cup. What kind of shelf life can be expected once the cup is filled with yogurt?
Lapidot: Should be the same as the current shelf-life of such a product on the shelf.
FE: Are there pH ranges that won’t work with these coatings, like tomato or orange juices?
Lapidot: No, as in these types of products the structure is such that Melodea’s coating is protected by another layer.
FE: Are these coatings available now? Are you working with food companies to test these products?
Lapidot: Of course. MelOx and Melodea VBcoat are available and already purchased by leading companies across the packaging value chain that wish to lead the eco-friendly packaging market. We are working with packaging companies that apply our materials, and food and consumer goods companies that provide specifications and perform pilots and shelf-life testing. While converters and paper companies apply the materials, the food and consumer goods companies are those that dictate the needs of the market.
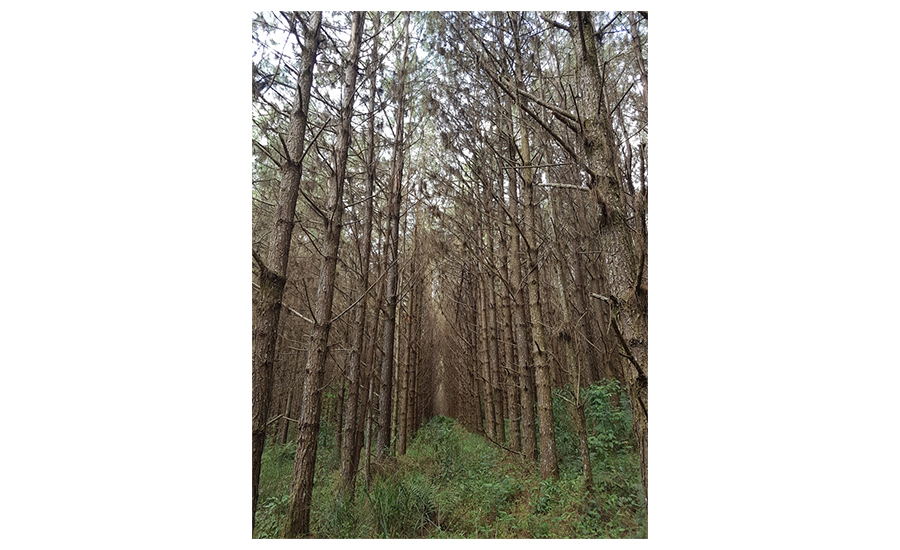
FE: What success stories have you had so far?
Lapidot: MelOx and Melodea VBcoat have the best performance on the market while still being recyclable. They were industrially tested and found successful by various clients that include Tier-1 companies.
Except for direct sales, Melodea is engaged in commercial agreements with some of the leading companies, packaging, food and consumer goods industries. Melodea has also entered into a major licensing agreement that will be published soon, so stay tuned.
FE: How do costs compete with comparable, existing technologies?
Lapidot: Costs are competitive to existing green solutions. According to Melodea’s business model, costs will continue to reduce as more licensing agreements are signed and production plants will be spread globally.
FE: Anything to add?
Lapidot: I want to clear some of the confusion for consumers that often hear the words “compostable” and “biodegradable.” It should be noted that although compostability / biodegradability of a package is positive, the infrastructure for composting is not ready and can take years for many countries to adopt, while the infrastructure for recycling already exists. From that reason, even though we use compostable and biodegradable materials we focus on recyclability of our products when applied on both paper and plastic as a key factor for eco-friendly packaging in the short term of the next years.
For more information, visit https://melodea.eu/.
Looking for a reprint of this article?
From high-res PDFs to custom plaques, order your copy today!