Workforce Trends
Evolving Plant Floor Technology Reshuffles Operator Skills
New technology coming to the plant floor, such as augmented reality and artificial intelligence, is making an impact on operator roles in 2023

New technology coming to the plant floor, such as augmented reality (AR) and artificial intelligence (AI), is making an impact on operator roles in 2023. Large capital investments in automation by food manufacturers have reshaped plant floors over the last 10 years, but those improvements tended to be substantial and longer projects, such as industrial network updates or changing to new programmable logic control (PLC) platforms. With these plant updates, manufacturers did the training in-house or had third parties help with workforce training.
So, how is training changing with new technology, and how should senior management look at plant personnel in 2023?
Back in April, Joe Campbell, a senior manager of application development at Universal Robots, said food executives were minimizing workforce issues. “There are still so many senior people who believe it's a short-term problem,” said Campbell back in April 2023.
However, the Rockwell Automation and Sapio Research 8th Annual State of Smart Manufacturing Report shows how that may change. One rather large finding from shows “that in last year’s report (2022), just 35% of respondents reported that their organization lacked a skilled workforce to outpace the competition over the next 12 months.”
In the 2023 report, this changed dramatically and revealed “an 11% year-over-year increase to 46%, and now represents the top concern for manufacturers in relation to competitiveness.
Moreover, the report says that “36% of manufacturers are repurposing existing workers to new or different roles.”
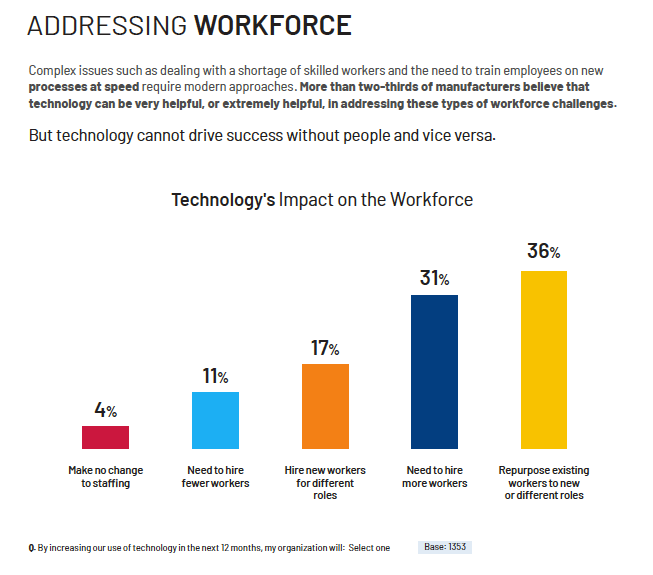
So, this wave of smart manufacturing technology investment on the plant floor creates new job duties and demands workforce training. The smart manufacturing report shows that “17% of companies need to hire new workers for different roles” and “41% of global manufacturing leaders surveyed reported training current employees on updated processes as the biggest workforce-related obstacles they face, including food and beverage manufacturers.”
“Our customers are telling us that ongoing challenges with staffing shortages and retention have brought a real focus to the importance of effective and repeatable training programs,” says Michael Newcome, VP of Sales at JLS Automation, which offers robotic packaging solutions.
Recently, JLS Automation demonstrated an AI inspection system that could be integrated into its primary loading system to identify appropriate cuts of protein, relying on an inspection system using visible light coupled with human-trained AI.
The Smart Manufacturing Report points to these recurring workforce pain points for food companies:
- Managing a shortage of skilled workers.
- The need to “train employees on new processes at speed requires modern approaches.”
“It's important to involve operators early in the process, explaining the benefits and addressing their concerns,” says Lee Coffey, global strategic marketing manager, consumer packaged goods at Rockwell Automation. “By understanding these concerns, organizations can create a supportive and encouraging atmosphere that helps embrace change.”
Technology Inroads in Processing and Packaging Operations
For years, food processing divisions within companies have received the first wave of plant modernization efforts or smart assets. This could mean capital investment for industrial networking buildouts for processing to optimize communication between the plant floor and the executive level and drive out costs.
That meant quicker wins for the processing, and older equipment and networking for packaging divisions within food companies.
