State of Food Manufacturing
2020 State of Food Manufacturing Survey
Annual industry survey reveals challenges food and beverage processors are facing

The COVID-19 pandemic dominates the conversation this year among food and beverage processors surveyed by Food Engineering for the 2020 State of Food Manufacturing.
Photo courtesy of Getty Images

More than half of respondents expect their throughput to increase over the next year, but almost a quarter expect it to go down due to a COVID-19 driven downturn in the foodservice market. (View full-size chart.)

Almost two-thirds of respondents expect to purchase process control hardware or software, which is in line with responses in a normal year. (View full-size chart.)

One of the most common responses to a question about structural changes was supply chain changes, as processors found out where the weak links were when the COVID-19 pandemic hit. (View full-size chart.)

Robotics are more common in food and beverage processing every year, but a number of respondents expect them to play a bigger role as COVID-19 reshapes the industry
Photo courtesy of ABB





Each year, Food Engineering surveys its readership to find out what challenges processors are facing, how they’re adapting and what they’re expecting for the future.
It will come as no surprise that the COVID-19 pandemic is dominating the conversation this year. It’s disrupted normal routines, planning, forecasting and even life in general. It’s created a multitude of challenges for the food and beverage industry, including dealing with a surge in demand for retail products while foodservice demand evaporates; keeping employees safe and protected in environments where social distancing is often impossible; maintaining construction schedules with project managers under travel bans; and hiring, training and retaining workers to meet all of these challenges in an environment where conditions are constantly changing.
All of those things are top of mind for food and beverage processors, which face challenges even under normal circumstance. Consider this: There’s a question at the end of the survey where respondents are asked for their thoughts on what is happening in the industry and what they see coming in the future. Respondents are granted anonymity to speak freely, and there’s one response in particular from a wave of COVID-19 answers that sticks out:
“COVID is more than a trend; it's a tidal wave that's going to dictate A LOT about how the next five years pan out.”
Layered on top of all of the COVID-related demands processors face on the production side is how the crisis is shaking up consumer demand. The trend toward single-serving, grab-and-go-style food and beverages has suddenly reversed as consumers are working from home, eating family dinners in the evenings instead of having multiple events on the calendar, and buying more frozen and nonperishable foods.
“Generally speaking, people have been panic-buying frozen foods because they last longer and won’t necessitate weekly shopping trips,” says Rigo Viezca, global head of fast-moving consumer goods (FMCG) solutions at Signals Analytics. The frozen vegetable aisle in particular has undergone a sort of resurgence: being able to buy and store healthy foods, including greens, suddenly seems like a luxury.
It is through that lens that the State of Food Manufacturing must be viewed: Constant changes, huge swings in demand or shifts in consumer behavior, employee safety, and a general uncertainty about what comes next.
Throughput and consumer demand
One of the staple questions of the survey is what processors expect in terms of throughput. It’s a good shorthand for identifying what is happening with customer demand by giving a general sense of what processors are planning for over the next year.
In the 2019 survey, 65% of respondents said they expected throughput to increase, 31% said they expected it to stay the same and only 4% said they expected a decrease. This year, only 55% of respondents say they expect an increase and 22% say they expect throughput to stay the same. The most common ranges of expected increases were 6-10% (28% of respondents) and 11-15% (22% of respondents).
The number of respondents who say they expect a decrease in throughput spiked to 23%, driven by drastic declines in foodservice markets. That’s not surprising after several months of shutdowns or limited service for restaurants, schools, colleges and universities, convention centers, stadiums, arenas, movie theaters, and basically any other foodservice market. It’s a big hit for processors and facilities that serve those markets, with 36% of respondents saying they expect a decrease of more than 25%.
One processor that had to face those challenges head-on is Before the Butcher, a plant-based meat manufacturer. Founder and president Danny O’Malley says that at the end of 2019, the company was just establishing a foothold in the retail market, with 80% of its business being foodservice.
“Overnight foodservice dropped off, almost 100%,” he says. “We literally lost 95% of our business overnight when everybody started shutting down; all the restaurants shut down and all the other foodservice operations started shutting down.”
When the shutdowns hit and the foodservice market came to a halt, retail demand boomed as consumers flooded grocery stores to stock up. Panic buying and overall demand caused runs on certain products and even temporary shortages, but as the new normal set in, demand started to decline from the peak because in many cases, consumers suddenly found themselves with more food than they knew what do with.
