Automation
Flexibility is key for automated pallet movement in cold storage facilities
Automated storage and retrieval systems have emerged as highly desirable solutions for refrigerated and deep-freeze warehouses

The Rover shuttle runs on a small 5 hp motor powered by a lithium-ion battery.
All photos courtesy of Advance Storage Products.


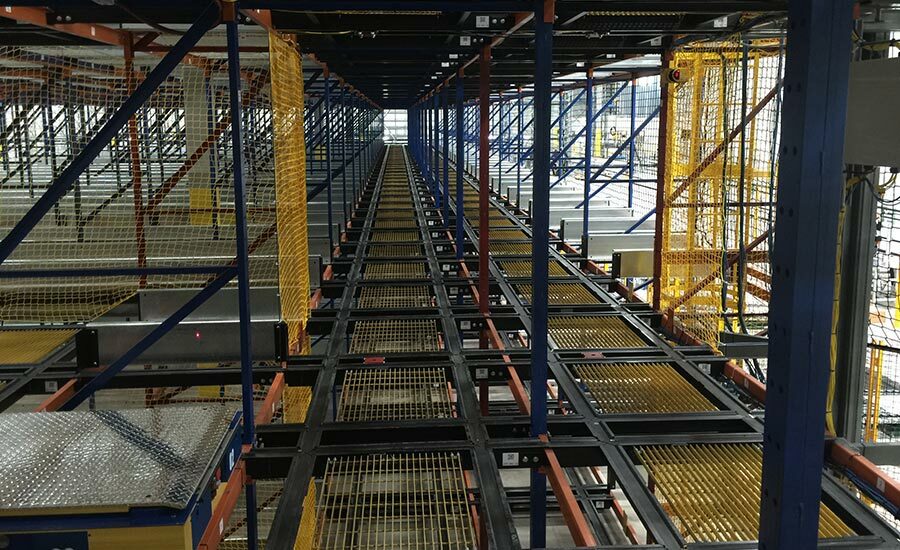






Because of increasing consumer interest in a more diverse product selection, healthy foods, and more convenient meal preparation, food manufacturers in dairy, meat, baked goods and produce are supplying a widening array of new SKUs in both chilled and frozen formats. This places an ever increasing demand on cold storage, and with older facilities, it’s not very easy to automate them.
FE interviewed Mads Jespersen, vice president automated systems, Advance Storage Products, to get a handle on the problem, and look at an alternative solution for older cold storage warehouses. Joining Advance Storage Products in 2017, Jespersen has been a professional engineer for more than 25 years, as well as an experienced manager and leader. He holds a B.S. in Mechanical Engineering from the Technical University of Denmark and an MBA and AME (Advanced Managerial Education) from CEDEP, INSEAD campus in France. He is certified in Stage Gate, LDP and Enneagram.
FE: So, what’s your view of the market for chilled and frozen foods?
Mads Jespersen: New offerings in meat and seafood ready meals, dairy, fruits and vegetables, pizza, bakery and desserts, and prepared pasta and potato products continue to fuel the growth of frozen and refrigerated foods. The frozen food sector is expected to grow globally at a compound annual growth rate (CAGR) of 5.2 percent between 2017 and 2023, according to industry analysts. Similarly, growth in refrigerated foods during this period is expected to reach 3.0 percent CAGR.
This escalating demand for chilled and frozen food products worldwide has made refrigerated warehousing a continually expanding sector for distribution. A study published by the International Association of Refrigerated Warehouses (IARW)—the 2016 IARW Global Cold Storage Capacity Report—shows 210 million cubic feet of refrigerated space was added to North American warehouses between 2014 and 2016, representing a 2.3 percent annualized growth rate. Worldwide, 1.7 billion cubic feet of refrigerated space was added to warehouses from 2014 to 2016, with an annualized growth rate in cubic footage of 4.2 percent.
FE: What are the challenges of the cold-storage environment?
Jespersen: Cold-storage warehouses pose definite challenges for food processors, distribution centers and retailers that endeavor to have facilities operating at a high level of efficiency. Handling deep-freeze and refrigerated meats, dairy and produce is a very complicated food distribution activity requiring management of temperatures, time and lot tracking, efficient rotation of inventory and complete quality control.
Most refrigerated warehouses are manually operated, and when compared to ambient-temperature facilities, have a much higher incidence of product damage, missed product rotation and wrong item fulfillment. These warehouses also have heightened facility, equipment and product damage, primarily caused by manually-operated fork lifts impacting racks and doors, significantly higher than that found in ambient temperature warehouses.
While the temperature in these facilities is cold enough to store food products safely, it creates an extreme environment with difficult working conditions for personnel, increased safety issues, and staff recruitment and retention problems, particularly with deep-freeze facilities. This puts refrigerated warehouses that are operating manually at a disadvantage with regards to throughput, order accuracy and cost efficiency.
FE: What about using off-site cold storage?
