Labor
Food & beverage companies cope with labor shortages
Processors look for solutions to labor challenges

Running a food plant without employees isn’t possible, so food and beverage processors are exploring a number of different solutions to ongoing staffing shortages and labor challenges.
Photo credit: Getty Images/DedMityay
Labor shortages in the food and beverage industry are nothing new, but add in a global pandemic and it’s safe to say that both the industry itself—and those who help companies design, renovate and become more efficient—have had to think outside the box.
Food and beverage processors are turning to a number of solutions to help solve this challenge, but there’s no easy solution. It’s a combination of design, employment and operating decisions that hopefully add up to meeting staffing needs.
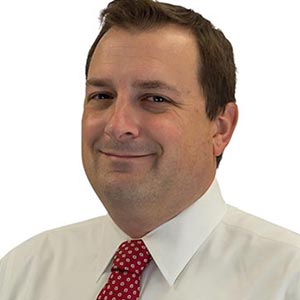
“We have heard about labor shortage concerns from clients dating back to the Great Recession. Like many other industries, workers that were laid off during this period did not return to their jobs as the economy recovered.”
–Dan Crist,
vice president of operations, A M King
“We have heard about labor shortage concerns from clients dating back to the Great Recession [in 2008],” says Dan Crist, vice president of operations for A M King. “Like many other industries, workers that were laid off during this period did not return to their jobs as the economy recovered. This has contributed to increased focus on designing and constructing more efficient facilities.”
Walter Nimocks, CEO and founder of Just Made Juice, says while his company doesn’t currently have a labor shortage, they are hoping to expand in 2021—and they are hoping to do that without adding staff or another shift. How? Through efficiency via capital investment.
Just Made Juice is looking at about $200,000 in capital investments to improve efficiency while running only one shift – and keeping its staff at around 14 employees.
“We’re looking to double production without increasing our headcount,” Nimocks says. “It’ll add complexity, for sure.”
Just Made Juice is planning to get more mixing tanks to cut the time between flavor or SKU changeovers and also invest in pressing equipment. They are also looking to invest in systems to get bottles filled and labeled faster.
“We need to address bottlenecks,” he says, echoing a common theme.
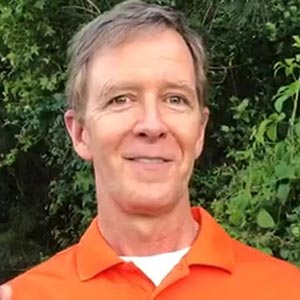
“We’re looking to double production without increasing our headcount. It’ll add complexity, for sure.”
–Walter Nimocks,
founder and CEO, Just Made Juice
Workflow improvements
Many food and beverage companies—and the companies that help them improve efficiency and output—say that improving workflow is crucial to addressing labor shortages.
“It’s all about how do you do more with less people and finding that way,” says Roy Johnson, business strategist with Black and Veatch.
Finding that balance is Tammi McAllister’s specialty as the business unit manager for the food and beverage division of CRB. Her team looks at how people and materials flow in and out of plants to try to find ways to make it more efficient.
“[We] really look at how to optimize layouts and minimize the number of people,” McAllister says.
Because of ongoing labor shortage issues, McAllister says CRB works to help companies do more work without bringing on more people. While many companies have been using temporary workers to address labor shortages, McAllister says these workers often aren’t as knowledgeable or reliable as full-time direct hires.
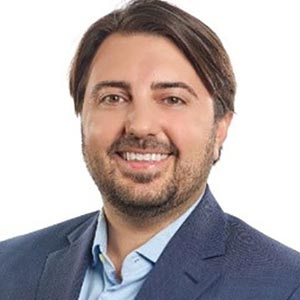
“It’s all about how do you do more with less people and finding that way.”
–Roy Johnson,
business strategist, Black & Veatch
Jasmine Sutherland, president of Texas Food Services, knows this first-hand. For years, her company avoided staffing struggles by working with local nonprofit and faith-based organizations to employ immigrants in a temporary capacity. However, the COVID-19 pandemic has slowed immigration so the company has had to get creative as staffing issues popped up and threatened to slow production.
“We decided to offer employees overtime,” she says. “And it has been very well received; it’s really popular. We’re also pretty much always hiring pretty aggressively.”
She says in a perfect world, Texas Food Services would hire direct employees who would stay on for years and become a part of the family. That is the ultimate goal, Sutherland says.
A now and future challenge
Food and beverage manufacturers need to address labor shortages today, but many say they don’t foresee labor shortages going away anytime soon. They are looking at whether they need one employee to do a task or multiple employees; also, they look at adding or taking away shifts, where equipment is placed and the layout of their processing or packing lines.
In a word: Efficiency is key.
Streamlining work and reconfiguring workspaces can make a huge difference, so design firms like CRB recommend optimizing what you have before building new or looking to expand staffing.
For example, a producer of packaged nutritional products that McAllister worked with spent about $100,000 on an operational study that managed to save $3 million a year. It was a simple solution that ended up with big rewards.
But a company has to be willing to invest in an audit to assess their systems and employees, because over time, people can get set in their ways and not want to look at new approaches or solutions.
“It can become a real spaghetti mess,” she says, “because you keep adding products without looking at how to work more efficiently.”
If a food and beverage company has maxed out staffing and efficiency changes, there is another option: automation. This is a costly option and it also comes with its own set of challenges and hurdles.
