AI: Behind-the-Scene Partner in Process Applications
Rather than apply AI/ML in one big fell swoop, why not choose applications that use AI to make them more efficient and build from there?

Artificial intelligence built into vision systems can guide decisions in robotics in pick-and-place and filling applications, while at the same time performing quality checks on products. Image courtesy of Festo North America
In an editorial piece on the ARC Advisory Group website, Director of Research Marianne D’Aquila asks, “Why do artificial intelligence implementations fail?” She answers by saying that “implementing AI in manufacturing can be challenging, if not daunting, as it requires an understanding of business objectives and the integration of AI with existing processes and systems.”
D’Aquila goes on to include that “it is typically overwhelming to determine an effective starting point for any digital transformation project, including implementing AI.” She says that without clear ideas on how to develop strong analytical digital competencies, companies often experience the collapse of AI pilots and projects, leading to the internal perception that these projects are a wasted investment.1
Could some of these failures have resulted from biting off more than can be chewed? For example, AI doesn’t have to be an all-at-once, doomed-to-fail implementation, spanning every plant operation from incoming ingredients to processing, to packaging and then out the door—which may not yield expected results. Perhaps a worthwhile alternative is to look for applications that feature embedded AI, for example, monitoring energy usage, visually inspecting product quality or predicting machine failure. Software and automation vendors are already embedding AI into these applications, and they have been shown to work.
This concept is similar to some of the new AI-based graphics software that works as an independent application or as a plug-in to Adobe Photoshop or Affinity Photo. The AI-based plug-ins I currently use let me get the job done more quickly, accurately and efficiently—and I don’t have to worry about AI programming or even modifying the host application. The plug-in application developer has already done the heavy lifting. I’ve found that the AI-based software just works better than its earlier non-AI-based software counterparts.
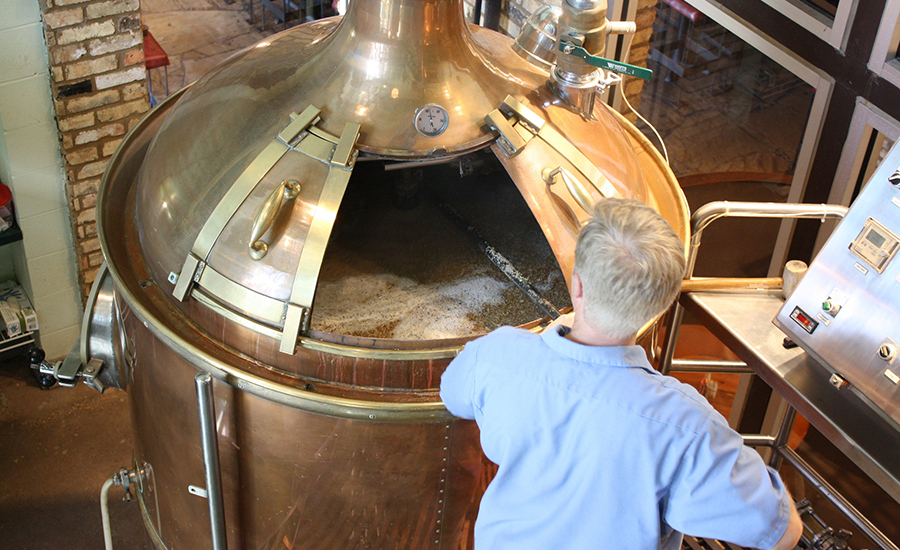
Ask the AI for its “Opinion”
So, I thought I’d ask the AI-based ChatGPT, “Will artificial intelligence become part of software applications such that users aren’t aware that the application uses AI?” After all, it seems only natural to ask an AI system what it “thinks” on the subject.
ChatGPT responded, “Yes, it’s very likely that artificial intelligence will become an integral part of software applications in such a way that users may not be aware of its use. This is because AI has the potential to enhance and automate various tasks in software applications, making them more efficient and effective.
“For instance, AI can be used in applications to improve user interfaces and experiences, provide personalized recommendations, and automate routine tasks. As these capabilities become more integrated into software applications, users may not even be aware that AI is being used.
“In fact, this is already happening in many applications that use AI behind the scenes, such as virtual assistants, chatbots and recommendation engines. These applications are using AI to improve their functionality without making it obvious to the user that they are interacting with an AI system.”