“People had already stocked up their pantries and their refrigerators and freezers, so retail business dropped off too,” says O’Malley. “I know a lot of people aren’t talking about that, but there was a significant drop-off in retail after the first month or so after everybody had completely inundated the retail locations and cleared the shelves.”
While the initial wave of buying was more of a “grab everything you can” mindset, consumer trends in purchasing have moved more toward foods that are healthier or possess immune-boosting properties. The “quarantine 15” may be a source of amusement on social media, but it’s also a real concern for consumers who suddenly couldn’t go to the gym or found themselves stuck at their desks at home with less real exercise options. According to Signals Analytics, vegetable-based versions of classic comfort foods, such as squash spaghetti, spinach gnocchi and cauliflower pizza crust, are growing in popularity as consumers look for healthier options. The company has also seen an increase in products that contain immune-boosting properties, such as probiotics, garlic, superfoods and hemp.
“Consumers are looking for ways to support their immune systems as they are extremely conscious of ways to avoid getting sick—whether it’s with COVID-19 or something else,” says Viezca. “For that reason, there has also been an uptick in popularity of beverages with immunity advantages, such as vitamin C, that boast claims around ‘all-natural’ or reducing allergy effects.”
SRG managing director and partner Amy Shipley agrees, noting that plant-based processors have seen significant increases in business as customers look for healthier alternatives.
“‘Immunity’ is certainly the topic du jour, so we expect to see that type of messaging both in the grocery aisles and away from home,” says Shipley.
The state of budgets
Budgets are following a similar trend to throughput. In 2019, more than half (52%) of respondents said their budgets for production, processing and packaging equipment were going up, with a mean increase of 21%. This year, only 38% of respondents say their budgets are going up, with a mean increase of 16%. Almost a quarter (22%) say their budget will go down, compared with only 8% in 2019.
The change was almost as drastic when it comes to automation and control hardware and software. In 2019, 33% said their budget was going up, while 62% said it would stay the same. This year, 22% say it will go up, while 16% say it will go down.
The most common expected purchase is lab analysis equipment, with 23% of respondents listing it. Digital sensors/transmitters (19%), plant control systems (18%), sanitation/CIP systems and/or software (16%) and wireless plant networking (16%) round out the top five.
One potential purpose that was mentioned more than once in the survey comments was a belief that processors will turn more to robotics to help navigate new safety protocols and staffing challenges. According to Cliff Cole, business development manager, ABB, safety is driving much of the decision-making around robotics, but it’s not solely confined to that.
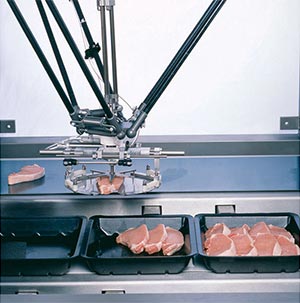
Photo courtesy of ABB
“What can we do to keep our employees safe? What can we do to keep our production safe, our food safe, our products safe?” says Cole. “They’re not only doing it because of the COVID requirements. They’re also doing it because they need to maintain competitiveness.”
Employee safety requirements and best practices during the ongoing pandemic are causing processors to rethink how they design and build future plants (see Food Engineering’s August cover story), but existing plants have to be retrofitted to meet employee safety needs as well. That can create challenges for facilities that don’t have much room for protective barriers or weren’t designed with social distancing in mind as part of the production line, and being able to integrate robotics can help.
“The robot doesn't care if there's a shield between one robot and another,” says Cole.
In addition to potential safety benefits, processors are also turning to robotics to help them keep up with competition, hit their production goals and keep their pricing in line with what their customers want.
“So it’s about keeping the people safe, keeping the food safe, keeping the environment safe, and then giving the speed and agility to get the products to consumers at the prices they need to allow those manufacturers to be competitive,” says Cole.
Structural changes and productivity needs
The most common structural change reported by respondents was conducting safety related training, with 53% of respondents mentioning it. That includes not only COVID-19 safety, but also training for categories such as HACCP or FSMA. “Changed a process” was reported by 40% of respondents, while expansions, renovations or added capacity were reported by 37%.
But one significant new addition was “changed elements of your supply chain,” with 31% of respondents choosing it. As demand surged in certain countries or areas as others were hit hard by the early stages of the pandemic, processors learned a lot about where the weaknesses were in their supply chains and had to figure out how to work around them.