Automation isn’t a fit for all companies, says David Ziskind, director of engineering at Black and Veatch. Some industries like meat processing might never be a good fit. And bringing in automation drives the need for more skilled labor, so that’s a counterpoint to the unskilled labor shortage.
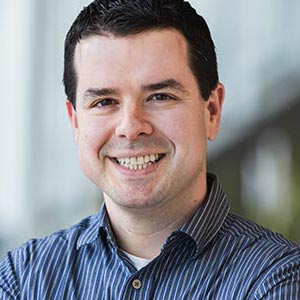
“Focusing on automation in areas where humans are less comfortable is a good place to start.”
–David Ziskind,
director of engineering, Black & Veatch
You still need staff, but now that staff has to be already trained and able to manage computer networks and machines that are complex and need to be regularly serviced and brought back online. Generally, you can’t just train people on these skills; employees need education and possibly advanced degrees.
But for some food and beverage manufacturers that employ people who work in environments that aren’t the friendliest—for example, if they involve extreme cold or extreme heat—automation can address not only labor shortages but employee satisfaction.
“Focusing on automation in areas where humans are less comfortable is a good place to start,” Ziskind says.
McAllister says her clients evaluate automation, especially when they are at a place where they can’t add more workers due to labor shortages or capacity issues.
“More automation equals less people,” she says. “So, in areas where it’s hard to find labor, it’s a real option. It can be costly, though. It’s a little more of a challenge.”
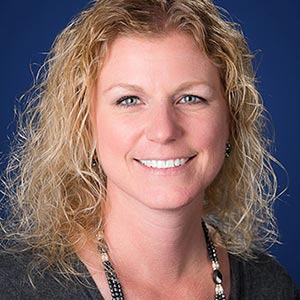
“Certain people want to work at a facility that is new and not dated.”
–Tammi McAllister,
business unit manager, food and beverage division, CRB
Pandemic complications
Another challenge that’s impacted the food and beverage industry this year—and one that will likely be around for years to come—is the COVID-19 pandemic.
Many food and beverage manufacturers say it will likely permanently change how they do business. Not only because the effects of the pandemic are likely to impact the labor force for years to come, but also because there will be an ongoing need to isolate and remove employees who are ill, as well as keeping people apart—aka social distancing—to ensure there isn’t a need for work stoppages due to exposures.
The food and beverage industry, and the industries that support them, need to adapt so that labor shortages don’t result in work stoppages.
“While there are economies of scale pushing toward larger central production, we have seen shortages when one of those facilities has an outbreak and closes,” says John Koury, architect with A M King. “A less centralized, more regional based, supportive supply network can adjust and cover more easily if an outbreak occurs. We’ve seen some industries flourish while others struggle in this pandemic. We do not know when the next pandemic will happen, but lessons learned during this one can help a producer be able to flourish and adapt.”
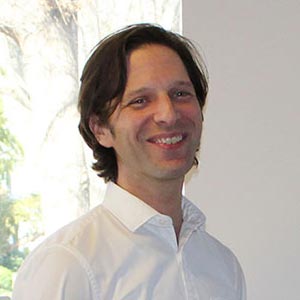
“While there are economies of scale pushing toward larger central production, we have seen shortages when one of those facilities has an outbreak and closes.”
–John Koury,
architect, A M King
Small changes, big solutions
Another way food and beverage manufacturers are adapting is by taking a softer, and often more subtle approach.
Small changes can help food and beverage manufacturers attract and retain talent—especially in the small towns and rural areas where factory work can be a hard sell to the potential labor pool.
“For a lot of companies, COVID has really forced their hand,” says Johnson. “They’ve had to look at technology solutions and other efficiency solutions. It’s a very interesting time.”
Food and beverage manufacturers say that potential workers don’t want to work in factories, because there is the stereotype that they are loud, dirty and dangerous places.
Adding things like natural light or undertaking renovations that create cleaner and quieter working areas, access to break rooms, restrooms and locker rooms can all make a difference. Newer or remodeled facilities can also be a draw.
“Certain people want to work at a facility that is new and not dated,” McAllister says.
Texas Food Services hasn’t done any facility changes; however, Sutherland says in recent months, they’ve improved training and communication to become even more efficient.
“We found that we run faster when everyone understands and is on the same page,” she says.
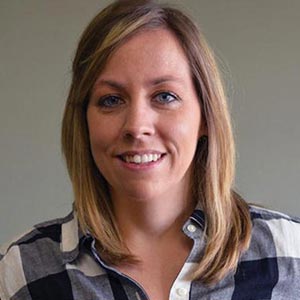
“We found that we run faster when everyone understands and is on the same page.”
–Jasmine Sutherland,
president, Texas Food Solutions
And having management and employees on the same page is critical to not only addressing labor shortages but maintaining productivity. These changes and adaptations send a clear message to employees that a company is committed to staying in the community and providing quality jobs for those who live there for years to come.
Oftentimes, a food and beverage manufacturer can address labor shortages by working to improve public relations externally and morale internally. It shows the company is invested in the community and its employees.
“We know that it’s critical to have a good team,” says Nimocks. “But you have to stay competitive.”
For more information:
A M King, amkinggroup.com
Black & Veatch, www.bv.com
CRB, www.crbgroup.com/food-beverage
Just Made Juice, www.justmade.com
Texas Food Solutions, texasfoodsolutions.com
Looking for a reprint of this article?
From high-res PDFs to custom plaques, order your copy today!