Jespersen: Supply chain executives in the refrigerated food and sector are faced with considerable challenges when balancing production runs, inventory volumes and delivery schedules. Facility managers are increasingly required to store more products in existing cold-storage warehouses, and to retrieve them faster for growing volumes of just-in-time orders to retail stores.
Space utilization within refrigerated production warehouses is at a premium, and they are consistently running out of space. Finished products are frequently stacked on floors and aisles, which contributes to increased fork truck accidents, spillage and damaged products, and lost and expired inventory.
These issues are forcing many food manufacturers to expand the footprint of their cold-storage facilities. More often than not, there is no longer much room available in adjoining spaces or buildings. Consequently, off-site cold-storage space for raw materials and finished goods is likely the only option. This requires facilities, labor, energy and equipment to manage. If the manufacturer is warehousing items that require refrigeration or freezer storage, the costs can be considerably amplified.
Third-party logistics (3PLs) are also a growing storage solution for food manufacturers. Although most contemporary 3PLs run highly-efficient cold-storage operations, transporting pallets of product to off-site storage incurs rental costs, increased transportation costs, and loss of last-touch product control which can increase product damage and returns.
FE: Processors often have refrigerated storage spaces, but often these are not readily adaptable to automation, are they?
Jespersen: Food producers and distributors are looking more closely at their refrigerated warehousing, and how they can more cost-efficiently balance their inventory against production and delivery. Key to this equation is building in automation with a high level of system flexibility that will allow changes in pallet storage paradigms, throughput volumes and system configuration as conditions require. For refrigerated warehouses, this means a solution that will ensure high-density pallet storage to minimize energy costs, as well.
FE: Crane-based AS/RS systems have been the common automation solution. What are their advantages and disadvantages?
Jespersen: At first look, crane-based automated storage and retrieval systems (AS/RS) come to mind. They optimize cubic space usage—so critical in cold storage—not only by their vertical stacking capability, but also by minimizing aisle cubic footage. By eliminating the need for fork lift trucks, aisles can be made significantly more narrow, allowing 12-foot-wide aisles to become just 5-foot wide as in the case with very narrow aisle (VNA) cranes. This space can then be condensed for higher density pallet storage.
Crane-based AS/RS solve the problem of achieving high-density, automated cold storage, and the problems associated with product- and facility-damage resulting from manually-driven forklifts, but basically, they are ridged systems. They are designed to fit a specific storage and throughput model, and if that model needs to change to a different paradigm—as is currently endemic in the food processing industry—then the warehouse is pretty much stuck with that original AS/RS throughput model. So long as the storage game plan doesn’t change very much, that AS/RS will likely remain a highly-efficient automation solution to move pallets.
Conventional brownfield cold storage warehouses that support food manufacturing, which have low ceiling heights, are typically not good candidates for crane-based AS/RS. Even though these facilities may have the same requirements for high-density, high-throughput storage and distribution of pallets, it is the high-bay configuration that permits crane-based AS/RS to deliver its most cost-efficient advantages. This, to a great degree, makes crane-based AS/RS an unlikely option for the vast number of food processors functioning in brownfield facilities, and even further exemplifies the limitations on the applicability of these systems.
FE: Your company makes shuttle pallet storage systems. How do they solve the problem of automating in older facilities? What’s the problem with crane-based systems?
Jespersen: What is missing in crane-based systems is the flexibility to modify system design, throughput volumes and storage configurations to adapt to changing distribution requirements. For many refrigerated food producers and distributors, this solution is emerging in the form of automated three-dimensional, shuttle-based high-density pallet storage.
One of the newest and more flexible of these shuttle-based systems is what we call Rover. Rover can solve high-throughput storage needs in cold storage facilities that cannot be addressed by other solutions. It is an automation solution that adapts to any warehouse—no matter the ceiling height or size constraints.
The Rover system is a three-dimensional, shuttle-based, automated pallet storage, retrieval and delivery system that is highly configurable, flexible and scalable. The system is capable of operating in temperatures down to -22° F. Powered by lithium-ion batteries, the shuttle vehicles can operate, transporting pallets, for 8 to 10 hours before requiring recharging.
Unlike conventional racking systems or crane-based AS/RS, Rover shuttle vehicles move simultaneously and tri-directionally throughout the storage rack. The system consists of very few moving components—shuttles, vertical reciprocating conveyors (VCRs), and a short inbound and outbound conveyor—making for very simple operation.
VRCs are used instead of fixed-aisle cranes and aisles, and the system enables storage locations of more than 20 pallets deep. Consequently, Rover, and systems like it, provides the industry’s most dense automated pallet storage, which delivers improved cold retention in refrigerated facilities.
FE: Are these systems flexible?
Jespersen: These pallet shuttle systems are tremendously flexible. Here are some examples.
FIFO and LIFO—For high-density storage in FIFO or LIFO configurations, these cold storage systems permit multiple SKU’s to be easily stored and accessed on any aisle and any level as needed. Deep-lane and shallow-lane storage can be easily accommodated within the same racking structure, without any additional equipment, and little or no modification to the system.