In addition to those challenges, consumer interest in sustainable or local sourcing and lower carbon footprints is driving reevaluations of supply chains. Shipley of SRG says that food and beverage processors are looking at every step of their supply chains to see where they can improve, as well as looking at how products are developed.
Processors are evaluating their supply chains to respond to pandemic challenges and consumer demand for sustainability.
“Given the significant disruption in supply chains, we’re seeing sharper scrutiny on sourcing and in product development,” says Shipley. “Product development in new sustainable food sources and technology is huge, and consumers appear far more interested in and accepting of these new technologies.”
Two other popular responses to the structural changes question were “added a new line” and “added manufacturing staff,” both coming in at 29%, an indication of an increase in demand.
Demand surges and other manufacturing challenges are driving a need for greater productivity, and processors see a number of challenges to reaching that goal. The most common is equipment upgrades, cited by 82% of respondents. Skills training of line supervisors (76%) and skills training of line operators (73%) were the next most common responses, with improve maintenance systems at 68% and improve communication between manufacturing levels/areas cited by 65%.
Workforce changes
Food and beverage processors have struggled for years to hire, train and retain qualified employees. A surge in demand this year combined with possible worker shortages due to illness has only exacerbated the problem.
But this year adds a new wrinkle: An increase in the number of respondents who say their workforce has decreased compared with last year. Almost a quarter (22%) say their company’s workforce has decreased, compared with 16% in 2019. While a number of reasons were given in 2019 (half of 2019 respondents said “workers have left and the company has chosen not to replace them,” while 31% said “workers have left and we have been unable to find qualified replacements”), this year all respondents who gave a reason cited “decrease in output.”
Forty-two percent of respondents say their location is currently short-handed. Processors are using overtime to cover gaps.
When it comes to current staffing levels, 58% of respondents say they are at full staff, while 42% say they’re running shorthanded. For those who are understaffed and gave an answer to how their company is handling it, the unanimous answer was overtime. Forty-two percent say their company is increasing wages to attract employees, while 40% say they’re offering more training.
Staffing challenges are another driver of automation and robotics implementation, says ABB’s Cole, but there’s a perception issue at play.
“Probably one of the biggest challenges we have is that concept that robots are coming in here and they’re somehow taking people’s jobs,” he says. He points out that robotics don’t necessarily replace employees as much as they shift job duties or even lead to more hiring, because employees are needed to clean and maintain robotics.
Future trends in food and beverage manufacturing
Automation/robotics/AI is the most common answer from respondents when asked about what the future holds for food and beverage manufacturing trends, with 27% citing it. Efficiency/maintenance/new equipment is cited by 24%.
But tied for the top spot is COVID-19, with 27% citing it. More than 60 respondents left specific comments citing COVID-19 in one way or another. A small sample of those comments:
- New normal after COVID-19, which will have us modify the environment and processes to protect employee and customer health.
- COVID. Depends on how long it takes for it to go away. Will have lasting effects.
- Social distancing/automation.
- Increased contact-free interactions between equipment and personnel due to the COVID-19 virus.
- COVID impact over the long term. New reality and requirements and restrictions.
- Finding creative ways to market and sell foodservice products when the business has been down due to COVID-19.
It is clear that the ongoing pandemic is the No. 1 challenge facing food and beverage processors, and with no clear end in sight, it will continue to drive decision-making, forecasting and spending. Processors both large and small face challenges in responding to and adapting to the new normal, and those challenges will shape the future of the industry.
For more information:
Signals Analytics, www.signals-analytics.com
SRG, www.srg.com
ABB, www.abb.com/us
► See more State of Food Manufacturing reports
Clear Seas Research. 2020 Food Engineering State of Food Manufacturing, August 2020.
Clear Seas Research is a full service, B-to-B market research company focused on making the complex clear. Custom research solutions include brand positioning, new product development, customer experiences and marketing effectiveness solutions. Clear Seas offers a broad portfolio of primary, syndicated research reports and powers the leading B-to-B panel for corporate researchers, myCLEARopinion Panel, in the architecture, engineering, construction, food, beverage, manufacturing, packaging and security industries. Learn more at clearseasresearch.com.
To learn more about the report and purchase: https://www.clearseasresearch.com/product/2020-state-of-the-industry-food-manufacturing
Looking for a reprint of this article?
From high-res PDFs to custom plaques, order your copy today!