So, why not take advantage of applications whose developers have embedded AI to make parts of your plant run more efficiently and smoothly?
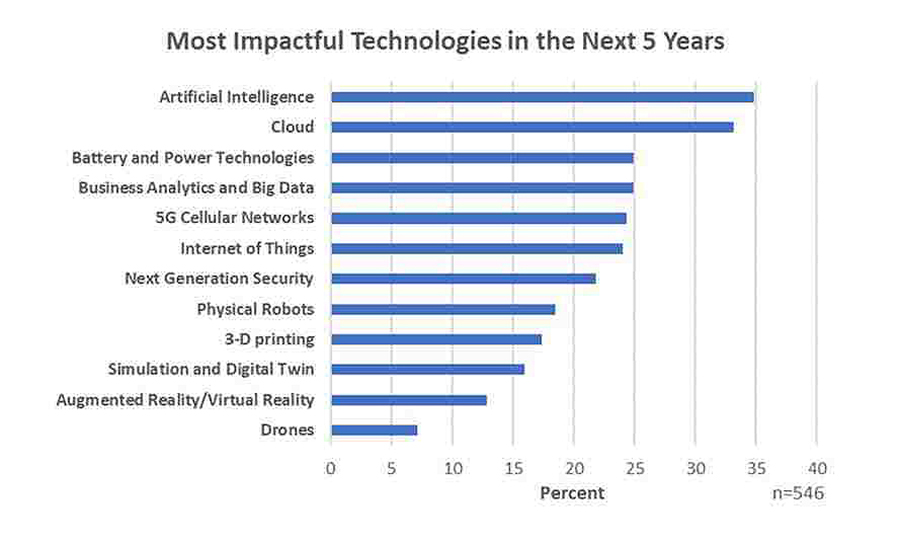
AI and Process Applications…and Beyond
When asked, ARC Advisory Group’s D’Aquila named four general categories for AI applications, with the fourth being one you may not have considered, but is equally important.
- Quality control —Use AI and machine learning to monitor and analyze data from sensors and cameras throughout the production process to detect potential quality issues early and improve product quality.
- Predictive maintenance for early detection of equipment failure, therefore, schedule maintenance before issues occur. This minimizes downtime and improves overall plant efficiency.
- Digital twin programs powered by AI are being used to simulate, optimize and validate manufacturing processes before being implemented in the real world. Digital transformation can become part of a competitive strategy in a market with fickle customer demand and razor thin margins.
- Workforce optimization —Many experts and operational leaders predict and fear automation and advanced technologies will rapidly displace factory jobs. However, leading factories are actually understanding and investing significantly in people. Leaders understand the lifecycle of any one worker is shifting and is pushing factories to compete with many other entry level jobs where people are hiking their pay per hour. The result is the factory floor worker is coming and going faster than they ever did before. Today’s workers are shifting jobs more frequently, which is reducing the lifecycle of an employee. This is driving the need for operational leaders to be more focused on providing decision making tools for the workforce. In other words, workers need to understand immediately where to turn for answers. This is vastly different from providing classes of educational training. Recognizing increasing complexities on the shop floor and making technology more accessible to enable people to collaborate with the experts and intelligent software (which can guide them on their next steps) are truly transformative measures unlocking significant value and productivity boosts.
“Food and beverage processors are increasingly looking for AI-based solutions to improve their sales and operations planning,” says John Dwinell, president, Peak Technologies/Peak Analytics. There is a growing awareness of the potential benefits of AI in the food and beverage industry, and many processors are actively seeking out AI-based solutions to help optimize their operations. However, there may still be some skepticism or uncertainty around AI’s effectiveness and applicability in certain areas.
AI can be intimidating at times, and that’s why it’s important to partner with someone who understands your business and has the ability to democratize the new technology adoption and hardwire it to critical business processes and KPIs, adds Dwinell.
Festo North America manufactures smart devices for pneumatic and electric automation that are used to control all sorts of process equipment, which are rich in data and can be used for data analytics. “We have gateways (hardware and software) that extract data models from third-party hardware/sources and our smart devices and utilize MQTT and Node-RED for contextualizing data and making it available on an MQTT broker for consumption,” says Frank Latino, product management electric automation. “We have an AI/ML software tool to analyze the data for predictive maintenance, quality, and sustainability applications.”