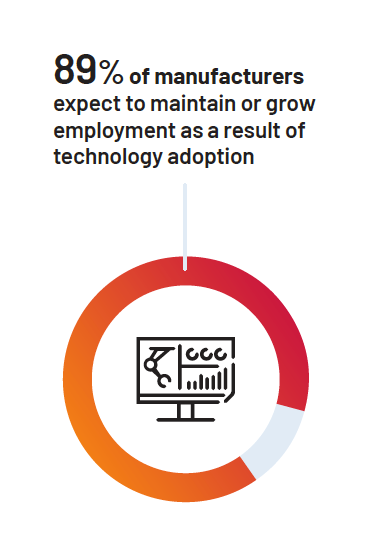
In 2013, Chobani won Food Engineering's Plant of the Year for its buildout of a new Idaho plant that added more than 29 PLCs throughout the plant and a process PLC, all connected together by a Hirschmann industrial Ethernet and more than 25,000 I/O points. Plus, an industrial Ethernet network allowed operators to follow processes at any location through Rockwell’s FactoryTalk View SE software and Wonderware’s Data Historian.
The first phase of the modernization was on the processing side. Years later, Chobani added Inductive Automation’s Ignition platform as well as Supervisory Control and Data Acquisition (SCADA) to the packaging business, which was important as process control data, such as process tanks, were able to communicate to the enterprise level and sync with real-time packaging operations information.
Moreover, management sent alerts to plant teams if production output fell below certain levels.
Augmented Reality and Digital Twins for Troubleshooting
As equipment and networking investments move into packaging, original equipment manufacturers (OEMs) partner with technology providers to aid operators and food companies troubleshoot production issues.
One example is Harpak-ULMA Packaging and its partnership with PTC, which offers a range of information solutions to troubleshoot plant floor lines. PTC offers Vuforia Expert Capture, an AR platform, and ThingWorx’s industrial connectivity technology solution. These two tools combine AR and with real-time video communications to help plant workers connect to a third-party expert—OEM—to solve troubleshooting issues.
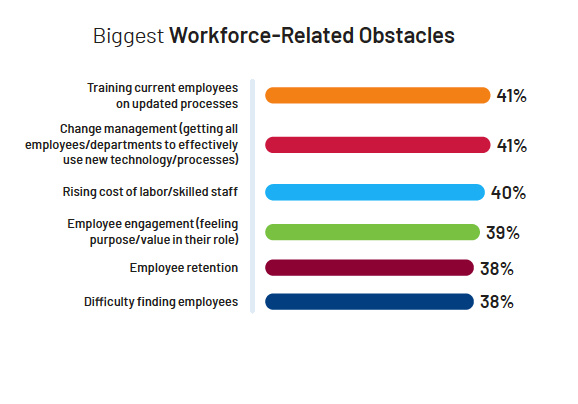
Harpak-ULMA Packaging offers a range of equipment for the food industry. The company offers a range of equipment including tray sealing and forming, thermoform machines, flow wrap machines, overwrap and packaging automation. For its equipment’s automation, Harpak-ULMA uses Rockwell Automation control platforms with Kepware industrial networking.
“We chose PTC’s Vuforia suite because we have a variety of customers and they need flexibility to access their data regardless of their organization setup,” says Alexander Ouellet, innovation engineer at Harpak-ULMA Packaging.
Maple Leaf Foods, based in Ontario, Canada, is a top-tier food manufacturer that produces prepared meats and poultry, and recently employed a pilot program around AR to improve operations. For the pilot project, Maple Leaf recruited Harpak-ULMA Packaging, Rockwell Automation and PTC.
For the project, Maple Leaf was looking to meet an 80% overall equipment effectiveness (OEE) or greater. Actions impacting OEE include upskilling staff through better training, fewer/shorter downtime events, increased first-pass quality and faster mean time to repair (MTTR).
The pilot included the entire library of PTC AR applications and created its own machine-based AR experiences. AR offers visually based work instructions and training, and on-demand expert guidance.
The project quickly demonstrated the value of AR in a packaging line. For example, the OEE application delivers self-diagnosing machine reports identifying downtime and high-priority action items by shift.
Using remote connectivity, the Harpak-ULMA team monitors these reports daily, identifies high-frequency stoppages and then builds remediation routines using Vuforia. With this application, OEM experts capture and transform step-by-step procedures into AR-based work instructions operators can access in real-time.