SKU profile changes—These systems support the flexibility to change to new SKU profiles, such as to accommodate a shift away from an 80/20 percent mix of fast- and slow-moving SKUs, to a 60/40 percent mix, as distribution operations require. Much simpler and cost effective when compared to crane-based AS/RS, which would require a change-out of crane types from satellite to forked, and new racking.
Expansion and reconfiguration—Significantly simplified when compared to crane-based AS/RS. It is just a reconfiguration of the physical rack system.
Scaling throughput—Throughput is scaled by simply and easily adding or removing shuttles as needed.
FE: What about energy usage? Are these systems energy efficient?
Jespersen: Deep-freeze distribution is the most energy intensive warehousing sector, with chilled facilities being the second most. In effect, these warehouses are giant insulated freezers and coolers which extract heat to produce a refrigerated environment. The removal of this heat comes at a hefty energy cost. Refrigeration energy costs are the second highest expense, next to labor costs, in cold storage warehouses.
Refrigeration draw and automation energy usage are interrelated, as the heat generated from the automation must be removed from the facility. When energy-efficient automation is implemented into a cold-storage facility, the energy and cost savings potential can be considerable. The low-energy requirement of the automated shuttle vehicles supports the initiative to reduce energy usage in cold storage facilities. The shuttles use 90 percent less energy than that of AS/RS cranes—5 hp motors compared to 50 hp motors used on cranes.
FE: How flexible are these systems in terms of pallet movement?
Jespersen: The Rover system is unique in that it brings an extended flexibility capability to pallet shuttle systems in cold-storage environments. The simplicity of adding track for the shuttles can extend beyond the storage locations of the Rover system, and easily integrate to interfacing operations of receiving, pick replenishment, layer picking, end-of-line production and shipping.
As product comes off the production line, for example, pallets can be staged for delivery to the loading dock using pallet racking or a gravity-flow conveyor, instead of conventional powered conveyor.
Around-the-clock operation of the system allows for off-shift staging, so pallets can be sequenced for loading. When the trucks arrive, they can be loaded very quickly by assigning a shuttle to constantly bring the pallets forward for loading into the truck.
FE: Fresh fruit storage is always a problem. How do you prioritize movements to keep it fresh?
Jespersen: The Rover technology is ideally-suited for optimized product handling of fresh fruit requiring refrigeration, incorporating damage-free conveying, precise product tracking, and first-in/first-out movement of bulk crates to ensure product freshness.
Facilities requiring precision environmental control, such as for apple sorting, packaging and storage, are prime candidates for Rover.
Rover delivers efficient and high-throughput movement for individual pallets with individual time and lot identification throughout the warehouse and production facility, permitting the processor to maintain precise control of its fresh fruit products through every stage of their handling—from receiving, to sorting, storage, and through packaging and shipping—while supporting the facility’s capability of monitoring batch numbers, processing dates and weight as the palletized fruit is moved through and shipped in the facility.
FE: Can Rover work in all warehouse architectures?
For cold storage warehouses confronted with ceiling height and space restrictions, automated three-dimensional shuttle pallet storage systems, like Rover, present an ideal solution for the utilization of existing warehouse space, as opposed to the necessity of expanding into larger warehouse facilities to accommodate manual pallet-handling operations. But, these systems can also extend into high-bay heights of 70 feet or more, directly competing with high-bay AS/RS.
These automated shuttle systems have emerged as highly flexible solutions to many issues relating to pallet movement and storage in refrigerated and deep-freeze warehouses.
For more information: Kevin Darby, Automated Systems Solutions Manager, Advance Storage Products; 15302 Pipeline Lane, Huntington Beach, California 92649; Telephone 714-657-1608; email kdarby@asprack.com; www.advancestorage.com.
About Advance Storage Products
Advance Storage Products (Advance) manufactures engineered-to-order structural rack systems. Started in 1958 in southern California and still family-owned today, Advance has become a major structural rack system producer, serving customers in the US and abroad. With a long history of innovation, the company offers turnkey systems from purchase through warranty.
Advance has successfully completed over 10,000 systems, and manufactures over 100 million pounds of structural rack solutions per year. Its production facilities are state-of-the-art rack system manufacturing facilities located in Cedartown, Georgia and Salt Lake City, Utah. Advance produces nearly half of the pushback systems sold in the US, and offers all types of long-lasting structural pallet storage systems, from static selective rack to dynamic, high- density systems, as well as rack-supported order-fulfillment structures including pick and flow systems.
In March, 2017, Advance introduced Rover, the next generation of automated pallet storage and retrieval systems. Rover is a highly configurable, 3-dimensional shuttle-based AS/RS that is cost effective, flexible and scalable. The system is ideal for manufacturers and distributors, including those in the food and beverage industries whose operations demand flexible high-density storage with high throughput.
Looking for a reprint of this article?
From high-res PDFs to custom plaques, order your copy today!