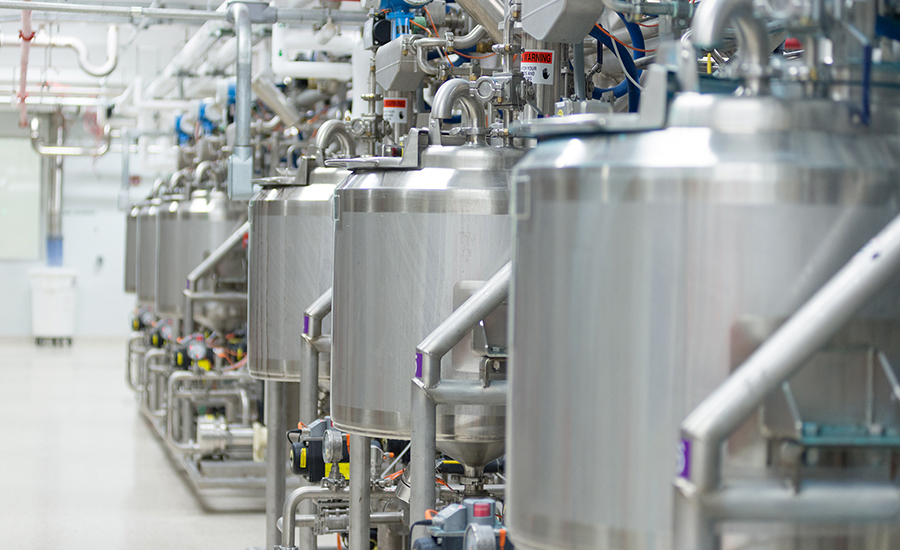
Improving OEE by Monitoring the Equipment
“Our software solution, Festo AX, is independent from any hardware manufacturers, even from Festo components,” says Lea Bayer, digital sales expert. “It can analyze offline as well as real-time data and helps to improve production’s OEE.”
“In general, we would apply AI/ML to food or beverage applications to predict mechanical failure of equipment, quality losses and unusual energy consumption,” says Latino. “For example, poultry processing has mechanics in every step of the process. AI is used to detect process disturbances in pneumatic cylinders. For filling applications, AI is used to detect changes in nozzles and valves for controlling liquid, ice cream, etc.”
“Process data collected through IIoT can be aggregated in order to build key performance indicators (KPIs),” says Gian Paolo De Salvo, industry manager for manufacturing operations management in process industry, Siemens Digital Industries Software. OEE KPIs will show machine downtimes and the reason for each failure occurrence, timespans when machines were operating at low speed and the percentage of scrap. Furthermore, it is crucial to provide the production context of these process issues, i.e., which type of packaging a packer machine was handling at a point in time or which product the filler was filling into consumer units. “Our manufacturing operations management (MOM) solution can deliver all of this visibility and supports to dig into the root cause analysis of the process and production issues,” adds Di Salvo.
AI can play a key role in analyzing OEE KPIs to support continuous improvement, for example, setting up automated alerts to notify operators about deviations in equipment behavior or product scrap percentage and identifying behaviors and correlations among different domains, such as process, production and quality.
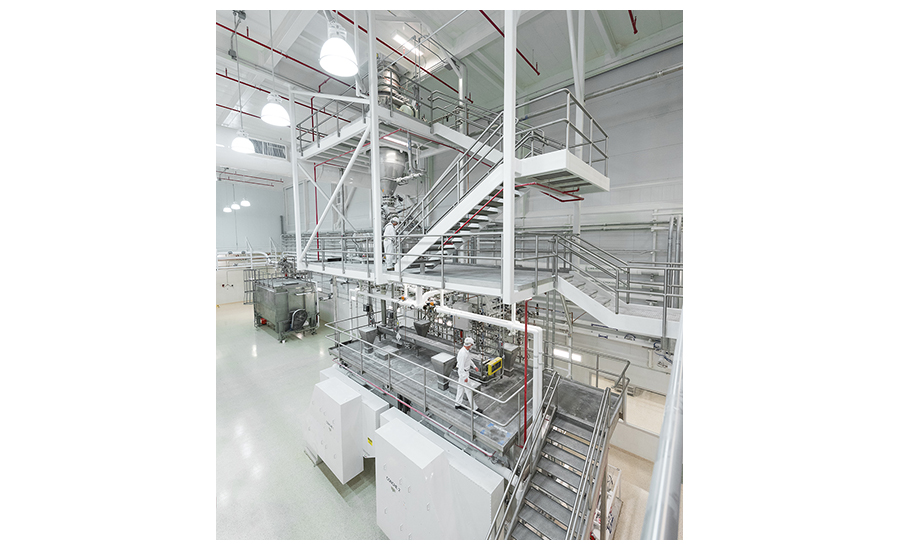
Quality is the Emphasis
Gray Solutions’ focus has been on advanced vision systems, mostly in the area of quality inspections, according to Greg Powers, VP of cool stuff, Gray Solutions, a Control System Integrators Association member. “Visual inspection automation (VIA) software goes beyond the capabilities of traditional machine vision in detecting anomalies and defects, even when products have natural variations. Using proven vision AI technology, manufacturers can scale production, reduce waste and adapt to workforce changes while achieving even higher levels of quality control. To add to this we are also using vision systems to identify opportunities to change control parameters—like the speed of the belt or oven temperature based on food being over or undercooked.