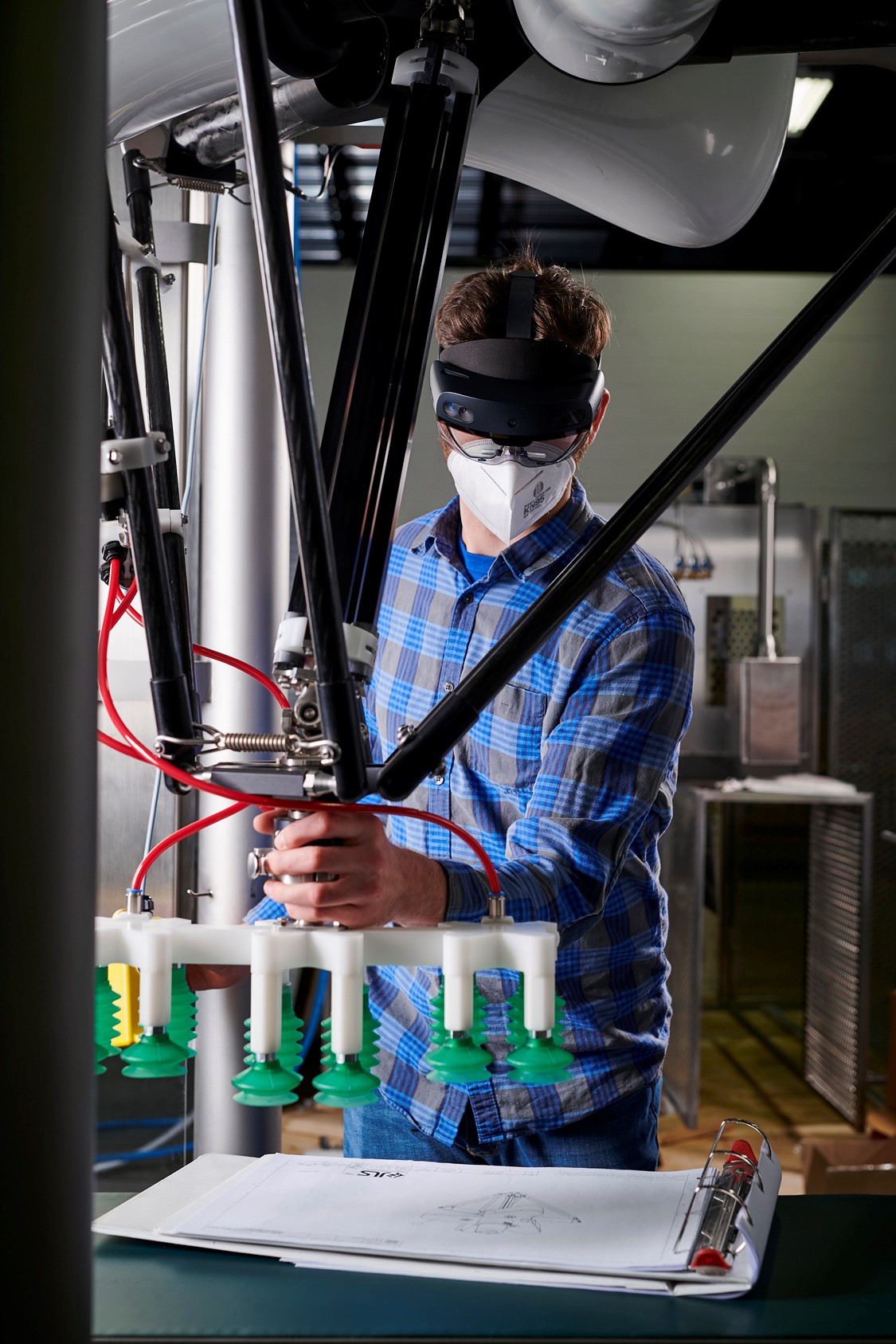
In a recent webinar, Ouellet provided a demo of a thermoforming machine and discussed operator challenges in troubleshooting and machine recognition. Ouellet says once a machine is recognized by area targeting, it can then pull in data streaming from the machine, and this can include a serial number, OEE, machine status and operator.
“In the field, this gives the operator a lot of information about how that machine is running in real-time and they don’t have to log in to a particular screen on an HMI,” says Ouellet. “This data can be checked against dashboards, too.”
Also, for increased workforce utility, Ouelett stressed the importance of why digital twin technology is part of the Harpak-ULMA offering. Digital twins also allow personnel to virtually see inside an operating machine to identify the location and condition of components without stopping production.
During the demo, Ouelett pointed out that a digital twin can create alerts, which can be communicated to an operator who doesn’t have years of experience on this machine. Digital wayfinding technology will guide an operator to the correct area of the machine and show which gauge, for example, is malfunctioning even though there are many in the machine section.
Plant Floors are a Changin’
As food and beverage plants modernize, more companies will give digital twin technology, AR- and AI- enabled solutions a longer look. For years, the goal of plant managers was to use automation technology to optimize operations and lower costs, and now next-generation technology is doing a similar thing: helping operators optimize production and deliver higher OEE.
“From a support perspective, whether it’s AR, event-based camera systems or live video from a cell phone, the use of camera-based technologies helps our customer service team view, identify and resolve an issue,” says Newcome.
Looking for a reprint of this article?
From high-res PDFs to custom plaques, order your copy today!