“Most of the areas we have been focused on are in processing,” adds Powers. “Vision systems with AI/ML have already been established in packing areas. The use of this same technology in processing is becoming more popular by eliminating much more waste and scrap. Most of the applications we have been focused on are quality-oriented, which would include sorting, grading and inspections. These same solutions are used to predict when downtime could occur based on past trends using advanced data algorithms.”
“AI can help in suggesting corrective actions to take in order to avoid scrap of an entire production batch,” says Kevin Hoorne, industry manager CP&R for digital manufacturing, Siemens Digital Industries Software. Based upon the quality parameter results for a batch coming from the lab, AI can bring efficiency and prevent lost batches by suggesting the corrective action to take to bring the quality parameter results of that batch back within spec. In the same way, even for good quality batches with all quality parameters within spec, AI can analyze contextualized data coming from the shopfloor and link this to quality parameters to optimize machine parameters for future production. That way, each batch produced can come closer to the golden batch until this finally becomes the standard.
“Similarly, at Siemens we believe true quality can only be realized by connecting early idea generation with final realization in manufacturing,” adds Hoorne. “This is where we have also been working on using AI during early product development in food and beverage. When working with formulated products, the action to take to optimize a formula toward less quantifiable parameters such as tastiness and smoothness is not that straightforward. This is where we have set up successful use cases leveraging upon AI to make that possible in an efficient way, saving time and money and allowing companies to be first to market with an improved product.”
Maintaining quality through high throughput can be a challenge, says Alexander Epple, head of industry IIoT industry solutions, Siemens Digital Industries Software. “We support this with our solution Quality Prediction Hub which utilizes machine learning on machine and process data to predict quality issues along the packaging process to automate quality inspection processes, detect issues as early as possible and provide information indicating drivers of quality issues, which can be utilized by operators to optimize line settings.”
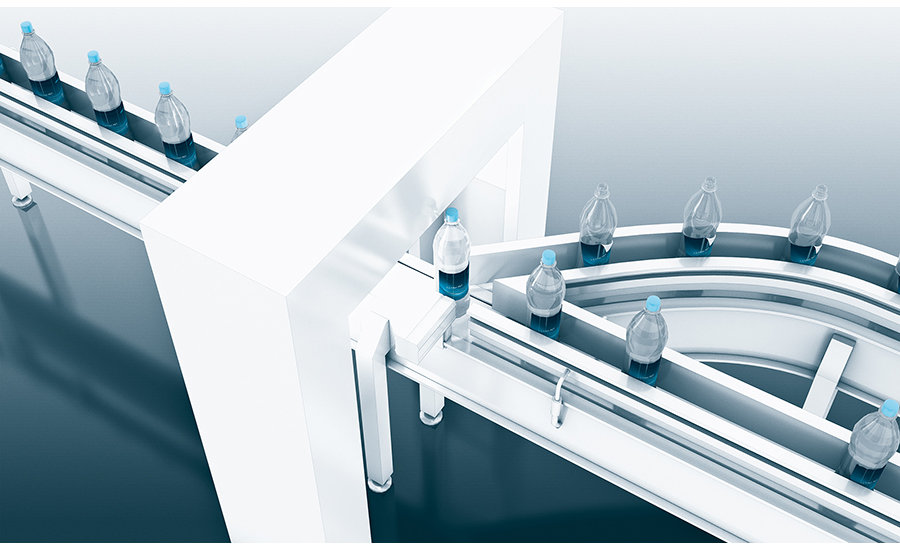
AI Expectations
Food processors expect to improve OEE, and AI/ML can help in these applications. “The main motivation of using machine learning/AI software is to improve production processes and OEE,” says Festo’s Bayer. “Our customers often have a pain point in their production, and no conventional solutions such as condition monitoring can help. They expect, besides failure detection, a solution that can easily and seamlessly integrate into their existing architecture and processes. Festo AX should be seen as part of their daily work.”
“We are expecting more built-in capabilities from equipment providers,” says Gray’s Powers. “Smart machines that can make adjustments based on data being captured downstream—using more advanced algorithms to make these adjustments. We are doing this now, but getting the correct data from equipment providers and what parameters we can adjust is always a challenge.”
Why a challenge? “They (equipment providers) are hesitant about providing this [data] to manufacturing companies with the risk of losing some control over their solutions and competitive advantage (IP),” says Powers. “The food processing companies that have been able to get through these hurdles have seen reduction in waste, improved quality and less downtime on equipment.”
Where AI can help a processor depends on setting priorities. “Focus areas will always depend on customers’ most pressing challenges, which may differ significantly between companies,” says Siemens’ Epple. “For instance, predictive maintenance may be more important to companies with older equipment than those which have brand new machinery. Likewise, the importance of predicting and avoiding electricity consumption peaks will differ with energy intensity, local energy cost, etc. Hence, we provide a portfolio of predictive solutions for the most common challenges and easy-to-use tools for customers to detect anomalies or make predictions based on their production data.”
How much should a processor expect to spend on AI-based tools? “From a product perspective, it depends heavily on the brand and the market positioning,” says Hoorne. “It’s like a quote from an AI vendor that stated, ‘We have a solution for those companies to whom it’s worth millions being first to market instead of being second.’ And for some CPG manufacturers and the innovative products they bring to market, this is the case. For others, however, being an early second in the market is more than good enough.”
Thus, it is incumbent on the processor to determine the focus areas where AI could bring value, adds Hoorne.
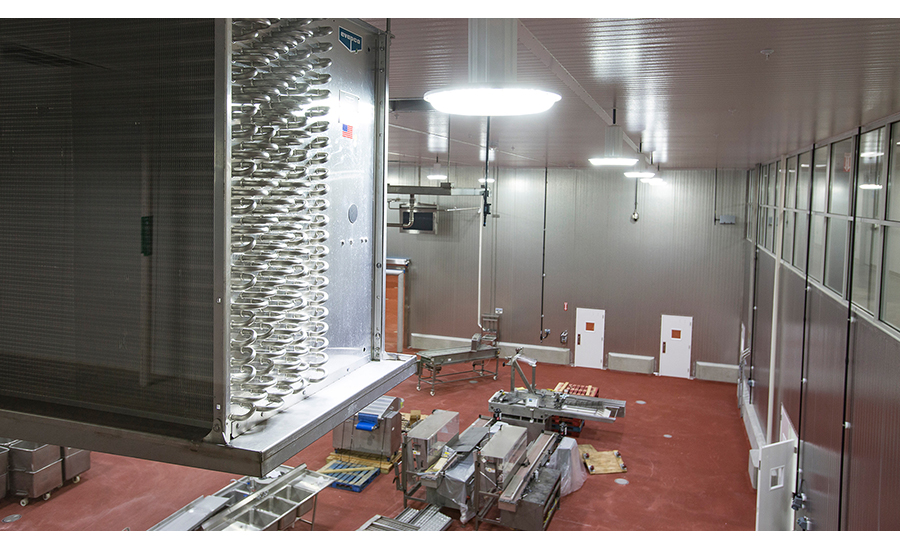
Expectations Realized but Patience is a Virtue
Meeting expectations does require patience as AI has to “learn” what is expected of it—so to speak. Sometimes manufacturers are expecting to see immediate gains and benefits on these solutions, but this isn’t always the case, says Gray’s Powers.
“AI/ML needs large amounts of data to analyze. This takes time to collect and identify these initial patterns so the algorithms can be updated. Eventually, the system can be tuned in and the benefits come quickly and little or no additional time is needed in the algorithms. Most of the gains are in waste reduction, less downtime, but even in labor,” says Powers.
“Much of the work that has been done in AI/ML is to replace something the worker has been doing, especially in quality inspections,” adds Powers. “Many times, the system picked more defects than was expected, allowing for an improvement in the overall quality of the product during the manufacturing process. It is very important to understand the data that needs to be collected and begin to collect it. Once data has been collected, use this to do some initial learning. This will save time during the overall project.”
In an OEE application run by Festo, improvement was recognized. “Our solution reduced unplanned downtimes, increased availability and reduced rework and waste, for example,” says Latino. “It may take a few iterations to improve a data model to reduce false positives. This is why using an experienced team adds value. Their experience helps to get the model right as soon as possible in the commissioning phase.”
The Future of AI
Has AI reached the toddler stage, or is it walking or running? “I see AI becoming easier to deploy by introducing it directly into the devices controlling the processes,” says Latino.
“We have proven our software over many years by helping customers to improve production processes and OEE,” says Festo’s Bayer. “We work with a lot of companies in the food industry and provide standardized AI solutions, for example, palletizers or filling machines. I can confidently say that we passed the toddler stage with our software solution long ago.”
“Machine vision tasks now require highly complex analysis beyond the scope of traditional vision systems,” says Gray’s Powers. “As a result, the demand for high-quality inspection tasks in the food manufacturing space has grown exponentially. The increasing need to ensure the quality of manufactured food products has exceeded the scope of traditional vision system techniques, which were widely incapable of performing human-like inspection tasks. Vision systems have made great strides in AI, and with more companies supplying AI tools, the market has exploded. As we implement more technology in other areas like predictive maintenance, AI becomes more tangible. AI companies are ramping up in this area and will explode in the next 10 years.”
ARC Advisory Group’s D’Aquila lists three growth areas for AI:
- More automated production lines with AI powered robots working alongside human workers to automate various stages of the food production process, improving efficiency and reducing labor costs.
- More sophisticated AI driven process optimization where AI steps in deeper to analyze production data to identify areas where processes can be optimized even greater for efficiency and cost savings. The business goal is reduced production costs and faster production times.
- An increased move beyond predictive maintenance to prescriptive maintenance. Predictive maintenance involves monitoring equipment and analyzing data to detect changes that may indicate an impending failure. Prescriptive maintenance, on the other hand, is a more advanced use of AI to analyze data from the sensors and equipment to recommend specific actions that should be taken to optimize maintenance. This approach goes beyond just predicting but provides recommendations on what should be to done to maintain the optimal performance including the timing of maintenance and parts replacement.
AI and the Cloud
“Patterns and algorithms can reside in the cloud and then be pushed down to a receiving system on premises that carries out the actions or provides more operational algorithms,” says Powers. “Some real infrastructure challenges may exist in getting the data to the cloud. As cybersecurity is a big concern with many companies, getting data out of the plants to the cloud becomes even harder. IT groups are hesitant to opening port channels for data to be collected from equipment.”
“Many in the processing space struggle with security concerns of the cloud,” adds D’Aquila. “Ironically, securing the cloud rises to the top as the most important challenge when thinking about digital transformation on the factory floor. ARC’s primary research conversations have revealed those who have made the move to the cloud actually feel more secure.
“They have also cited scalability as a benefit from moving to the cloud, allowing them to scale up or down the processing power and storage as needed without having to invest in expensive hardware on premises,” says D’Aquila. “Cloud can be much more cost-effective over time and does not require constant maintenance on site.”
“In general, cloud solutions can be updated more easily from a vendor, so the latest versions are always available to the user,” says Latino. “Hosting services generally provide the latest protection for security. Running in real time depends on the application. If needed, then running on an edge controller is possible. But software may be flexible enough to do anomaly detection on the edge, and model definition, database, etc. can be in the cloud where more resources (i.e. memory) are available.”
References/Resources
[1] “Why Do Artificial Intelligence Implementations Fail?” Marianne D’Aquila, ARC Advisory Group, www.arcweb.com, accessed 1 May 2023
“Artificial intelligence/machine learning reduces mistakes and waste, FE, 9 May 2022
“AI helps control greenhouse automation systems,” Engineering R&D, FE, 3 June 2022
“AI/ML-based real-time sensing techniques turn art of winemaking into exact science,” Engineering R&D, FE, 12 July 2022
“Getting Consistent Results from Fermentation,” FE, 10 September 2021
“Finding new AI-based methods to boost productivity requires digital data,” FE, 13 February 2020
Looking for a reprint of this article?
From high-res PDFs to custom plaques, order your copy today!